Bleche auf innovative Art verbinden
Die Erwartungen stets übertreffen
Geht es um das Verbinden von Blechen, so sind zahlreiche Lösungen denkbar. Punktschweißen und Kleben sind zwei mögliche Verfahren, die dafür in Frage kommen. Das Unternehmen Nimak hat diesbezüglich ein ganz besonderes Know-how zu bieten.
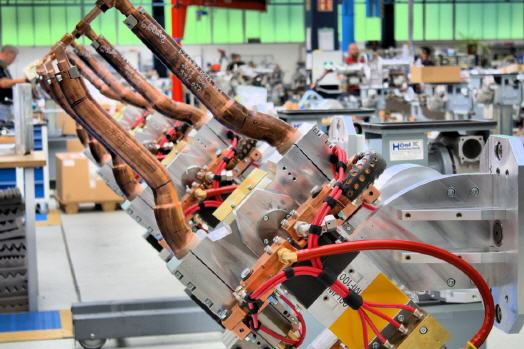
Um Bleche zu verbinden, gibt es zahlreichen Möglichkeiten, die vom Verschrauben und Vernieten über das Clinchen bis zum Verschweißen mit dem Laserstrahl reichen. Jedes dieser Verfahren hat Vorzüge, aber auch Nachteile. Es gilt daher, das zum Produkt passende Verfahren zu finden, um es kostenoptimal sowie ressourcenschonend anzufertigen. Dabei spielt die Stückzahl des zu produzierenden Teils ebenso eine Rolle wie dessen Montageart an andere Baugruppen. Nicht zu vergessen sind die Eigenschaften, die das Bauteil nach dem Fügen der Komponenten besitzen soll. Zu erwähnen wären hier beispielsweise Verzugs- und Spannungsfreiheit, weitgehende Sauberkeit der Oberfläche oder die Einhaltung von Maßtoleranzen.
Für das Verbinden von Blechen hat sich daher im Automobilbereich das Punktschweißen mit leistungsstarken Schweißzangen durchgesetzt, da dank dieses Verfahrens Karosserien in rascher Folge produziert werden können. Darüber hinaus wird nur wenig Wärme in die zu verbindenden Karosseriebleche eingebracht, was deren Verzug minimiert. Zu den Marktführern in Sachen Schweißzangen zählt ohne Zweifel das deutsche Unternehmen Nimak, das sich bereits seit 1965 mit den Herausforderungen des Widerstandsschweißens beschäftigt.
Heute verfügt das Unternehmen über ein umfangreiches und leistungsstarkes Sortiment an Schweißzangen, aus dem sich Automobilhersteller, aber auch andere Branchen, zum Beispiel die Luft- und Raumfahrt, Metallbearbeitung sowie Konsumgüterunternehmen, gerne bedienen. Dank eines Baukastensystems können rasch individuelle Schweißzangen produziert werden, die mühelos die Vorgaben der jeweiligen Werksnormen erfüllen.
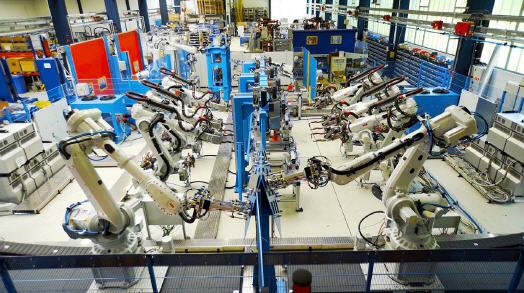
Variable Plattform
Auf der Grundlage dieses Erfahrungsschatzes hat Nimak die Plattform ›Multiframegun‹ für Roboter-Schweißzangen entwickelt. Dank dieses modularen Baukastensystems lassen sich auf einer stets gleichen Trägerplatte fünf unterschiedliche Module montieren, die es wiederum in vielen Varianten für unterschiedlichste Einsatzzwecke gibt. Mit diesem variantenreichen System können sowohl X- als auch C-Zangen wesentlich schneller und kostengünstiger produziert werden. Mit dem Meilenstein ›Magneticdrive‹ werden die Nimak-Schweißzangen und Schweißmaschinen noch leistungsstärker.
Dies ist eine neuartige Krafterzeugungs- und Nachsetzeinheit, die mittels eines Elektromagneten einen sehr präzisen und sanften Kraftaufbau besitzt und auch Kraftprofile in Millisekunden realisieren kann. Das mit diesem System mögliche kontrollierte Nachsetzen führt zu deutlich besseren Punkt- und Buckelverschweißungen. Zudem wird damit selbst im Fall schlecht schweißbarer Stähle sowie bei Aluminium eine zuverlässige Fügeverbindung erreicht.
Praktiker kennen die Probleme, die beim Schweißen von Aluminium entstehen: In aller Regel ist ein Schutzgas – beispielsweise Argon – nötig, damit sich der Luftsauerstoff nicht mit der Aluminiumschmelze verbindet, was ein zuverlässiges Fügen durch die sich bildende Oxidschicht verhindern würde. Beim Punktschweißen unter Zuhilfenahme von Magneticdrive ist dies jedoch nicht nötig, da mit dieser Technik die Schweißzange per Magnetkraft schnell nachgesetzt wird, wenn durch den Stromstoß die Schmelze entsteht.
Der Schweißpunkt ist dank dieses cleveren Systems sauber und stabil ausgeführt, es entsteht eine gleichmäßige Schweißlinse, frei von Heißrissen und Porenbildung. Doch das ist noch nicht alles, was auf der Haben-Seite des Magneticdrive verbucht werden kann: Stimmt die Stückzahl eines zu produzierenden Teils, so sollte dessen Einsatz dort geprüft werden, wo bisher ein anderes Schweißverfahren herangezogen wurde.
Beispielhaft soll das Fügen eines Anschlussstutzens für ein Kfz-Teil erwähnt werden. Im Vergleich zum Schweißen per MIG-Anlage ist das Widerstandsschweißen dieses Teils mit Magneticdrive-Unterstützung wesentlich schneller. Sogar der Roboter kommt da nicht hinterher, wenn dieser das gleiche Teil per Laser verschweißt. Viele Schweißaufgaben sind durch Magneticdrive von Nimak lösbar geworden oder können in wesentlich kürzerer Zeit durchgeführt werden.
Doch das Unternehmen hat noch viel mehr zu bieten. So bietet es neben seinen Schweiß-Innovationen auch eine Dosierlösung für den robotergestützten Klebstoffauftrag an. Dies ist ein Schritt in die Zukunft, da durch den Trend zur E-Mobilität leichtere Kraftfahrzeuge benötigt werden, weshalb sehr viele verschiedene, teilweise nicht mehr schweißbare Bauteile zum Einsatz kommen.
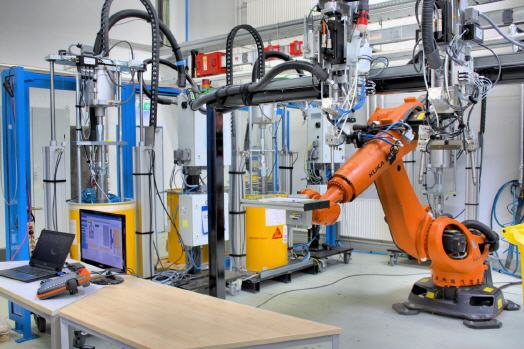
Ausgefeilte Technik
Die dahinterstehende Technik ist äußerst ausgefeilt, geht es doch darum, trotzt höchstem Auftragstempo von rund 500 Millimetern pro Sekunde einen gleichmäßigen Klebstoffauftrag mit gleichbleibender Raupenbreite zu erzeugen. Mit der von Nimak entwickelten Dosiertechnik ist es sogar möglich, in rascher Folge unterbrochene Klebstoffraupen – sogenannte Steppnähte – zu erzeugen, zwischen denen Schweißpunkte gesetzt werden können. Auf diese Weise sind Leichtbauteile aus Aluminium produzierbar, die geklebt und zugleich punktgeschweißt sind. Dies hat im Fall eines Fahrzeugs insbesondere beim Crashverhalten durch eine höhere Stabilität große Vorteile.
In der Großserienfertigung sind natürlich beträchtliche Mengen an Klebstoff nötig, um möglichst viele Teile ohne Stillstandzeit verkleben zu können. Diese werden in bis zu 200 Liter fassende Fässern angeliefert und über eine Pumpe zum Dosierventil gepumpt. Da sich Klebstoff im Anlieferzustand schwer fördern lässt, wird dieser zunächst erwärmt, damit er eine dünnflüssigere Konsistenz annimmt, sich dadurch leichter pumpen lässt. Damit dies auf dem Weg zum Dosierventil so bleibt, sind zusätzlich die Schläuche beheizt. In der Dosierkammer angekommen, wird der Klebstoff mit rund 500 Millimeter pro Sekunde auf das zu verklebende Bauteil aufgetragen.
Damit sichergestellt ist, dass trotz diesen hohen Tempos stets ein gleichmäßiger Klebstoffauftrag in der gewünschten Menge erfolgt, ist raffinierte Technik nötig. Die Herausforderung ist, dass die gewünschte Klebstoffmenge bei jeder Verfahrgeschwindigkeit des Roboters konstant bleiben muss. Im Fall einer spiralförmigen Klebung ändert sich die Geschwindigkeit sogar kontinuierlich, daher muss die Klebstoffmenge ebenfalls laufend angepasst werden.
Damit dies klappt, wird der vom Fass mit einem Druck von rund 150 bis 300 bar kommende Klebstoff im Dosiersystem zunächst in ein Einlassventil geleitet, das von einem servogesteuerten Schieber bedarfsgerecht geschlossen und geöffnet werden kann. Von dort wird der Klebstoff in eine Dosierkammer geleitet, wo ein ebenfalls servomotorisch gesteuerter Kolben den Klebstoff mit 20 bis 300 bar in das eigentliche Auslassventil drückt, das von einer steuerbaren Nadel verschlossen wird.
Diese Nadel steuert den Klebstofffluss. Durch deren Steuerbarkeit kann das Ventil in rascher Folge geöffnet und geschlossen werden, sodass mühelos bei jeder Robotergeschwindigkeit die schon angesprochenen Steppnähte ebenso erzeugt werden können, wie ununterbrochene Raupen. Damit diese stets eine gleichmäßige Dicke bekommen, ist ein fein abgestimmtes Zusammenspiel zwischen Schieber und Kolben nötig, um den Klebstofffluss stufenlos zu regulieren. Dank moderner Servotechnik ist diese Herausforderung sicher beherrschbar.
Dieses große Know-how in Sachen ›Schweißen‹ und ›Kleben‹ hat Nimak gebündelt und bietet komplett automatisierte Einzelstationen, aber auch ausgewachsene Roboterzellen an, die nach Kundenwunsch gestaltet sind. Abgesehen davon, sind von Nimak selbstverständlich auch manuell bedienbare Schweißgeräte und Schweißzangen zu bekommen. Dieses große Produktspektrum erlaubt es, jeden Kundenwunsch zu erfüllen. Und da die Fertigungstiefe außergewöhnlich groß ist, sind unliebsame Überraschungen durch Mängel oder gar dem Ausbleiben von Zulieferteilen kein Thema.
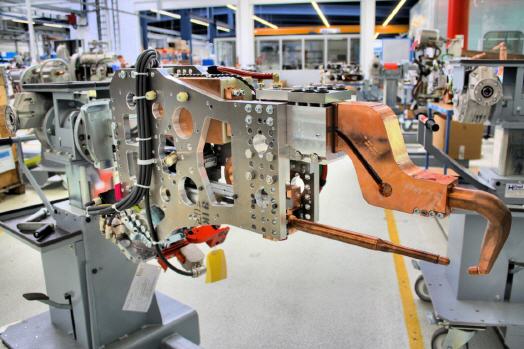
Qualität vom Experten
Besonders hervorzuheben ist, dass Nimak ein Auge darauf hat, bewegte Teile möglichst leicht auszuführen. Deshalb kommen, wo immer möglich, keine schweren Gussteile für die Schweißzangen und die Dosiersysteme zum Einsatz, sondern wird massives Aluminium-Rohmaterial verwendet, das in der eigenen Zerspanungsabteilung zu den einzelnen Bauteilen veredelt wird. Eigene Prüfstände sorgen dafür, dass ausschließlich perfekt funktionierende Komponenten den Weg in die Montage finden.
Kein Wunder, dass sich angesichts der herausragenden Qualität viele Hersteller hochwertiger Erzeugnisse auf Nimak-Produkte verlassen. Diese sind in der Vorserienproduktion der neuen Mercedes S-Klasse ebenso zu finden wie in der vollautomatischen Fertigung von Gerüstbauteilen eines namhaften deutschen Herstellers. Der Nimak-Slogan ›Erwartungen übertreffen‹ ist eben Programm.
Mehr Informationen zur NIMAK GmbH:
![]() |
NIMAK GmbH |
![]() |
Frankenthal 2 |
![]() |
57537 Wissen |
![]() |
Tel.: Tel.: +49 2742 7079-0 |
![]() |
E-Mail: info@nimak.de |
![]() |
www.nimak.de |
War dieser Artikel für Sie hilfreich?
![]() |
![]() |
![]() |
![]() |
![]() |
Bitte bewerten Sie diese Seite durch Klick auf die Symbole.
Zugriffe heute: 2 - gesamt: 10364.