Die Zukunft steckt im Pulver
Laserschmelzen als Zerspanungsalternative
Das regenerative Erstellen von Werkstücken aus festen, flüssigen oder pulverförmigen Stoffen schreitet mit Siebenmeilenstiefeln voran. Wir erleben derzeit eine Revolution, die wohl nur mit der Erfindung der Dampfmaschine vergleichbar ist. Wie damals gibt es Schrittmacher, die den Takt der Innovationen vorgeben. Das Unternehmen SLM ist ganz vorne zu finden, wenn es um diese Technik geht.
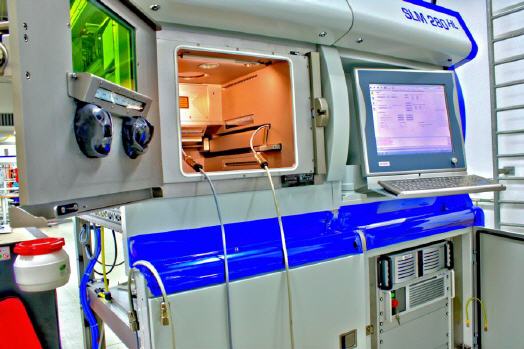
Die 3D-Drucktechnik ist schon lange den Kinderschuhen entwachsen und schickt sich an, in großem Stil die Art, wie Werkstücke hergestellt werden, auf eine völlig neue Basis zu stellen. Schon heute ist es möglich, regenerativ hochbelastbare Bauteile für Flugzeugtriebwerke herzustellen, die den Eigenschaften von herkömmlichen Bauteilen, die durch Drehen, Fräsen und Erodieren entstanden, in nichts nachstehen. Weder in der Zugfestigkeit noch in der Druckfestigkeit oder Elastizität gibt es große Abweichungen. Lediglich die Dichte regenerativ hergestellter Bauteile ist ein wenig geringer, da technikbedingt eine Neigung zur Porosität gegeben ist, was jedoch vielfach kein Nachteil, sondern eher als Vorteil im Hinblick auf Gewichtseinsparungen zu werten ist.
Mittels der 3D-Drucktechnik werden plötzlich Lösungen sichtbar, die früher als unlösbar oder nur als sehr aufwendig umsetzbar galten. Beispielsweise ist es ab sofort eine leichte Übung, neue Flügelformen für Flugzeuge auszutüfteln, da Modellflügel problemlos mit den nötigen Hohlräumen, Rohren und Bohrungen versehen werden können, um die Drücke beim Umströmen des Flügels messen zu können. Da es keine Grenzen bezüglich der Bauteilgeometrie mehr gibt, kann die 3D-Drucktechnik auch in den Bereichen Schmuck, Design, Medizin oder Forschung punkten.
Sogar im Raumfahrtbereich gibt es visionäre Überlegungen, den extrem feinen Mondsand, auch Regolith genannt, zu Nutzen, um daraus mittels 3D-Drucktechnik die Behausung für Mondexpeditionen zu Drucken. Auf diese Weise würden gewaltige Menge Baumaterial eingespart, die man sonst via Transporter zum Mond verfrachten müsste, was gewaltige Kosten bedeuten würde. Schließlich kostet es 10.000 Dollar, ein Kilogramm Nutzlast in den Weltraum zu transportieren.
Für irdische Anwendungen ist das Unternehmen SLM eine erste Adresse, wenn es um hochwertige Teile geht, die per Laserschmelzen hergestellt werden sollen. Beim Laserschmelzen wird Metallpulver in feinen Schichten aufeinandergelegt und jede Schicht gezielt an ausgewählten Stellen mit einem 50 bis 150 Mikrometer im Durchmesser messenden Laserstrahl auf 1700 Grad Celsius erhitzt, sodass dort das Metallpulver schmilzt und sich mit der darunterliegenden Schicht verbindet.
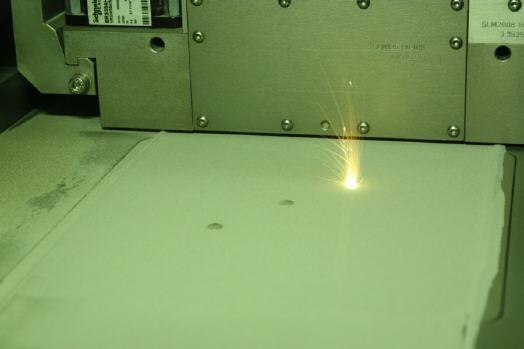
Der YLR-Faserlaser, der je nach Anlagenmodell eine Leistung zwischen 100 und 1000 Watt besitzt, legt dabei ein gehöriges Tempo vor. Mit drei bis sieben Meter pro Sekunde huscht er über das Metallpulver. Nur wenige Augenblicke reichen, um es auf Schmelztemperatur zu erhitzen. Sobald der Laser weitergewandert ist, kühlt sich das Pulver an der erhitzten Stelle mit etwa 1500 Grad pro Sekunde ab, sodass das Material praktisch unmittelbar nach Verlassen des Laserstrahls an der eben noch flüssigen Stelle fest wird.
Auf diese Weise entstehen in einem passablen Tempo Teile, die sich anschließende für den harten Alltagseinsatz verwenden lassen. Sie können sogar gehärtet und geschliffen werden, wenn das dazu passende Pulver verwendet wird. Und was für die Ressourcenschonung ganz wesentlich ist: Mittels Laserschmelzen können im Vergleich zu zerspanenden Verfahren zwischen 30 und 40 Prozent Material eingespart werden. Dazu kommen noch Einsparungen durch nicht benötigte Kühlschmierstoffe, die in aller Regel Beschaffungs-, Lager-, Pflege- und Entsorgungskosten auslösen.
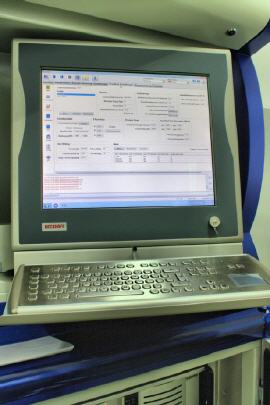
Was jedoch kräftig zu Buche schlägt, ist das Pulver, das in einem aufwendigen Herstellungsprozess bei spezialisierten Unternehmen erzeugt wird. Je nach Pulverart reicht der Preis von 50 bis über 500 Euro für nur ein Kilogramm des begehrten Materials, wobei der Alu-Preis mit etwa 122 Euro pro Kilogramm noch im unteren Bereich zu finden ist. Kein Wunder, dass die Konstrukteure von 3D-Teilen besonderes Augenmerk auf ausgefeilten Leichtbau legen, sollen diese Teile per Laserschmelzen hergestellt werden.
Nach der Konstruktion gilt es, das 3D-Teil für den 3D-Druck aufzubereiten. Dazu werden durch das Teil hauchdünne Schnitte gelegt, deren Schnittflächen die Wege darstellen, die später der Laserstrahl abschreitet. Die Erzeugung dieser Schichten übernimmt die Software ›Magics AutoFab‹, die SLM seinen Anlagen serienmäßig beilegt. Dazu werden Dateien im STL-Format an das System übergeben, das daraus die einzelnen Schichten berechnet.

SLM ist derzeit der einzige Hersteller, der mehrere Laserquellen in seinen Anlagen gleichzeitig einsetzen kann. Dadurch wird die Fertigungszeit für das herzustellende Teil massiv verkürzt, was sich in aller Regel natürlich auch bei den Stückkosten positiv bemerkbar macht. Dazu kommt, dass bei Betrachtung aller Faktoren die Lasersintertechnik weit besser abschneidet als zerspanende Verfahren, wenn es um den Energieeinsatz pro Bauteil geht. Auch das einzusetzende Material ist in dieser Betrachtung mit einem positiven Beitrag beteiligt, da nicht verwendetes Pulver nach kurzer Aufarbeitung direkt wieder verwendet werden kann. Lediglich fünf Prozent des Pulvers wird unbeabsichtigt immer wieder ausgetragen und muss ersetzt werden.
Das Laserschmelzen ist eine unschlagbar schnelle Möglichkeit, wenn es darum geht, rasch einen Prototypen in Händen zu halten, um die Tauglichkeit einer Konstruktion in der Praxis zu testen. Dazu können in den SLM-Anlagen sogar zwei Pulverarten gleichzeitig eingesetzt werden, was Werkstücke ermöglicht, die auf herkömmliche Art überhaupt nicht machbar sind. Doch auch die Auswahl unter den verschiedenen Pulvern ist am Wachsen. Mittlerweile kann man Bauteile aus Titan, Aluminium, Werkzeug- und Edelstahl, Kobalt-Chrom, Inconel und vielen anderen, zu Pulver vermahlene Materialien herstellen. Das Endergebnis unterscheidet sich, wie erwähnt, nur marginal vom auf zerspanende Art erzeugten Gegenstück.
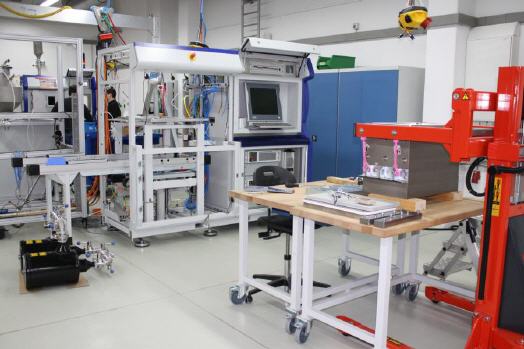
Damit der Pulverauftrag nicht zum Flaschenhals wird, haben die SLM-Konstrukteure ihren Anlagen eine Pulverauftragsvorrichtung spendiert, die in beiden Richtungen arbeitet und so ohne das sonst übliche Zurückfahren des Schlittens auskommt. Natürlich ist beim Umgang mit Pulver stets besondere Umsicht vonnöten. Feiner Pulverstaub neigt besonders gerne zum Entzünden, was schon bei Mehlstaub der Fall ist, wie Explosionen in Getreidemühlen dokumentieren.
Wenn nun noch ein heißer Laserstrahl über Pulver huscht, ist die Gefahr einer Explosion extrem hoch. Aus diesem Grund wird die Luft aus der Arbeitskammer abgepumpt und an dessen Stelle das Gas Argon zusammen mit Stickstoff eingefüllt, bis nur mehr eine Restsauerstoffkonzentration von 0,01 Prozent in der Arbeitskammer vorhanden ist. Diese Gase garantieren, dass sich nicht versehentlich das Metallpulver entzünden kann, was besonders bei Aluminium der Fall wäre.
Nachdem ein Werkstück erstellt wurde, gilt es, das überschüssige Pulver, das nicht für den Bau benötigt wurde, zu entfernen. Zu diesem Zweck werden Staubsauger verwendet, die das abgesaugte Pulver in ein Wasserbad leiten, um jede Gefahr einer Explosion, beispielsweise durch elektrostatische Aufladung, zu eliminieren. Es zeigt sich also, dass das generative Erzeugen von Werkstücken ein wenig anders abläuft. In jedem Fall werden jedoch Werkstücke auf besonders effektive Art erstellt.
Wer weiß, womöglich dauert es gar nicht mehr lange, bis diese Technik künftigen Mondexpetitionen ein Dach über den Kopf lasert. Dazu wäre nicht einmal die Erzeugung eines Vakuums wegen der Ex-Gefahr nötig, da dieses im Weltraum bereits vorhanden ist. Goldene Zeiten also für künftige Mondsiedler, die sich dort oben sogar ihr Werkzeug problemlos drucken könnten.
Mehr Informationen zur SLM Solutions GmbH:
![]() |
SLM Solutions GmbH |
![]() |
Roggenhorster Straße 9c |
![]() |
23556 Lübeck |
![]() |
Tel.: 0451 / 16082 -273 |
![]() |
Fax: 0451 / 16082 -250 |
![]() |
E-Mail: info@slm-solutions.com |
![]() |
www.slm-solutions.com |
War dieser Artikel für Sie hilfreich?
![]() |
![]() |
![]() |
![]() |
![]() |
Bitte bewerten Sie diese Seite durch Klick auf die Symbole.
Zugriffe heute: 9 - gesamt: 13338.