Mit Druckluft zu mehr Effizienz
Atlas Copco unterstützt Anwender bei der Analyse
Wer ein Energiemanagementsystem einführt, spart auf mehreren Ebenen. Zum einen locken Steuersenkungen und eine Reduzierung der EEG-Umlage, zum anderen lässt sich der Energieverbrauch mit Maßnahmen zur Effizienzsteigerung im Schnitt um 30 Prozent senken. Diese Maßnahmen sind zum Teil förderfähig, wie etwa eine Modernisierung der Druckluftversorgung. Atlas Copco unterstützt Anwender bei der Ist-Analyse sowie der Erstellung effizienter Konzepte.
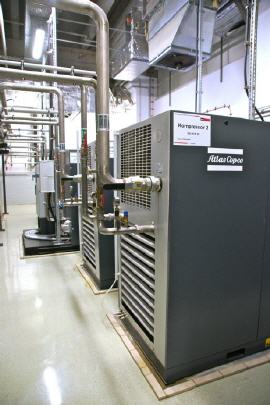
Die Themen Energiemanagement nach ISO 50001 und Energieaudits gemäß EN 16247 stehen bei vielen unserer Kunden auf der Tagesordnung“, erklärt Karsten Decker, Teamleiter Energieberatung bei Atlas Copco in Essen. „Dabei spielt die Druckluft eine wichtige Rolle; denn mit einer zeitgemäßen, effizienten Druckluftversorgung können wir erheblich dazu beitragen, die gesteckten Energiesparziele zu erreichen.“
Das Kyoto-Protokoll sieht eine Reduktion der CO2-Emissionen um 40 Prozent bis zum Jahr 2020 (im Vergleich zu 1990) vor. Um diese Forderung umzusetzen, sind alle Nicht-KMU (Unternehmen mit mehr als 250 Mitarbeitern oder 50 Millionen Euro Umsatz) seit dem 5. Dezember 2015 dazu verpflichtet, ein Energieaudit durchzuführen oder ein Energiemanagementsystem zu etablieren.
Mit letzterem verpflichtet sich das Unternehmen, im Rahmen eines kontinuierlichen Verbesserungsprozesses Energieeinsparungen voranzutreiben. Jährlich sollen neue Einsparmöglichkeiten aufgedeckt und umgesetzt werden. „Die Ziele beider Systeme sind für die Bundesregierung ganz klar die Verringerung der CO2-Emissionen“, erklärt Decker. „Und weil das ohne gewisse Anreize nicht zu schaffen ist, hat die Regierung das Energiemanagementsystem und das Audit zur Bedingung dafür gemacht, dass Unternehmen Steuerreduzierungen und andere Vergünstigungen in Anspruch nehmen können.“
EEG-Umlage ist an Energiemanagement oder Energie-Audit gekoppelt
So ist beispielsweise die teilweise Rückerstattung der EEG-Umlage an die Einführung eines Energiemanagementsystems oder eines Energie-Audits gekoppelt. „Die EEG-Umlage betrug für das Jahr 2017 6,88 Cent pro Kilowattstunde und kann ab der ersten Gigawattstunde um 85 Prozent reduziert werden“, erläutert Decker. „Damit können auch mittlere Unternehmen schon rund 60.000 Euro pro Jahr einsparen.“ Aber auch Unternehmen, die jährlich weniger als eine Gigawattstunde (1 GWh = 1 Million kWh) an Strom benötigen, könnten laut Decker von einem Energieaudit oder Energiemanagementsystem profitieren, indem sie Energieverbrauch und Kosten reduzieren, ihre Außendarstellung mit Audit-Zertifikaten bei Geschäftspartnern verbessern und dadurch ihre Wettbewerbsfähigkeit steigern.
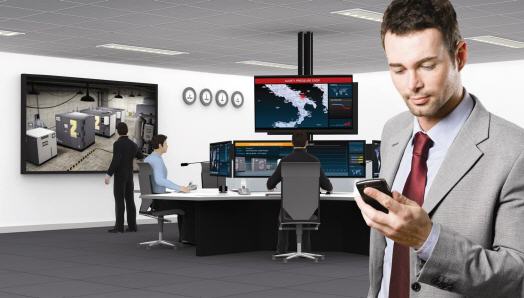
„Die Systeme eignen sich auch für kleine und mittlere Unternehmen“, betont Karsten Decker. Dabei empfehle sich das Energie-Audit für kleine oder Kleinstunternehmen. „Beim Audit wird nur der Ist-Zustand erfasst, also die verbrauchte Energie für die unterschiedlichen Unternehmensbereiche“, erläutert er. „In einer Lackiererei mit 100 Mitarbeitern, die vom Umsatz her noch als KMU gilt, würde sich bereits ein Energiemanagementsystem bezahlt machen.“ Erst, wenn man Energieverbräuche erkannt und aufgeschlüsselt habe, wo die Energie hingehe, könne man über Einsparmöglichkeiten nachdenken. Diese könnten die Modernisierung der Beleuchtung sein, der Austausch von Pumpen und Motoren oder die Optimierung der Druckluftversorgung.
Bis zu 30 Prozent Einsparungen sind nach Deckers Erfahrungen realistisch, wenn das Energiemanagementsystem im Unternehmen „gelebt“ wird. Im Durchschnitt seien ohne größere Investitionen kurzfristig etwa 10 % an Einsparungen möglich. „Diese Reduzierung erreiche ich durch ein verändertes Verhalten meiner Mitarbeiter, durch veränderte Einstellungen an den Anlagen und gegebenenfalls durch eine moderate Modifizierung von Prozessen“, erklärt Decker. „All diese Dinge kann man relativ schnell umsetzen. Sie wirken sich direkt positiv auf den Energieverbrauch aus.“
Effizientere Druckluftversorgung von der Erzeugung bis zu den Verbrauchern
Wenn die Modernisierung des Druckluftsystems ansteht, gibt es viele Ansatzpunkte, um die Effizienz zu verbessern. Nicht nur Erzeugung und Aufbereitung müssen betrachtet werden, sondern auch die Druckluftverteilung und die verschiedenen Abnehmer. Hier gilt es zu prüfen, ob die Maschinen tatsächlich den anliegenden Überdruck benötigen oder mit einem geringeren Wert arbeiten könnten. Auch die Optimierung des Druckluftnetzes bezüglich Materialauswahl und Dimensionierung lohnt sich häufig: Sie vermeidet Druckverluste und senkt damit den Energieverbrauch. „Bei der Auslegung der Druckluftverteilung ist es wichtig, unnötige Bögen und Verjüngungen zu vermeiden und dass der Durchmesser stimmt“, erläutert Decker. „Es ist nicht sinnvoll, die Druckluft mit hocheffizienten Maschinen zu erzeugen, sie dann aber in ein altes, falsch dimensioniertes Rohrleitungsnetz abzugeben, das vielleicht auch noch Ablagerungen aufweist und mit einer Sternverteilung statt einer Ringleitung arbeitet.“ Denn das erzeuge einen hohen Druckverlust und sei eben nicht effizient.
Viele Verluste kommen auch durch Leckagen im Druckluftnetz zustande. Mit speziellen Ortungsgeräten können diese schnell und sicher aufgespürt und anschließend verschlossen werden. Eine weitere Möglichkeit zur Effizienzsteigerung ist die Druckabsenkung sowie die Realisierung eines engeren Druckbandes, sprich eine Reduzierung der Druckschwankungen. Dies kann durch Einsatz einer übergeordneten Steuerung erreicht werden. „Darüber hinaus kann ich Phasen mit einer geringeren Auslastung identifizieren, in denen ich dann über eine Zeitschaltuhr den Druck absenke“, ergänzt Decker. Last but not least seien der Einsatz moderner Erzeugungs- und Aufbereitungstechnik sowie eine Wärmerückgewinnung zu empfehlen, um Energie zu sparen.
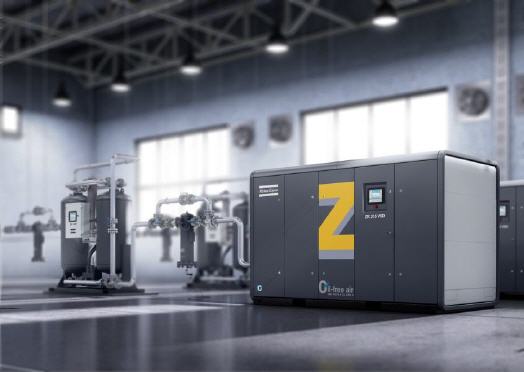
Das Technologie-Portfolio von Atlas Copco reicht von hocheffizienten drehzahlgeregelten Kompressoren und Trocknern über Systeme zur Energierückgewinnung und übergeordnete Steuerungen bis hin zum Rohrleitungssystem AirNet, das auf eloxierten Aluminiumkomponenten basiert. Der Anwender profitiert von einer schnellen und einfachen Installation, einem leckagefreien Betrieb sowie einem niedrigen Reibwert und entsprechend geringen Druckverlusten.
Darüber hinaus bietet Atlas Copco verschiedene Dienstleistungen an, mit denen ebenfalls an der Effizienzschraube Druckluft gedreht werden kann. „Mit dem sogenannten AirScan analysieren wir ein vorhandenes Druckluftsystem, wir identifizieren Schwachstellen und besondere Ereignisse, die energetisch kritisch sind“, beschreibt Karsten Decker eines der Instrumente. „Wir zeigen, mit welchem Druck gefahren wird und welcher Druck an bestimmten Verbrauchern anliegt, wie viel Energie die Kompressoren ziehen und – ganz wichtig – welcher Volumenstrom in welchen Teilbereichen benötigt wird, damit der Verbrauch auf die verschiedenen Kostenstellen aufgeteilt werden kann.“ Der AirScan wird häufig im Vorfeld der Auslegung von Neuanlagen genutzt, aber auch um mehr Informationen über ein vorhandenes Druckluftnetz zu erhalten. Außerdem hilft er, ein Energieaudit zu bestehen, indem die einzelnen Druckluftverbräuche sowie deren Entwicklung dokumentiert werden.
Ein weiteres Produkt zur Effizienzsteigerung ist der Service Smartlink Energy. Das internetbasierte Datenüberwachungsprogramm unterstützt den Anwender dabei, einen besseren Überblick über den individuellen Wartungsbedarf seiner Druckluftanlage zu erhalten, die Produktion verfügbar zu halten und den Energieverbrauch – und damit die Betriebskosten – so weit wie möglich zu senken.
„Smartlink Energy benachrichtigt den Anwender über den Zustand seiner Kompressoren sowie über Störungen“, erläutert Decker. „Auf Kundenwunsch analysieren wir auch die Maschinendaten und können Optimierungsmöglichkeiten aufzeigen. Beispielsweise, wenn eine Maschine plötzlich mehr Energie als gewöhnlich verbraucht, wenn die Auslastung eines Kompressors eine Wärmerückgewinnung empfiehlt oder wenn aufgrund der Anzahl der Leerlaufstunden eine übergeordnete Steuerung sinnvoll wäre.“
Smartlink Energy dokumentiert alle Messwerte
Hat das Unternehmen bereits ein Energiemanagementsystem etabliert, können zudem die geforderte Visualisierung, Datenaufzeichnung und Dokumentation über Smartlink Energy erfolgen. „Das System erzeugt einen Bericht, der direkt im Energiemanagementsystem als Report genutzt werden kann“, erklärt Decker. „Über die Lizenz für Smartlink Energy hat das Unternehmen Zugriff auf einen externen Server, auf dem die aufbereiteten Daten individuell abgerufen werden können.“
Für Unternehmen, die ihre Daten nicht aus dem Haus geben möchten, stellt Atlas Copco das System Smart2LAN für eine lokale Datenspeicherung und Visualisierung auf dem Kundenserver zur Verfügung. „Hierbei können wir den Kunden natürlich nicht aktiv benachrichtigen“, gibt Karsten Decker zu bedenken. „Er ist in diesem Fall selbst in der Pflicht, die Anlagendaten zu betrachten, auszuwerten und zu analysieren.“
Vom Start der Planung bis hin zur Inbetriebnahme der Druckluftanlage und zum anschließenden Service steht Atlas Copco seinen Kunden beratend zur Seite. „Nach einem Vorgespräch vor Ort beginnen wir mit der Analyse, das heißt mit dem AirScan“, beschreibt Karsten Decker den Ablauf. „Es folgen die Auswertung der ermittelten Daten und die Präsentation der Ergebnisse. Daraus leiten wir einen Maßnahmenplan ab und fixieren die Ziele.“ Der Kunde erhält Empfehlungen zur Modifikation der vorhandenen Technik und zu Neuanschaffungen. „Die Effizienz spielt dabei eine wichtige Rolle“, betont Decker, „aber die Betriebssicherheit muss immer noch an oberster Stelle stehen.“
Gut beraten von der Planung bis zur Inbetriebnahme
Wird die Effizienz mit der Neuanlage deutlich gesteigert, lohnt auch ein Blick auf mögliche Fördergelder. So hat die Bundesregierung einen Energieeffizienzfonds zur Förderung der rationellen und sparsamen Energieverwendung aufgelegt. Auf dessen Grundlage werden hocheffiziente Querschnittstechnologien über das Bundesamt für Wirtschaft und Ausfuhrkontrolle (BAFA) gefördert. Das Programm, das zunächst kleinen und mittleren Unternehmen vorbehalten war, richtet sich seit seiner Aktualisierung im Mai 2016 an Gewerbe- und Industriebetriebe aller Größenklassen mit einer Betriebsstätte oder Niederlassung in Deutschland sowie an Energiedienstleister. Die neue Förderrichtlinie gilt bis Ende 2019.
Eine weitere Neuerung in der aktuellen Fassung ist die Förderung hocheffizienter Systeme. „Anfangs gab es nur eine Förderung für Einzelmaßnahmen. So wurden beispielsweise hocheffiziente Kompressoren gefördert, bei denen ein maximaler Energieverbrauch pro Kubikmeter Luft festgeschrieben ist“, erklärt Decker. „Außerdem gab es finanzielle Unterstützung für übergeordnete Steuerungen bei Stationen mit mehreren Kompressoren oder für Wärmerückgewinnungsmodule, wenn die Bedingungen erfüllt wurden.“
Förderung für Einzelmaßnahmen und effiziente Gesamtsysteme
Seit 2016 sind nun auch Druckluftsysteme förderfähig. Dabei wird nicht auf die Effizienz der einzelnen Komponenten geschaut, sondern das Gesamtsystem betrachtet. Dieses muss nach der Modernisierung mindestens 25 % an Energie einsparen. „Hier können auch Kompressoren gefördert werden, die als Einzelmaßnahme nicht zulässig wären“, erläutert Decker. „Wenn in Verbindung mit einer übergeordneten Steuerung, einer Wärmerückgewinnung oder einem veränderten Rohrleitungssystem die 25 Prozent erreicht werden, ist die Maßnahme förderfähig.“ Durch diese Änderung sei es nun beispielsweise möglich, ölfrei verdichtende Kompressoren von Atlas Copco als Bestandteil eines Gesamtsystems fördern zu lassen. Für eine Einzelförderung wären sie dagegen trotz ihrer hohen Energieeffizienz nicht zugelassen. Dies liegt an ihrer speziellen Technologie, die nicht im Kriterienkatalog aufgeführt ist.
Auch als Einzelmaßnahme förderfähig sind unter anderen die öleingespritzten drehzahlgeregelten Kompressoren aus den Reihen GA VSD und GA VSD+ sowie die Wärmerückgewinnungsmodule von Atlas Copco. Der Hersteller unterstützt seine Kunden sowohl bei der Konzeption eines förderfähigen Komplettsystems als auch bei den Vorbereitungen für eine Antragstellung. Denn wer für ein neues Druckluftsystem eine Förderung beantragen möchte, muss zunächst eine Bestandsaufnahme machen, auf deren Basis ein Konzept zur Energieeinsparung oder Abwärmenutzung erstellt wird. Diese Ist-Analyse wird entweder von einem externen Energieberater durchgeführt oder – wenn das Unternehmen bereits ein Energiemanagementsystem etabliert hat – vom internen Energiebeauftragten.
Für beide kann dies schwierig sein, wenn sie nicht über das nötige Know-how und/oder die nötigen Messmittel verfügen. „Deshalb stellen wir dem externen Berater oder dem internen Experten unsere Dienstleistung zur Verfügung und führen mit kalibrierten und zertifizierten Messmitteln und nachvollziehbaren Messkatalogen die Ist-Aufnahme durch“, erläutert Karsten Decker. „Um das Energieeinsparungskonzept zu erstellen, muss bekannt sein, wie viel das aktuelle System verbraucht, denn nur so kann man die eingesparten 25 Prozent nachweisen.“
Dieser Nachweis der Energieeinsparung ist die nächste Voraussetzung für die Förderung. „Hier kann man sich zwischen der Vorlage der Gerätedaten oder einer Messung entscheiden, wobei letztere wesentlich aussagekräftiger ist“, weiß Decker. „Die meisten Kunden lassen daher den Verbrauch nachmessen. Oder sie haben permanente Messgeräte eingebaut, über die sie den Verbrauch selber mitschreiben und kontrollieren können.“
Beispiel aus der Praxis: Papierhersteller spart monatlich 100000 kWh
So verfährt beispielsweise die Propapier GmbH in Burg bei Magdeburg. Das Unternehmen stellt jährlich über eine Million Tonnen Wellpappenrohpapiere her und benötigt Druckluft in zwei Qualitäten. Mit neuen Atlas-Copco-Kompressoren und einem Versorgungskonzept mit zwei Netzen spart Propapier nun monatlich 100000 kWh elektrische Energie.
Schon vor der Installation der neuen Anlage wurde eine Online-Messung eingerichtet, so dass der Druckluftverbrauch kontinuierlich gemessen und im Betriebsleitsystem dokumentiert werden kann. Auch die monatlichen Stromverbräuche der einzelnen Kompressoren sowie die Summe der Leerlaufstunden lassen sich über das Leitsystem abfragen. Sie stehen dann unter anderem für das Energiemanagementsystem nach ISO 50001 zur Verfügung. Die rund 100000 kWh, die die neue Station bei gleicher Lastlaufzeit monatlich weniger verbraucht als die alte, entsprechen mehr als 20 Prozent des ursprünglichen Stromverbrauchs.
Mehr Informationen zu Atlas Copco:
![]() |
Atlas Copco Deutschland |
![]() |
Langemarckstr. 35 |
![]() |
D-45141 Essen |
![]() |
Tel.: +49 (0)201 21 77 0 |
![]() |
Fax: +49 (0)201-2177-100 |
![]() |
E-Mail: atlascopco.deutschland@de.atlascopco.com |
![]() |
www.atlascopco.de |
![]() |
------------------------------------------------------ |
![]() |
Handwerkzeuge: |
![]() |
Atlas Copco Tools Central Europe GmbH |
![]() |
Langemarckstr. 35 |
![]() |
D-45141 Essen |
![]() |
Tel.: +49 (0)201 21 77 0 |
![]() |
E-Mail: tools.de@atlascopco.com |
![]() |
www.atlascopco.com/de-de/itba |
War dieser Artikel für Sie hilfreich?
![]() |
![]() |
![]() |
![]() |
![]() |
Bitte bewerten Sie diese Seite durch Klick auf die Symbole.
Zugriffe heute: 5 - gesamt: 9260.