MIM als Zerspanungs-Alternative
Vom Metallpulver zum Serienteil
Massenteile werden häufig viel zu teuer produziert, da ein wichtiges Produktions-Verfahren, das in der Lage ist, die Stückkosten dramatisch zu senken, nur wenigen Firmen in Europa aber auch weltweit bekannt sind. Die Rede ist vom Metallpulverspritzgussverfahren – MIM.
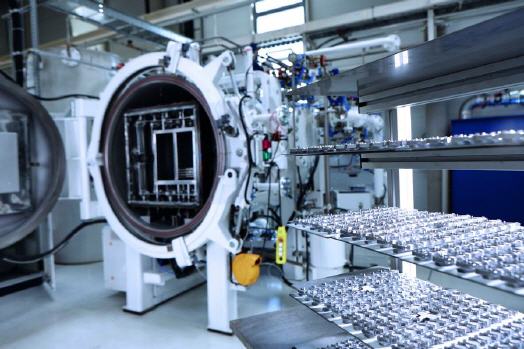
Gerade die Industrie ist immer auf der Suche nach Möglichkeiten, die Stückkosten der eigenen Produkten weiter zu senken, um diese auch künftig zu konkurrenzfähigen Preisen anbieten zu können.,Hier gehen die Firmen häufig im großen Stil an einem echten Fertigungs-Joker vorbei, nämlich dem MIM-Verfahren. Obwohl die MIM--Technik bereits seit den 1980er Jahren bekannt ist, nutzen noch viel zu viele Unternehmen andere kostenintensivere Verfahren für die Herstellung Ihrer komplexen Serienbauteile.
Dabei ist dieses Verfahren für höchste Stückzahlen ideal geeignet, da das Material analog zum Kunststoffspritzguss auf einer Spritzgießmaschine verarbeitet wird. Die Designvielfalt und damit die Komplexität der Bauteile ist ein weiterer Vorteil, der Konstrukteure von Systemen und Komponenten begeistert. Gerade mit diesem Verfahren können Geometrien erreicht werden, die zerspanend nur mit hohen Kosten oder auch gar nicht realisiert werden können. Der Kreativität der Entwickler für Ihre zukünftigen Serienbauteile ist somit keine Grenze gesetzt.
Zudem können die verschiedensten metallischen Materialien, wie niedrig legierte Stähle, rostfreie Edelstähle, Sonderlegierungen und Ti-Legierungen verarbeitet werden. So können die Materialeigenschaften des jeweiligen Metalls für die jeweilige Anwendung optimal ausgenutzt werden.
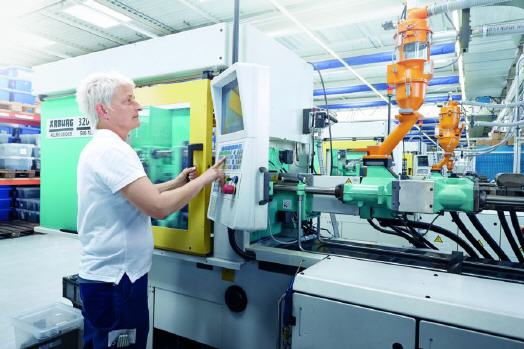
Große Konstruktionsfreiheit
Das MIM-Verfahren, ist eine innovative Technologie, die der Pulvermetallurgie untergeordnet wird. Bei diesem Verfahren wird Metallpulver mit Polymeren und Wachsen homogen zu einem Pulver-Binder Gemisch, dem sogenannten „Feedstock“ verarbeitet. Dieses Ausgangsmaterial ist vergleichbar zum Kunststoffgranulat und kann auf einer herkömmlichen Spritzgussmaschine verarbeitet werden. Bei diesem Prozessschritt wird der Feedstock unter Temperatur zu einer fließfähigen Masse aufgeschmolzen. Hierbei dienen die vorher eingebrachten Binderbestandteile dazu, dass der hochviskose Feedstock in ein Werkzeug eingespritzt werden kann.
Die Werkzeuge selbst haben ein bis vier Kavitäten, je nach benötigter Stückzahl. Zykluszeiten betragen zwischen 20 und 50 Sekunden pro Schuss, d.h. ein bis vier Bauteile werden in dieser Zeit produziert. Die so gewonnenen Bauteile werden ›Grünlinge‹ genannt. Allerdings besitzen diese noch den Binder, der vor der in den folgenden Prozessschritten entfernt werden muss. Dieser Entbinderprozess geschieht in einem katalytischen Entbinderungsofen, bei dem rauchende Salpetersäure im Ofenraum verdampft wird. Der Salpetersäuredampf reagiert mit einem Binderbestandteil zu Formaldehyd, welcher stark mit Stickstoff verdünnt und in einem Kamin verbrannt wird, so dass keine schädlichen Stoffe in die Umwelt entweichen können.
Nachdem ein Bestandteil des Binders entfernt wurde, bleibt ein poröses Werkstück zurück, das ›Braunteil‹, welches durch den Restbinder in Form gehalten wird.
In einem weiteren thermischen Entbindungsprozess, der auch als ›Vorsintern‹ bezeichnet wird, wird bei 400 bis 900 Grad Celsius der restliche Binder aus dem Bauteil entfernt.Bei diesen Temperaturen fangen die feinen Metallpartikel im Bauteil bereits an sich zu verbinden. Sie bilden sogenannte Sinterhälse aus, die das Bauteil stabil halten, um im nachfolgenden Sinterschritt auf etwa 97-99 Prozent der theoretischen Materialdichte gesintert bzw. verdichtet zu werden.
Die eigentliche Umwandlung zum vollen metallischen Bauteil geschieht anschließend im Sinterprozess. Bei diesem Verfahrensschritt werden die Werkstücke auf 1200 bis 1400 Grad Celsius beziehungsweise bis ca. ¾ tel der Schmelzpunkt des jeweiligen Metalls erwärmt. Während des Sinterns, bei dem für jedes Material eine optimiertes Temperaturprofil im Ofen gefahren wird, schließen sich die Poren, die der Binder im Bauteil hinterlassen hat. Das bedeutet, dass das Bauteil analog zum vorher integrierten Binderanteil schrumpft.
Je nach verwendeten Feedstock kann dieser Schrumpf zwischen 15-20 Prozent betragen. Das Besondere ist, dass die so erstellten metallischen Bauteile sich in den mechanischen Werten von konventionell durch Drehen oder Fräsen hergestellten Werkstücken nicht unterscheiden. Dies bedeutet, dass die Festigkeitseigenschaften des eingesetzten Werkstoffs voll zum Tragen kommen und somit das Material gezielt auf die jeweilige spätere Anwendung ausgesucht werden kann.
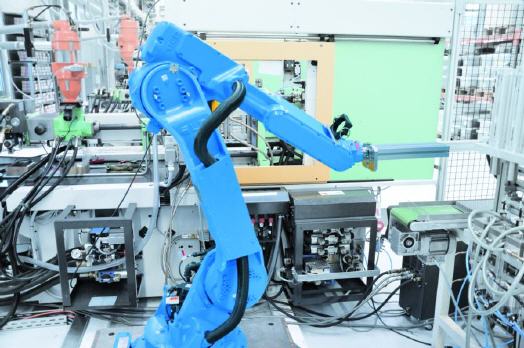
Das neue Denken macht´s
Um die Vorteile der MIM-Technik voll nutzen zu können, muss bereits im Werkzeugbau auf die richtige Auslegung des Werkzeuges und der jeweiligen Geometrie geachtet werden. Es gilt, nicht mehr ›kubisch‹ beziehungsweise ›zerspanend‹ zu denken. Der volle Kostenvorteil von MIM kommt nur zum Tragen, wenn die Teile geometrisch optimiert mit gleichmäßigen Wandstärken und gewichtsoptimiert konstruiert werden. Weitere Details sind am sichersten mit den Experten der Zimmer Group zu besprechen, die das MIM Verfahren für die Serienfertigung von „ In-house“ Produkten , aber auch extern dem Kunden anbieten und in dieser Technologie beraten.
Bei konsequenter Umsetzung sind mit der MIM-Technik Einsparungen zwischen 25 und 65 Prozent im Vergleich zu herkömmlichen Produktionsverfahren möglich. Insbesondere bei komplexen Bauteilen spielt MIM seine Vorteile aus. Sogar Bohrungen, Innen- und Außengewinde, Querbohrungen und Verzahnungen sind problemlos herstellbar. Komplexe Bauteile mit Wandstärken bis hinunter zu 0,5 Millimeter sind möglich. Bei der Konstruktion der Teile gibt es nahezu keine Einschränkungen. Im Gegenteil, sind mit MIM doch völlig neue Ansätze denkbar.
Dadurch, dass mit Pulver gearbeitet wird, das dem Material entspricht aus dem das Bauteil auf herkömmliche Art durch Zerspanen gefertigt worden wäre, verbindet sich der Vorteil der Spritzgusstechnik mit den Festigkeits- und Verschleißeigenschaften der eingesetzten Metalle. Darüber hinaus lässt eine konsequent auf MIM abgestimmte Teilekonstruktion die Fertigungskosten durch die Vermeidung kostenintensiver Montage- und Verbindungstechniken sinken.
Seine Grenzen findet MIM allerdings in der Bauteilgröße, da die Wirtschaftlichkeit von MIM bei Bauteilgewichten von über 150 Gramm nicht mehr gegeben ist. Der Grund liegt im hohen Preis des Feedstock, der es nicht erlaubt, schwere Bauteile mittels der MIM-Technik wirtschaftlich herzustellen. Selbst wenn das Gewicht passen würde: auch die Bauteilgröße spielt eine Rolle in der Kostenfrage, da große Teile den Platz im Prozessofen rasch füllen. Ergo sind die Kosten pro Teil umso geringer, je kleiner das Teil ist. Bei kleinen Werkstücken ab etwa 0,3 Gramm ist das MIM-Verfahren bei hohen Stückzahlen daher eine absolut überlegenswerte Alternative zu herkömmlichen Fertigungsverfahren. Zudem ist das Verfahren extrem nachhaltig, da es äußerst Materialsparend ist und keine Späne entsorgt werden müssen, wenn die Nacharbeit entfällt.
Selbst wenn es konstruktiv nicht möglich sein sollte, dass das herzustellende Teil mittels MIM-Technik fertig aus dem Ofen kommt, lohnt sich das Verfahren aus der Sicht der Fertigung, da die mittels der MIM-Technik hergestellten Werkstücke nach der Formgebung ganz normal gedreht, geschliffen oder gehärtet werden können und auf diese Weise selbst komplizierte Werkstücke mit relativ geringem Aufwand fertiggestellt sind. Auch Hochglanzpolieren, Sandstrahlen, Passivieren, Elektropolieren oder Beizen sind selbstverständlich möglich. Überzüge wie Brünieren, Chromatisieren, Verkupfern, Vernickeln, Versilbern oder Vergolden sind bei entsprechend gewähltem Werkstückmaterial problemlos durchführbar.
Die MIM-Technik empfiehlt sich daher für eine Vielzahl von Anwendungen. Mit dieser Technik ist es möglich, Getriebeteile, Uhren, Schmuck, Brillen, Operationsbestecke, Pinzetten, Zahnspangen oder Teile für Mobiltelefone und Computer anzufertigen. Das aufgezählte Teilespektrum ist jedoch noch lange nicht vollständig. Es lohnt sich, die eigene Produktpalette auf MIM-Tauglichkeit zu überprüfen. Dazu sind oft nur geringe Konstruktionsmodifikationen nötig, wenn überhaupt.
Wer sich der innovativen MIM-Technik öffnen will, jedoch noch keine Erfahrung mit MIM hat, der sollte sich nicht scheuen, diesbezüglich Kontakt mit den Experten der Zimmer Group aufzunehmen, die in der Lage sind, kompetente Beratung zu leisten. Das Unternehmen setzt schon seit einiger Zeit die MIM-Technik mit größtem Erfolg für eigene Produkte ein und gibt das erworbene Fachwissen gerne weiter.
Mehr Informationen zur Sommer-automatic:
![]() |
Sommer-automatic GmbH & Co. KG |
![]() |
Pforzheimer Straße 70 |
![]() |
76275 Ettlingen |
![]() |
Tel. 07243 727-2441 |
![]() |
Fax. 07243 727-2299 |
![]() |
www.sommer-automatic.com |
![]() |
www.zimmer-group.de |
War dieser Artikel für Sie hilfreich?
![]() |
![]() |
![]() |
![]() |
![]() |
Bitte bewerten Sie diese Seite durch Klick auf die Symbole.
Zugriffe heute: 2 - gesamt: 14840.