Weber KP: Via Metallpulver zum Werkstück
Teileproduktion mit Aha-Effekt
Die additive Fertigung dringt mehr und mehr in unterschiedlichste Bereiche vor, die ehemals von der zerspanenden Zunft beherrscht wurden. Wer die Chancen dieser Technologie frühzeitig erkennt, kann sich beizeiten viel Know-how aufbauen, hier eine führende Position einzunehmen. Dies hat das Unternehmen Weber KP erkannt, das in Bretten Innovatives aus Pulver formt.
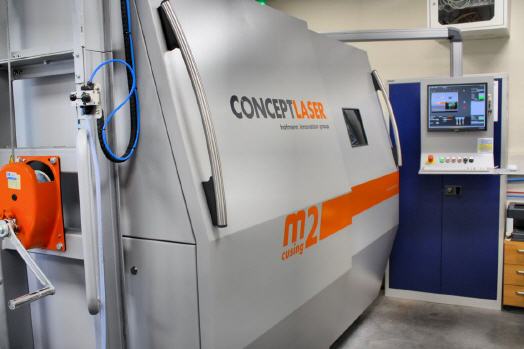
›M2 cusing‹ von Concept Laser
Wer zum ersten Mal ein additiv hergestelltes Teil in Händen hält, reagiert oft erstaunt, wenn verraten wird, auf welche Weise das Werkstück entstanden ist. Dank einer passendenden Oberflächenbearbeitung weist zunächst nichts darauf hin, dass das Teil aus Pulver, einer Kunststoffflüssigkeit oder aus einem festen Filament entstanden ist.
Die Technologien rund um die Additive Fertigung haben schon lange das Versuchsstadium hinter sich gelassen. Nicht zuletzt das selektive Laserschmelzen von Metallen, kurz SLM, erfährt bei vielen innovativen Unternehmen großen Zuspruch, da die damit hergestellten Teile mittlerweile von ihren Festigkeitswerten her gesehen nahezu keinen Unterschied mehr zu traditionell durch Zerspanen hergestellten Teilen aufweisen. Vielfach sind sie sogar durch nur geringe oder sogar ganz ohne Nacharbeit als Einbauteile zu verwenden.
Aufgrund der vielen Vorteile beschäftigt sich das 2007 von Martin Weber gegründete Unternehmen Weber KP bereits seit 2008 mit der Additiven Fertigung. In diesem Jahr wurde in eine FDM-Anlage von Stratasys investiert, die dazu diente, schnell Funktionsprototypen sowie Anschauungsmodelle herstellen zu können. Anhand der Modelle wurden Optimierungen an teils komplizierten Konstruktionen vorgenommen, ehe reale Teile durch Fräsen, Drehen oder Erodieren hergestellt wurden.
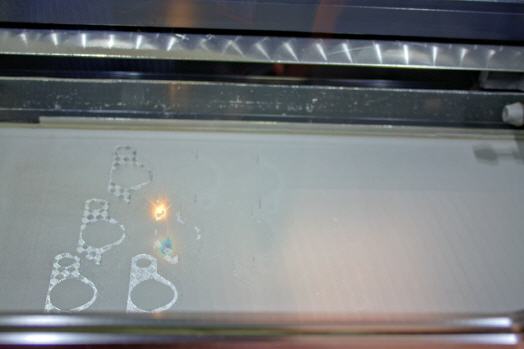
Ein Kontrollsystem überwacht den Bauprozess
Einstieg zum Aufstieg
2014 erfolgte dann der Einstieg in das selektive Laserschmelzen von Metallen. Diese Technologie erlaubt das relativ einfache Herstellen komplizierter Einzelteile und Prototypen aus Metall. Während es bei der zerspanenden Fertigung nötig ist, die Teilekonstruktion an die systembedingten Einschränkungen von zerspanendenden Maschinen anzupassen, ist dies beim Einsatz der SLM-Technologie nicht nötig. Hier können nahezu alle geometrischen Wünsche problemlos erfüllt werden.
Möglich macht dies der schichtweise Aufbau des Teils, das in einem Pulverbett entsteht. Zu diesem Zweck wird über einen Schieber Metallpulver auf eine beheizte Trägerplatte aufgebracht, das anschließend an genau festgelegten Stellen von – je nach Maschinenmodell – einem oder mehreren Laserstrahlen erhitzt wird. Die Hitze schmilzt das an der vom Laserstrahl überstreichten Stelle liegende Metallpulver auf und verbindet die Metallkörnchen untereinander. Dies geschieht bei Temperaturen, die – je nach Metallsorte – bei bis zu 2 000 Grad Celsius liegen. Beim Pulverauftrag überschüssiges Pulver wird übrigens aufgefangen und kann erneut verwendet werden.
Martin Weber hat sich damals für eine ›M2 cusing‹ von Concept Laser entschieden. Diese Maschine verfügt über einen 400 Watt-Faserlaser sowie einen Bauraum von 250 x 250 x 280 mm und ist nach Atex-Richtlinien konstruiert. Auf diese Weise wird garantiert, dass eine sichere Verarbeitung reaktiver Werkstoffe möglich ist. Und reaktiv sind viele Metalle, da diese beim Erhitzen mit dem Sauerstoff der Luft reagieren.
Aus diesem Grund muss der Bauteilraum mit einem Schutzgas geflutet werden. Dies kann, je nach Material, CO2 – etwa bei Stahl und Aluminium – oder Argon – etwa bei Titan – sein. Interessant ist, dass die M2 cusing über einen geschlossenen Gaskreislauf verfügt. In diesem Kreislauf sind Filter zwischengeschaltet, die das Schutzgas von den mitgerissenen Schmauchpartikeln befreien.
Viel Komfort ist durch den automatischen Wechsel zwischen zwei Gasen gegeben. Dazu wird die Verrohrung von der Anlage automatisch vom Restgas der vorherigen Prozedur befreit und mit einem anderen Gas geflutet. Zu diesem Zweck wird automatisch zwischen Flaschenbündel mit unterschiedlichen Gasinhalten umgeschaltet.
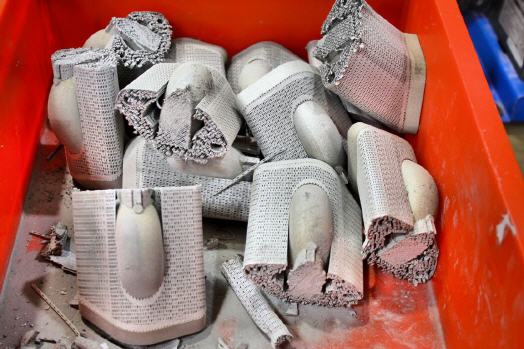
Bauteile nach dem Absägen von der Trägerplatte
Für eine perfekte Produktion
Anzumerken ist, dass der Abfuhr der Schmauchpartikel bezüglich der Bauteilfestigkeit eine zentrale Rolle zukommt. Wird dieser Prozess nicht sicher beherrscht, fallen zu viele im Schmelzprozess verbrannte und hochgewirbelte Partikel auf das Werkstück zurück, wo sie wegen ihrer nun nichtschmelzenden Eigenschaft das Aufschmelzen einer neuen Pulverschicht beeinträchtigen. Sie spielen hier in etwa die gleiche Rolle, wie Lunker in einem Gussstück, die ebenfalls unerwünscht sind und die Festigkeit des Gussteils negativ beeinflussen. Das gereinigte Schutzgas wird wieder in den Kreislauf zurückgeführt und kann erneut seine Schutzwirkung entfalten.
Dass möglichst wenige Schmauchpartikel auf der Oberfläche zurückfallen sollten, hat noch einen weiteren Aspekt: Die Partikel können unter Umständen dazu führen, dass der empfindliche Wischergummi, mit dem neues Metallpulver in kleinsten Schichten auf die bereits bearbeitete Schicht aufgetragen wird, beschädigt wird. Beschädigungen des Wischergummis können zudem entstehen, wenn sich aufzubauende Teile durch den Hitzeeintrag verziehen. In diesen Fällen würde an der beschädigten Wischerstelle, je nach Schadensart, eine zu dicke oder zu dünne Pulverschicht stehenbleiben. Beide Fälle würden zu Bauteilen führen, deren Festigkeit nicht den Anforderungen entspricht.
Damit dies nicht passiert, ist die ›m2‹ von Weber mit einer Digitalkamera ausgerüstet, die jede Pulverschicht abfotografiert. Die damit angefertigten Bilder werden in Echtzeit von der Concept Laser-Software ›QM Coating‹ ausgewertet, um Fehler beim Pulverauftrag sofort zu erkennen. Pro Pulverschicht werden dazu zwei Bilder von der Oberfläche gemacht: einmal vor dem Pulverauftrag, einmal danach. Auf diese Weise kommen pro Bauteil Tausende von Bildern zusammen, die ausgewertet werden müssen. Da diese Technik durch die Rechenzeit den Bauprozess um rund 35 Prozent verlängert, kommt sie bei Weber nur bei besonders kritischen Teilen oder auf ausdrücklichen Kundenwunsch zum Einsatz.
Nicht zuletzt Bauteile für die Medizintechnik profitieren von dieser Analysetechnik. Damit sind Teile über Nacht herstellbar, die garantiert frei von Aufbaumängeln sind. Überhaupt empfiehlt sich das SLM-Verfahren – Concept Laser spricht hier vom ›Laser Cusing‹ – für Bauteile mit hohen Anforderungen an Festigkeit und Designfreiheit. Damit sind dünnwandige Teile mit nur wenigen Zehntelmillimeter Wandstärke ebenso problemlos herstellbar, wie besonders kleine oder ungewöhnlich geformte Teile, die kein Aufnehmen in einem herkömmlichen Spannmittel zulassen.
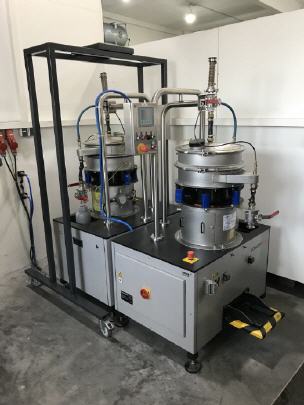
Eine Filteranlage trennt Pulverreste von Abfall
Neue Möglichkeiten
Die weitgehende Freiheit im Design macht es sogar möglich, dass unter Umständen mehrere Bauteile in einem einzigen Bauteil zusammengefasst werden können. So geschehen bei einem Ventil zur Abfüllung von Getränkeflaschen: Bestand das herkömmlich hergestellte Ventil noch aus mehreren Bauteilen, die viel Platz benötigten, so ist künftig nur mehr ein einziges, verhältnismäßig kleines Ventil nötig, das von Weber dank Additiver Fertigung auch noch billiger herzustellen ist, als die Einzelteile der bisher eingesetzten Ventilinsel kosteten.
Groß im Geschäft ist die Additive Fertigung auch im Oldtimer-Ersatzteilgeschäft. Vielfach gibt es zu gefragten Automodellen früherer Jahrzehnte keine Originalteile mehr. Weber hingegen fertigt beispielsweise für das Unternehmen ›Porsche Classic‹ Ersatzteile, die dem Original in nichts nachstehen. Unter anderem werden Bauteile für das Kühlsystem ebenso aus Pulver hergestellt, wie Halter für das Getriebe.
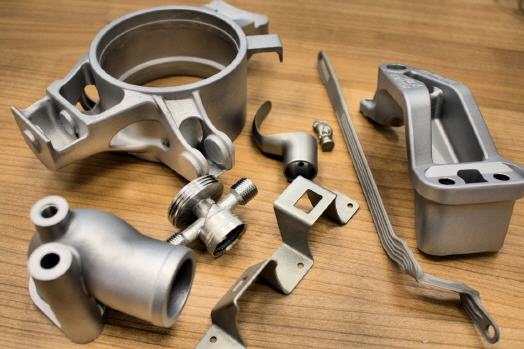
Das Laserschmelzen ist sehr vielseitig
Der digitale Weg
Und wo es keine technischen Zeichnungen gibt, werden eben per Laserscanner die Teile kurzerhand digitalisiert und für die Fertigung via SLM aufbereitet. So geschehen bei einem Denkmal, dem sogenannten ›Brettener Hundle‹. Dieses wurde für ein Event abgescannt und digital aufbereitet. Die digitale Fertigung machte es möglich, ohne den Zwischenschritt über eine Gussform direkt dutzende Kopien des Denkmals im Miniformat anzufertigen, die beim Fest unter die Leute gebracht wurden.
Auch bei der Anfertigung von Ausschabwerkzeugen, die im Rahmen von Hüftoperationen eingesetzt werden, ist eine akkurate Herangehensweise bezüglich deren Produktion wichtig, soll ihr Bau gelingen. Diese Werkzeuge bestehen in der Regel aus dem Edelstahlpulver 17-4 PH, das nach der Formgebung noch gehärtet werden kann. Da diese Werkzeuge eine scharfe Schneide bekommen und dünnwandig sind, ist eine sorgsame Herstellung extrem wichtig, soll später die OP erfolgreich verlaufen. Hier ist die wohlüberlegte Vorgehensweise beim Aufbau gefragt, damit der dünne Schablöffel exakt nach Maß aufgebaut wird.
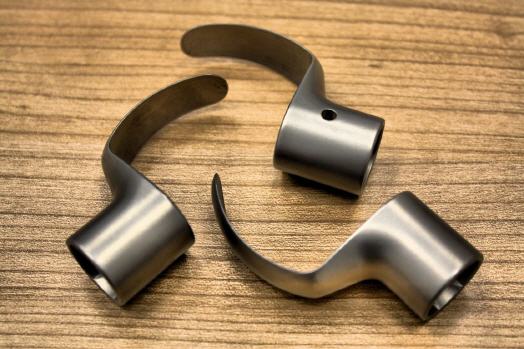
Auch filigrane Werkzeuge sind machbar
Die Grundlagen des Erfolgs
In jedem Fall sind bestens ausgebildete Fachleute gefragt, soll die Additive Fertigung zum Erfolg werden. Sie erkennen anhand der letzten Pulverschicht, ob der Aufbauprozess erfolgreich war, wissen, wie Stützstrukturen anzubringen sind, und kennen die unterschiedlichen Parameter der unterschiedlichen Metallpulver, um diese zuverlässig aufzuschmelzen. Zusätzlich achten sie darauf, dass der Laser stets die korrekte Leistung bringt. Zu diesem Zweck wird in bestimmten Zeitraumabständen eine Laserfeldmessung durchgeführt.
Die Additive Fertigung ist, ebenso wie die zerspanenden Verfahren, eine Technik, die man nicht mal so eben ausführen kann. Zahlreiche Stellschrauben, wie etwa Scangeschwindigkeit, Spurabstand oder Spotgröße sind zu berücksichtigen, soll ein Werkstück korrekt aufgebaut werden. Hilfe gibt es von Concept Laser, da das Unternehmen für seine Maschinen Parameterlisten anbietet, die entweder zu jedem bei Concept Laser erworbenen Material mitgeliefert werden oder käuflich zu erwerben sind. Mit der Software ›CL WRX Parameter 2.0‹ können diese Parameter eingesehen und variiert werden.
Doch auch nach dem Aufbau eines Teils ist Wissen gefragt, sollen unliebsame Überraschungen fernbleiben. So darf beispielsweise ein eben aufgebautes Teil nicht in jedem Fall sofort von der Stützstruktur gelöst werden, wenn eine hohe Maßhaltigkeit gefragt ist. Der Grund sind Spannungen, die durch die Laserhitze in das entstehende Teil eingebracht werden. In diesem Fall ist das komplette Teil zunächst spannungsfrei zu glühen, ehe die Stützstrukturen entfernt werden.
Es zeigt sich, dass das Schmelzen von Metallpulver keine triviale Sache ist. Sicher geht, wer, wie Martin Weber, auf einen erfahrenen Anbieter, in diesem Fall auf Concept Laser, setzt. Dann steht dem Einstieg in den Aufstieg nichts entgegen.
Mehr Informationen zu Concept Laser:
![]() |
CONCEPT Laser GmbH |
![]() |
An der Zeil 8 |
![]() |
96215 Lichtenfels |
![]() |
Tel.: +49 (0) 9571 / 949-238 |
![]() |
Fax: +49 (0) 9571 / 949-239 |
![]() |
E-Mail: info@concept-laser.de |
![]() |
www.concept-laser.de |
War dieser Artikel für Sie hilfreich?
![]() |
![]() |
![]() |
![]() |
![]() |
Bitte bewerten Sie diese Seite durch Klick auf die Symbole.
Zugriffe heute: 1 - gesamt: 2991.