Glanzfräsen statt erodieren und polieren
Viermal schneller zum HM-Rundkern
Die Wild & Küpfer AG (W&K) produziert Kunststoffspritzgussteile, die höchsten Qualitätsansprüchen genügen. Von zentraler Bedeutung ist dabei der betriebseigene Werkzeugbau, in dem eine Kern Micro und seit 2020 eine Kern Micro HD für höchste Präzision und Produktivität sorgen.
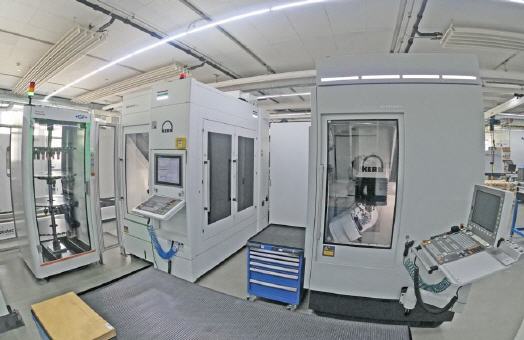
„Aus Visionen sollen Ideen und daraus Produkte werden“. Diesem Credo folgt der Schweizer Kunststoffspritzgusshersteller Wild & Küpfer schon seit seiner Gründung vor über 40 Jahren – heute mehr denn je. Das mittelständische Unternehmen im Kanton St. Gallen bietet von der Beratung und Entwicklung, über den Werkzeugbau und Produktion bis hin zur Baugruppenmontage im Reinraum, die komplette Herstellungskette für ihre Kundenprodukte samt Logistik und Service.
Diese Durchgängigkeit gepaart mit höchster Produktqualität schätzen Kunden aus der Elektro- und Automobiltechnik, Telekommunikation, Pharma-, Medizin- und Dentaltechnik. Die meisten von ihnen nutzen die gesamte Wertschöpfungskette von W&K und arbeiten mit den Kunststoffexperten schon in der Entwicklungsphase eng zusammen.
CTO Daniel Wild, der seit dem Jahr 2000 im Betrieb arbeitet und seit 2019 gemeinsam mit seinem Bruder Tobias die Geschäfte des Unternehmens leitet, erklärt: „Wir produzieren verschiedenste Kunststoffbauteile oder -baugruppen, die unsere Kunden für ihre Endprodukte brauchen. Dabei liegen die Losgrößen durchschnittlich bei ca. 100.000 Stück pro Jahr. Wir haben aber auch Kunden, die nur wenige 1000 oder mehr als 100 Mio. Stück pro Jahr benötigen. Auch das können wir.“
Die Produkte sind so vielfältig wie die Branchen. Wild nennt ein paar Beispiele: „Wir produzieren Vorhang-Gleitelemente, spezielle Flaschenverschlüsse und Elektro-Steckerleisten ebenso wie sicherheitsrelevante Verschlusssysteme für den Antidopingbereich und komplexe medizintechnische Baugruppen, die unter anderem für Einführvorrichtungen zum Setzen von Stents gebraucht werden. Dafür ist natürlich extrem viel Know-how gefragt.“ Das beginnt bei der Einschätzung, ob und wie die gewünschten Kunststoffteile herstellbar sind und endet in der Produktion und Auslieferung von Spritzguss-Serienbauteilen. Der Qualitätsanspruch ist stets sehr hoch, egal ob Zehntausend oder Millionen Produkte pro Jahr benötigt werden.
80 Prozent der Bauteilqualität kommt aus dem Werkzeug
Zwischen Beratung und Auslieferung wird entwickelt, konstruiert und produziert. Außerdem stellt W&K die Formen für seine Spritzgussmaschinen allesamt selbst her. Der Grund liegt für Technikchef Daniel Wild auf der Hand: „80 Prozent der Bauteilqualität kommt aus dem Werkzeug.“ Der gelernte Werkzeugmacher und studierte Maschinenbauer, der bereits von Kindesbeinen an ein Teil der Firma ist, misst daher dem betriebseigenen Werkzeugbau höchste Bedeutung zu: „An dieser Stelle überlassen wir nichts dem Zufall und gehen auch im Hinblick auf die technische Ausstattung keine Kompromisse ein.“
Die Best-Quality-Philosophie ist bei W&K nichts Neues. Schon die Gründer Tobias Wild sen. (Vater) und Peter Küpfer (Onkel) gingen bedingungslos diesen Weg. Das brachte sie im Jahr 2014 mit der Kern Microtechnik GmbH zusammen. Daniel Wild dazu: „Wir suchten damals eine dynamische Fünfachs-Präzisionsmaschine für die mannlose Elektrodenfertigung, die in unser Automationskonzept passte. Natürlich war uns der Name Kern in diesem Zusammenhang gut bekannt. So kam es bald zu einer Evaluation und unsere Entscheidung fiel auf eine Kern Micro.“
Konfiguriert auf die permanente Trockenzerspanung von Grafitelektroden erledigte sie diese Aufgabe viele Jahre zuverlässig, rund um die Uhr. Im Jahr 2019 reifte bei den W&K-Geschäftsführern die Idee, mit einer Hochpräzisionsmaschine in den „Mischbetrieb“ zu gehen. Das heißt, dass nicht nur gehärteter Stahl, Bunt- und Hartmetalle, sondern auch Grafit nass und ohne Umrüstung, auf der gleichen Maschine automatisiert zerspant werden kann.
Kern Micro HD für aktuelle und künftige Herausforderungen
Das Fräsen von Grafit- und Kupferelektroden, gehärteten Formeinsätzen und Hartmetallkernen in Kleinserien von durchschnittlich 50 Stück übernimmt seither ein neues Fünfachszentrum der Extraklasse, wie Daniel Wild sagt: „Das gestiegene Auftragsaufkommen machte eine entsprechende Investition notwendig. Wir evaluierten, testeten und waren uns diesmal noch schneller einig, dass wir mit der Kern Micro HD die aktuellen und künftigen Herausforderungen am besten lösen werden.“ Dabei sind die Brüder Wild nicht nur von der Kern-Technologie überzeugt, gleiches sagen sie von der Philosophie des Unternehmens: „Das ist wie bei uns – man spürt den Familien-Gedanken. Jeder unterstützt jeden und denkt nicht kurz- sondern immer mittel- und langfristig.“
Um optimale Ergebnisse erzielen zu können, passten Kern-Ingenieure die Kern Micro HD perfekt an die Bedürfnisse von W&K an. Sie konzipierten und integrierten eine spezielle Kühlschmiermittelaufbereitung, eine Ringdüse sowie ein großes Werkzeugmagazin mit 210 Plätzen für HSK-E40 Aufnahmen. Dadurch funktioniert der Mischbetrieb stets einfach und zuverlässig. Im Sinne hoher Flexibilität ebenso hilfreich: die Kern Micro HD ist mit einer System-3R-Zelle komplett automatisiert. Darüber hinaus schätzt CTO Wild diverse Standard-Produktivitäts-Komponenten wie die verschleißfreien, aktiv temperierten Linearmotore, die Beschleunigungen von bis zu 2 g und Eilgangsgeschwindigkeiten bis 60 m/min erreichen.
Auf die Frage was denn die HD so besonders macht, entgegnet Kern Gebietsverkaufsleiter Stephan Zeller: „Die herausragende Technik der Maschine hat sich seit der Einführung im Jahre 2019 im Markt herumgesprochen und bei Kunden bewährt. Eine verschleißfreie, hydrostatische Maschine, wie die Kern Micro HD, ist einfach einzigartig.“
Zwei Stunden anstatt acht Stunden
Daniel Wild kennt alle Features die zur hohen Präzision und Produktivität der Kern-Maschinen beitragen. Um darüber hinaus für seine speziellen Belange belastbare Zahlen an eigenen Produkten zu bekommen, hat er einen eigenen Vergleich an einem bei ihm häufig benötigten Bauteil durchgeführt. Es handelt sich dabei um einen Rundkern mit Außengewinde aus Hartmetall. Dieser wird zur Herstellung einer Kunststoff-Schraubkappe für einen Spritzenverschluss in der Medizintechnik benötigt.
Den Rundkern produzierten die Werkzeugbauer einmal traditionell durch Senkerodieren und manuelles Strichpolieren. Zum Vergleich frästen sie es anschließend fünfachsig mit der Kern Micro HD. Wild erklärt: „Zum Erodieren brauchen wir bereits gut drei Stunden und danach noch etwa fünf Stunden zum Strichpolieren. In Summe liegen wir da etwa bei einer achtstündigen Prozesszeit. Das Fräsen mit der HD dauert ziemlich genau zwei Stunden – mannlos und mit einer Oberfläche, die einer Strichpolitur entspricht.“
Unter dem Motto „Eine Maschine muss mindestens so flexibel sein wie der Kunde es ist“ rüsteten im Projektverlauf Kern Techniker die vorhandene Kern Micro mit einer Kühlschmiermitteleinheit und einer Absaugung aus. Jetzt steht sie neben ihrer großen Schwester, fräst hochgenaue Einzelteile und kommt zum Einsatz, wenn Änderungen an bestehenden Produkten durchzuführen sind.
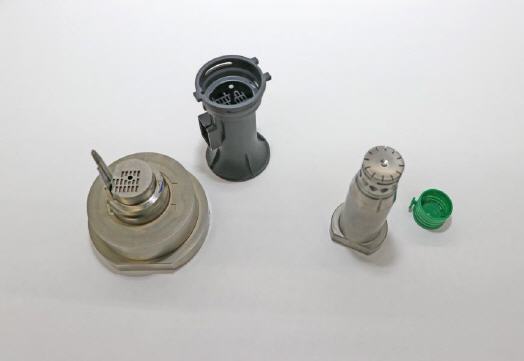
Mehr Information zu KERN:
![]() |
KERN Micro- und Feinwerktechnik GmbH & Co. KG |
![]() |
Olympiastrasse 2 |
![]() |
82438 ESCHENLOHE |
![]() |
Tel.: +49 (0)8824 9101 0 |
![]() |
Fax:-+49 (0)8824 9101 124 |
![]() |
Email: mtsales@kern-microtechnic.com |
![]() |
www.kern-microtechnic.com |
War dieser Artikel für Sie hilfreich?
![]() |
![]() |
![]() |
![]() |
![]() |
Bitte bewerten Sie diese Seite durch Klick auf die Symbole.
Zugriffe heute: 1 - gesamt: 4300.