Produktion auf innovativere Art
Additive Fertigung mit viel Zukunft
Die additive Fertigung schickt sich an, die Produktion von Teilen grundlegend zu ändern. Frank Herzog, Gründer und CEO der Concept Laser GmbH, gibt interessante Einblicke, was diesbezüglich möglich ist und noch kommen wird.
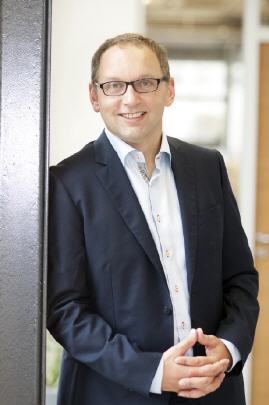
Frank Herzog, CEO der Concept Laser GmbH
Frank Herzog kann zweifelsohne in einem Atemzug mit deutschen Erfindern, wie etwa Conrad Röntgen oder Konrad Zuse genannt werden, war es doch seine Idee, mithilfe eines Lasers aus Metallpulver feste Teile herzustellen.
Sehr geehrter Herr Herzog, die additive Fertigung ist auf dem besten Weg, zu einem wichtigen Bestandteil der Teileproduktion zu werden. Sie und ihr Unternehmen sind ein Wegbereiter dieser innovativen Art, Teile herzustellen. Wie sind Sie auf die Idee gekommen, Metallpulver per Laser zu 3D-Teilen zu formen?
Frank Herzog: Nun, das ist sicher meinem beruflichen Werdegang geschuldet. Ich hatte das Gymnasium nach der Oberstufe verlassen und eine Lehre als Industriemechaniker begonnen. Danach begann ich ein Studium des allgemeinen Maschinenbaus. Während dieser Zeit kam ich mit der Stereolithografie in Berührung und war von dieser Technik total begeistert. Ich überlegte mir damals, ob es nicht möglich wäre, auf diese Weise Werkstücke aus Metallen, statt aus Kunststoff herzustellen.
Für meine Diplomarbeit habe ich mich dann entschieden, diesen Gedanken aufzugreifen. Damals – das war um das Jahr 1998 herum – baute ich den ersten 3D-Drucker im Kleinformat, der manuell bedient wurde und in der Lage war, Metallpulver via Laser zu festen Plättchen zu verschmelzen. Diese Plättchen waren anfangs jedoch recht zerbrechlich, weshalb ich unbedingt eine Lösung brauchte, die mehr Festigkeit versprach.
Die Lösung steuerte meine heutige Frau bei, die zur gleichen Zeit an der gleichen Fachhochschule studierte und für ihre eigene Diplomarbeit Zugang zu einem Laser mit kürzerer Wellenlänge hatte. Sie lieh mir diesen Laser für eigene Versuch aus. Und siehe da, die Teile wurden damit fester, da das Pulver besser aufgeschmolzen wurde. Der damals für die Diplomarbeit hergestellte Mini-3D-Drucker steht heute übrigens in unserem Empfangsraum.
Interessant, wie lange dauerte es dann noch, um von der Idee zu einer ersten Prototypanlage zu kommen?
Herzog: Nach unserem Studium war es der Wunsch von meiner Frau und mir, eine Firma zu gründen, die sich dem pulverbettbasierten Laserschmelzen von Metallen widmet. Wir wollten Maschinen bauen, mit denen dies möglich war. Also gründeten wir im Jahr 2000 die Concept Laser GmbH und bauten mit anfangs vier Mitarbeitern in nur 15 Monaten einen ersten Prototypen, den wir 2001 auf der Messe ›Euromold‹ der Fachwelt vorstellten.
Die Maschine, genannt ›M3 linear‹, konnte Schmelzen, Abtragen sowie Gravieren und war praktisch eine Weltpremiere, was uns damals gar nicht bewusst war. Jedenfalls war der Zuspruch für diese Technik damals enorm, was uns die Gewissheit gab, auf das richtige Pferd gesetzt zu haben.
Wie haben Sie dies alles finanziert?
Herzog: Das war gar nicht so einfach. Damals war es sehr schwer, an angemessene Fördermittel der öffentlichen Hand zu kommen, um ein derartiges Vorhaben umzusetzen. Zum Glück waren die Eigner der Hofmann Innovation Group von der Idee, mit einem Laser Pulver aufzuschmelzen und darauf feste Bauteile zu produzieren, überzeugt und stellten uns 1,5 Millionen DM zur Verfügung, die innerhalb von zwei Jahren rückzahlbar waren. Zusammen mit einem öffentlichen Darlehen der Bayerischen Staatsregierung in Höhe von 350 000 DM war damit der Grundstock vorhanden, das Wagnis zu schultern.
Ihre Laseranlagen haben das Wort ›Cusing‹ im Namen. Was bedeutet dieses Wort?
Herzog: Der Begriff LaserCUSING, zusammengesetzt aus dem C von Concept Laser und dem englischen FUSING (vollständig aufschmelzen), beschreibt die Technologie, bei welcher wir das Pulver schmelzen und nicht sintern.
2016 wurde Concept Laser zu 75 Prozent von General Electric übernommen. Was hat sich seither geändert?
Herzog: Der Markt des 3D-Metalldrucks wächst extrem stark. Die Überlegung vor einigen Jahren war, ob wir als relativ kleines Unternehmen mit damals rund 200 Mitarbeitern diesem Wachstum gerecht werden können. Unser Problem war, dass wir mittel- bis langfristig nur schwer in der Lage gewesen wären, personell und finanziell in der notwendigen Weise zu wachsen, um mit der stark steigenden Marktgröße Schritt zu halten. Es war die Befürchtung vorhanden, dass wir zwischen großen Unternehmen zerrieben werden könnten. Also haben wir uns nach einem starken Partner umgesehen, der dieses Wachstum möglich machen würde.
Diesen Partner haben wir in GE gefunden. Die Power von GE erlaubt es uns, die bisher verteilten Verwaltungs- und Produktionsbereiche in einem Neubau, dem sogenannten ›3D Campus‹, zusammenzuführen. Während die Produktion bereits Mitte 2019 einziehen wird, folgt die Verwaltung Mitte 2020. Rund 105 Millionen Euro wurden in dieses Projekt gesteckt. Geldmittel, die wir nie hätten alleine aufbringen können.
GE hat nicht nur uns, sondern noch weitere Firmen erworben, um im Bereich des 3D-Metalldrucks eine weltweit führende Stellung einzunehmen. Darunter ein schwedisches Unternehmen (Arcam), welches Maschinenlösungen mit der EBM-Technologie anbietet, ein kanadisches Unternehmen (AP&C), das Pulver herstellt sowie ein Softwareunternehmen aus Belgien (GeonX), das Lösungen im Bereich der Additiven Fertigung anbietet. Ich bin fest davon überzeugt, dass wir mit dem Zusammenschluss unsere Arbeitsplätze in Lichtenfels auf Dauer sichern und zusammen mit GE eine starke Stellung auf dem Weltmarkt erreichen werden.
Wo sehen Sie die größten Chancen des LaserCUSING?
Herzog: Überall dort, wo Produkte anders gedacht werden. Das kann in der Medizintechnik ebenso sein, wie im Fahrzeugbau oder in der Luft- und Raumfahrttechnik. Das Verfahren des Selektiven Laserschmelzens erlaubt es, die Produktion bisher extern angefertigter Teile wieder ins eigene Haus zu holen, da damit Dinge möglich sind, für die bisher spezielle Maschinen oder Verfahren nötig waren.
Wer bereit ist, sein Portfolio hinsichtlich der Fertigungsweise eigener Produkte zu hinterfragen, wird feststellen, dass hier viel Potenzial schlummert, Teile zu vereinfachen, viele Einzelteile in einem Teil zu vereinigen oder die Zahl der Lieferanten, und somit den Beschaffungsaufwand, zu reduzieren. Beispielsweise können Module für die Raumfahrt künftig in einem Stück gedruckt werden und müssen nicht mehr aus mehreren Komponenten durch Löten oder Schweißen komplettiert werden.
Dass dies möglich ist, zeigt sehr schön eine neue Satellitenantenne, die früher aus 100 Einzelteilen bestand und heute aus einem Stück mit unserem Verfahren komplett aus Metallpulver hergestellt wird. Durch die Additive Fertigung konnte die Antenne rund 95 Prozent leichter und um rund 25 Prozent günstiger hergestellt werden. Zudem ist die RF-Leistung sogar besser, als die von herkömmlich hergestellten Antennen. Man sieht, dass das Spektrum der Additiven Fertigung sehr groß ist und nur durch die Fantasie der Konstrukteure begrenzt wird. Es hilft durchaus, ein wenig „Spinnert„ zu denken, um zu neuen Ufern aufzubrechen!
Welche Verschiebung der Marktanteile zwischen zerspanenden und aufbauenden Verfahren erwarten Sie durch die zunehmende additive Fertigung?
Herzog: Ich denke, dass weniger die zerspanenden Bereiche, als vielmehr die Gusstechnik Marktanteile durch das Laserschmelzen von Metallen verlieren wird. Wer sich das Spektrum additiv gefertigter Teile ansieht, wird dies bestätigen. Da das Finishen nach wie vor nötig ist, wird es beim Zerspanen zumindest nicht zu größeren Verschiebungen kommen.
Erwarten Sie eine völlige neue Gattung an zerspanenden Werkzeugmaschinen, um additiv gefertigte Teile nachzubearbeiten? Schließlich treten nur kleine Zerspanungskräfte auf, sind verschiedentlich Passungen einzubringen und Oberflächen zu finishen.
Herzog: Das ist ein interessanter Aspekt! Natürlich müssen Maschinenbauer sich wohl hinsichtlich des Aufbaus ihrer Maschinen Gedanken machen, da additiv hergestellte Teile nahezu Fertigmaß haben und nur mehr wenige Zehntelmillimeter abzutragen sind. Werkzeugmaschinen für das Nachbearbeiten additiv gefertigter Teile werden daher wohl anders konstruiert sein, als Maschinen, die für massive Zerspanungsleistungen gedacht sind. Insbesondere werden diese wohl leichter sowie agiler werden und über Spindeln verfügen, die wesentlich höhere Drehzahlen bieten, als sie heute an Werkzeugmaschinen üblich sind.
Extrem feines Pulver stellt eine Gefahr dar. Man denke etwa an eine Staubexplosion oder an Lungengängigkeit beim Einatmen. Wie werden künftige Lasercusing-Maschinen konstruiert sein, damit sehr feine Metallpulver keine Gefahrquelle darstellen?
Herzog: Aktuell sind Korngrößen von 10 bis 40 Mikrometer Standard. Unsere Maschinen sind derart konstruiert, dass solche Pulver problem- und gefahrlos verarbeitet werden können. Hinsichtlich der Körnergröße ist es nicht unbedingt so, dass das Pulver so fein wie möglich sein soll. Ganz im Gegenteil, auch gröbere Körner sind durchaus interessant, da diese beispielsweise durch ihre kleinere Oberfläche weniger reaktiv sind und weniger Feuchtigkeit binden. Kleinere Körnchen bedeuten auch nicht unbedingt festere Körper, da dies eine Frage des Gefüges ist, das sich nach dem Erkalten bildet. In dieser Frage gibt es noch viel Forschungsbedarf. Auch hier hilft uns der Zusammenschluss mit GE sehr, da in diesem Unternehmen eine diesbezügliche Expertise vorhanden ist.
Bisher gibt es keinen Ausbildungsberuf, der auf die additive Technik zugeschnitten ist. Welche Ausbildungsinhalte müsste ein diesbezüglich neuer Beruf haben?
Herzog: Ich denke nicht, dass ein eigenes Berufsbild nötig ist, um den Bedarf der Industrie an Fachleuten zu decken, die mit Maschinen für die additive Fertigung umgehen können. Ich weiß aus meiner eigenen Ausbildungszeit, dass es für die verschiedenen Berufe sogenannte Ausbildungsmodule gibt, in deren Rahmen man Feilen, Drehen und Löten lernt. Ich kann mir gut vorstellen, auch für die additive Fertigung solch ein Modul zu erstellen und in die Ausbildung der relevanten Berufe zu integrieren.
Je mehr Laserstrahlen in einer Maschine zum Einsatz kommen, desto schneller sind die Teile fertig. Welche maximale Laserzahl ist wirtschaftlich und technisch sinnvoll?
Herzog: Aktuell bieten wir Maschinen mit vier Lasern an. Die Integration von immer mehr Lasern in die Maschinen ist zwar technisch möglich, doch stellt sich die Frage nach dem wirtschaftlichen Nutzen. Hinzu kommt, dass auch die Steuerung der Aufrüstung angepasst werden muss, schließlich muss die Bahn jedes Laserstrahls so berechnet werden, dass sich die einzelnen Strahlen nicht überkreuzen, was einen fehlerhaften Schmelzprozess an einer bestimmten Stelle des Bauteils zur Folge hätte. Wir arbeiten durchaus daran, den Bauprozess der Teile zu beschleunigen, doch möchte ich dazu noch nichts sagen, in welche Richtung wir gehen werden.
Große Teile benötigen entsprechend große Maschinen. Wo sehen Sie die Grenze hinsichtlich der Maschinengröße im Bereich der additiven Fertigung?
Herzog: Grundsätzlich gibt es fast keine Begrenzung der Baugröße, was die additive Fertigung per Laserschmelzen von Metallen betrifft. Allerdings wird der Auftrag von Metallpulver bei steigender Aufbaufläche zum Problem. Je größer die Fläche, desto schwieriger wird es, Schicht für Schicht ein stets gleichmäßiges Pulverbett zu erzeugen. Hier sehen wir für das bisher in unseren Maschinen genutzte Verfahren Grenzen.
Die Lösung könnte sein, nur an denjenigen Stellen Pulver aufzutragen, an denen es benötigt wird. Dazu muss jedoch eine Möglichkeit gefunden werden, Pulver an Überhängen sicher aufzubringen, schließlich entstehen durch dieses Verfahren Hohlräume, die frei von Pulver sind. Ergo würde dort aufgetragenes Pulver in die Tiefe fallen. Zudem ist das Verzugsverhalten von größeren Bauvolumina ebenfalls ein relevanter Faktor für die Machbarkeit von Bauteilen.
Mit dem Modell ›Project A.T.L.A.S:‹ haben wir zusammen mit GE jedoch einen Drucker im Programm, der über eine Druckfläche von einem Quadratmeter verfügt. Das Konzept ist modular ausgelegt, sodass künftig auch größere Teile damit gedruckt werden können, was nicht zuletzt für die Luftfahrtindustrie von Interesse ist.
Additiv hergestellte Teile können nicht nur Einzelteile, sondern ganze Baugruppen sein. Ist es Utopie, dereinst voll belastbare Baugruppen herzustellen, deren Einzelteile teilweise eine Funktion haben, sich daher bewegen können?
Herzog: Solche Teile wurden von uns bereits hergestellt! Beispielsweise haben wir für einen Uhrenhersteller ein Uhrenarmband produziert, dessen einzelne Glieder nicht mehr montiert werden müssen. Dieses Armband kommt fix und fertig aus dem Drucker. Ein weiteres Beispiel ist ein Kupplungsgelenk, das ebenfalls ohne Montage gebrauchsfertig durch das Verschmelzen von Metallpulver entsteht. Diese Beispiele zeigen, dass man Produkte neu denken muss, um die Vorteile der additiven Fertigung für sich zu nutzen.
Hier ist die Entwicklung erst ganz am Anfang. Sicher werden im Laufe der Jahre noch weitere Innovationen kommen, die immer näher zur perfekten, einbaufertigen Komponente führen. So etwas muss über einen längeren Zeitraum reifen, da gute Ideen meist auf zuvor gemachten Ideen aufbauen.
Wo werden die Grenzen solcher Teile etwa hinsichtlich Lebensdauer oder Drehzahl sein?
Herzog: Aktuell sind fix und fertig gedruckte, bewegliche Teile natürlich nicht mit Teilen zu vergleichen, die aus mehreren einzelnen Komponenten bestehen, da etwa die Oberflächenhärte eines Stiftes oder die Rauheit einer Bohrung sich unterscheiden. Nichtsdestotrotz sind diese Teile für untergeordnete Anwendungen, in denen geringe Belastungen auftreten, ideal. Hoch belastbare Lager etwa sind derzeit noch utopisch, doch ist dieses Ziel über viele Zwischenschritte wohl durchaus erreichbar.
Verlieren künftig Passungen an Bedeutung? Immerhin wären Spielpassungen und Presspassungen bei additiven Verfahren direkt programmierbar.
Herzog: Teilweise ja, so sind etwa Presspassungen nicht mehr nötig, da die Teile durch eine additive Fertigung bereits fest verbunden sind. Spielpassungen sind selbstverständlich möglich, wie das Beispiel des bereits erwähnten Kupplungsgelenks zeigt. Allerdings sind systembedingt natürlich Grenzen gesetzt, was die Größe des Passungsspiels betrifft. Zudem gilt: müssen Teile demontierbar sein, um beispielsweise Wartungsarbeiten zu ermöglichen, so sind die Konstrukteure gefragt, eine entsprechende Lösung zu finden, die sich idealerweise additiv umsetzen lässt.
Was sollte moderne Software können, um für die Additive Fertigung prädestiniert zu sein?
Herzog: Nun, die Additive Fertigung durch das Schmelzen von Metallpulvern muss man als geschlossene Fertigungskette betrachten. Innerhalb dieser Kette sind immer wieder verschiedene Parameter anzupassen, wenn der Prozess nicht wie gewünscht abläuft. Mit unserer Software ist es beispielsweise möglich, die Intensität des vom Metallpulver zurückgestrahlten Lichts auszuwerten. Dies ermöglicht das Erkennen von Abweichungen vom Sollwert, und somit als Indikator für mögliche Schwachstellen im finalen Bauteil.
Darüber hinaus ist es wichtig, vor dem Start des Bauvorgangs diesen zunächst zu simulieren. Dadurch kann beispielsweise der Wärmegang festgestellt werden, der das Bauteil räumlich bewegen kann, beziehungsweise im Bauteil unnötig große Spannungen aufbaut. Dies kann mit einer Korrektur der Parameterwerte verhindert werden.
Vielfach ist das Verarbeiten mehrerer Materialien gewünscht, um etwa Stromleitende und isolierende Bereiche in einem Teil zu erzeugen. Es gibt zwar Anlagen, die feste und elastische Kunststoffe verarbeiten, doch keine, die Metalle und Kunststoffe verarbeiten können. Ist von Concept Laser eine Maschine in der Planung, die diese Lücke füllt oder wird dies aus technischen Gründen nie möglich sein?
Herzog: Das Verarbeiten mehrerer Metalle sowie Kunststoffe mit einer einzigen Maschine ist sehr anspruchsvoll. Wir stecken hinsichtlich der Additiven Fertigung erst in den Kinderschuhen einer großartigen Entwicklung, vergleichbar der ersten Automotoren, die meilenweit von heutigen Hochleistungsmotoren entfernt sind. Sicher wird die Zukunft auch bei der Additiven Fertigung noch viele bahnbrechende Erfindungen hervorbringen, an die wir aktuell noch gar nicht denken. Ich bin jedenfalls zuversichtlich, dass uns die Additive Fertigung noch viele Produkte schenken wird, an die wir aktuell noch gar nicht denken. Entscheidend für zukünftige Entwicklungen sind jedoch die jeweiligen Business Cases.
Die Maschinen von Concept Laser sind voller patentierter Innovationen. Wie können Sie sicherstellen, dass diese nicht von Fernost-Plagiatoren für deren Maschinen unerlaubterweise genutzt werden?
Herzog: Der beste Schutz vor Plagiatoren ist ständige Innovation. Hier sind, und waren wir immer sehr gut. Patente können hier dennoch sehr hilfreich und ein flankierender Schutz der eigenen Produkte und Produktstrategie sein.
Ihr Unternehmen hat eine ausgesprochen innovative Lösung entwickelt, Teile aus dem 3D-Drucker vollautomatisch, also inklusive nachfolgender Zerspanung und Qualitätskontrolle, herzustellen. Dazu fahren die Teile von Kabine zu Kabine, wo sie vollautomatisch weiterbearbeitet werden. Welche Zielgruppe haben Sie hier im Fokus und wann wird das Konzept realisiert werden?
Herzog: Hier sprechen Sie unser System ›M LINE FACTORY‹ an. Der Kerngedanke dieses Systems ist die räumliche Entkopplung der Maschineneinheiten zur Bauteilproduktion sowie für Auf- und Abrüstvorgänge. Diese Aufgaben können dank der modularen Architektur parallel und räumlich getrennt voneinander durchgeführt werden. In diesem Konzept ist es möglich, eine beliebige Anzahl von Maschinen miteinander zu verknüpfen, sodass voll automatisierte Maschinennetzwerke entstehen, die untereinander Daten austauschen.
Das Konzept setzt den Leitgedanken ›Industrie 4.0‹ auf überzeugende Weise um. Das Lasersystem arbeitet mit vier Laserquellen, wobei mehr Laser dabei grundsätzlich denkbar sind, und ermöglicht in der Summe seiner Eigenschaften die wirtschaftliche Serienproduktion additiv gefertigter Metallbauteile. Als Zielgruppe haben wir alle Branchen im Fokus, die Serienteile herstellen. In Zukunft möchten wir alle wesentlichen Prozesse, wie etwa das Trennen der aufgebauten Bauteile, das Absaugen nicht benötigten Pulvers oder das Vermessen der erzeugten Bauteile voll automatisieren, sodass eine wirklich autonome Produktion gegeben ist.
GE ist übrigens ein großer Kunde von uns, der mit Begeisterung unsere Technik seit Anbeginn einsetzt. Die dort gesammelten Erfahrungen werden in unsere Maschinen einfließen, stehen demnach später allen unserer Kunden zur Verfügung.
Wird die Additive Fertigung Auswirkungen auf die Zahl der Beschäftigten haben?
Herzog: Über diese Frage haben schon die alten Weber nachgedacht, die durch das Aufkommen des automatischen Webstuhls um ihr Arbeitseinkommen fürchteten. Die Aufregung war umsonst, denn sie fanden in den neu entstandenen Fabriken bessere Arbeitsbedingungen und höheren Lohn vor. Nicht anders wird es bei der Additiven Fertigung sein. Sicher werden anderswo, etwa in der herkömmlichen Produktion von Gussteilen, Arbeitsplätze wegfallen, doch werden viele neue Arbeitsplätze bei Unternehmen entstehen, die Teile via additiver Fertigung herstellen.
Dazu werden Fachkräfte benötigt, die sich mit der Additiven Fertigung auskennen, und die für das Wachstum dieser neuen Technologie benötigt werden! Nicht vergessen werden darf, dass auch Konstrukteure benötigt werden, die in der Lage sind, additiv zu denken. Auf diese Weise wird es möglich, Produkte einfacher und somit günstiger hinsichtlich der Stückkosten zu machen.
In welche Richtung wird Concept Laser die Idee der additiven Fertigung weiterentwickeln?
Herzog: Wir werden den bereits eingeschlagenen Weg weitergehen und neue Modelle entwickeln, die es erlauben, noch größere Bauteile additiv herzustellen. Natürlich feilen wir an der Geschwindigkeit, noch schneller zum Teil zu kommen, sowie an den Parametern, um die Stückkosten noch weiter zu senken. Hier sind wir schon ein ganzes Stück vorangekommen. Lagen die Kosten für die Maschinenstunde im Jahre 2001 bei rund 80 bis 100 Euro pro Stunde, so ist diese heute auf rund 20 bis 25 Euro pro Stunde gesunken.
Konnten im Jahre 2001 nur Bauteile mit einem Volumen von einem Kubikzentimeter pro Stunde hergestellt werden, so schaffen wir heute, beim Ausreizen von zum Beispiel ›Aluminium-Parametern‹, sogar 126 Kubikdezimeter. Das Modell ›Project A.T.L.A.S.‹ wird sogar einen derart großen Bauraum bieten, der es erlaubt, Teile zu produzieren, die einen ganzen Kubikmeter einnehmen. Unser Ziel ist demnach das immer schnellere und kostengünstigere Herstellen von Teilen, die gerne auch größer sein dürfen.
Herr Herzog, vielen Dank für das sehr interessante Interview.
Mehr Informationen zu Concept Laser:
![]() |
CONCEPT Laser GmbH |
![]() |
An der Zeil 8 |
![]() |
96215 Lichtenfels |
![]() |
Tel.: +49 (0) 9571 / 949-238 |
![]() |
Fax: +49 (0) 9571 / 949-239 |
![]() |
E-Mail: info@concept-laser.de |
![]() |
www.concept-laser.de |
War dieser Artikel für Sie hilfreich?
![]() |
![]() |
![]() |
![]() |
![]() |
Bitte bewerten Sie diese Seite durch Klick auf die Symbole.
Zugriffe heute: 2 - gesamt: 2878.