Mit Kanban zum Produktionserfolg
Fertigungssteuerung mit Köpfchen
PPS- und ERP-Systeme werden als notwendig angesehen, eine Fertigung optimal zu gestalten. Prof. Dr. Markus Schneider, Geschäftsführender Gesellschafter der PuLL Beratung GmbH und Leiter des Technologiezentrums PULS der Hochschule Landshut, legt hingegen faktenreich dar, dass ein Kanban-System die Trägheit dieser Systeme überwindet, demnach für Unternehmen der Königsweg ist, eine schlagkräftige, flexible Produktion aufzuziehen.
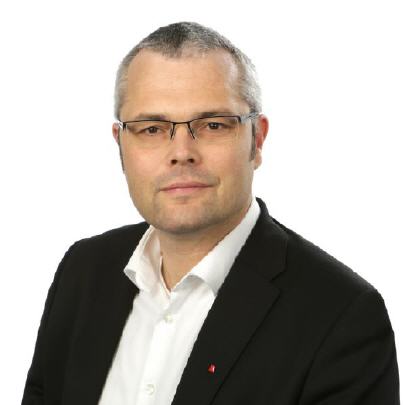
Sehr geehrter Herr Prof. Schneider, Hersteller von reinen PPS- und ERP-Systemen versprechen, dass die Produktion mit ihren Softwareprodukten effizienter und wirtschaftlicher wird. Stimmen Sie dem zu?
Prof. Markus Schneider: Sicher leisten PPS-Systeme einen Beitrag zur Optimierung der Produktion und schaffen eine gewisse Transparenz. Andererseits machen sie Unternehmen auch unflexibel. Prozesse werden nicht optimiert, da der Aufwand für die Pflege der Systeme gescheut wird oder das PPS-System bestimmte Prozesse nicht abbilden kann. Wenn Sie wirklich radikale Prozessverbesserungen erreichen wollen, müssen Sie eben diese Gegebenheiten, also das dahinter liegende Produktionssystem und die Werksstrukturen, verändern. Das Kernproblem heutiger ERP- und PPS-Systeme ist, dass sie letztlich für Unternehmen in Verkäufermärkten entwickelt wurden.
Das heißt, für Situationen geringer Varianz, frei definierbarer Liefertermine und lokaler Kostenoptimierung durch Maximierung der Auslastung. Die zu Grunde liegende Push-Logik (schieben/drücken von Arbeitsgang zu Arbeitsgang) ist in dieser Situation sicherlich die beste Steuerungsmöglichkeit der Wirtschaftlichkeit. Leider befindet sich heutzutage kaum noch ein Unternehmen in einem Verkäufermarkt. In heutigen Käufermärkten gelten diametral entgegensetzte Rahmenbedingungen, die fast alle Unternehmen zu spüren bekommen haben (Varianz, Termindruck, kurze Lebenszyklen). Die Lösung dafür kann nicht in tayloristischen Push-Systemen liegen.
Es gilt, den Wandel zu Pull-gesteuerten Systemen – wie einem Kanban-System – zu vollziehen, um wettbewerbsfähig zu bleiben. Bestände müssen daher definiert und kontrolliert werden. Je nach Wertstrom bedeutet dies den Einsatz von Kanban, Conwip oder Drum-Buffer-Rope. Diese Pull-Systeme garantieren kurze Durchlaufzeiten, hohe Termintreue und geringen Kapitalbedarf.
Dann ist eine Investition in derartige Softwareprodukte demnach nicht sinnvoll?
Prof. Schneider: Ich hatte gerade wieder den Fall, dass ein Unternehmen mit erheblichen Problemen in der Produktion kämpft: Teile fehlen, es treten beträchtliche Suchzeiten auf, Aufträge werden ständig umsortiert und die Termintreue sinkt. Die Lösungsidee des Managements ist, einen Masteranden einen Anforderungskatalog für ein PPS-System schreiben zu lassen und dann in einem Benchmark ein PPS-System auszuwählen.
Dieses Vorgehen wird keines der oben genannten Probleme lösen, sondern vielmehr zu einer Fehlinvestition in Millionenhöhe führen. Das Problem liegt in den Prozessabläufen und den Werkstrukturen, die an die Anforderungen eines Käufermarktes angepasst werden müssen. Darauf hat das PPS-System aber keinerlei Einfluss, vor allem dann nicht, wenn Sie das heutige IST-System einfach 1:1 in der Software abbilden. Die Erfolgswahrscheinlichkeit ist wesentlich höher, wenn Sie zuerst die Prozesse „gerade ziehen“ und dann die passende Software aussuchen. Sollten Sie sich entscheiden, Ihre Prozesse Lean zu gestalten, so bleiben nur sehr wenige PPS-Systeme übrig, die das wirklich unterstützen.
Was sind die größten Unzulänglichkeiten dieser Programmgattung?
Prof. Schneider: Wie ich bereits ausgeführt habe, liegt der Kern des Problems darin, dass die ERP-/PPS-Systeme für einen heute praktisch nicht mehr existenten Verkäufermarkt entwickelt wurden. Zunächst einmal basieren ERP/PPS-Systeme auf Schätzungen zu Bedarfen. Obwohl dies in heutigen Käufermärkten schlicht nicht machbar ist, betreiben viele Unternehmen einen hohen Aufwand zur Bedarfsschätzung, anstatt zu hinterfragen, ob das Problem nicht auch anders lösbar sei. Weiterhin versuchen PPS-Systeme die Produktion durch das Einstellen von „Planaufträgen“, „Nettobedarfsrechnung“ et cetera zu „optimieren“. Hinzu kommt, dass Kundenaufträge „zerrissen“ und auf Baugruppenebene in Losgrößen gefertigt werden.
Dahinter steht die Grundidee der „Economies of Scale“, dass es günstiger sei, große Mengen ein und derselben Baugruppe in höheren Stückzahlen zu fertigen. Der Effekt hieraus allerdings ist, dass die realen Kundenaufträge nicht mehr erkennbar sind. Dies mag ja alles richtig sein, jedoch nur, wenn einerseits alle Absatzprognosen, andererseits alle in die Berechnungen eingehenden Daten stimmen würden. Leider ist beides in der Praxis eher selten der Fall. Prognosen zu Verkaufszahlen sind oft falsch und die Datenqualität in den meisten Unternehmen, die ich kenne, ist schlecht bis sehr schlecht. Somit sind zwangsläufig auch die mit den PPS-Systemen erarbeiteten Pläne von geringer Aussagekraft.
Wir kennen alle die alte EDV-Regel: shit in – shit out. Es besteht die große Gefahr, Kapazitäten für Produkte und Baugruppen einzusetzen, die im Moment gar nicht notwendig sind. Dies führt zu hohen Beständen von bestimmten Baugruppen , während andere, die dringend gebraucht werden würden, nicht vorhanden sind. ERP-Systeme verwenden meist fest definierte Losgrößen beispielsweise auf Basis der Andler’schen Formel oder einfacher Schätzungen. Die Konsequenzen sind hohe Bestände und lange Liegezeiten. Aus unserem Verständnis ergeben sich die Losgrößen jedoch vor allem aus der zur Verfügung stehenden Kapazität und der aktuellen Nachfrage. Das Zeitdelta wird genutzt, um so oft wie möglich zu Rüsten und Losgrößen zu reduzieren (Stichwort EPEI). Die Losgröße ist somit nicht Eingangsparameter, sondern Ausgangsparameter der Planung. Dies beherrschen ERP-Systeme aber nicht.
Zur Start- und Endterminierung werden starre Liege- und Übergangszeiten zwischen Arbeitsgängen verwendet. Diese Übergangszeiten werden geschätzt und als Pufferzeiten eingetragen. Die Übergangszeiten machen aber 80 bis 95 Prozent der gesamten Durchlaufzeit eines Produktes durch das Unternehmen aus. PPS-Systeme wollen alles Mögliche optimieren, aber 80 bis 95 Prozent der Durchlaufzeit – ein aus Lean-Sicht absolut entscheidender Faktor, um schnell beim Kunden zu sein – werden weder überwacht noch systematisch reduziert. Ein weiteres Problem dieser Vorgehensweise ergibt sich daraus, dass sowohl bei Voll- als auch bei Unterauslastung die gleichen Liegezeiten verwendet werden. Liegezeiten sind aber eine Funktion von Kapazität und Nachfrage und damit der Auslastung! In Zeiten hoher Auslastung nehmen Liegezeiten zu, da sich Engpässe für den Durchsatz bilden.
Die Start- und Endtermine am Engpass und an flussabwärts liegenden Prozessen können dann nicht eingehalten werden und das Chaos wird perfekt. Ohne einen „Terminjäger“ funktioniert schließlich gar nichts mehr. Die meisten ERP-/PPS-Systeme berücksichtigen bei der Planung Engpässe meist gar nicht oder nur rudimentär. Werden die Freigabemengen jedoch nicht in Abhängigkeit des aktuellen Engpasses geregelt, so sind die hinterlegten Liegezeiten sinnlos. Die Terminierung kann nicht eingehalten werden und die tägliche Feinplanung gleicht mehr einem „Brände löschen“. Ein weiteres Manko ist, dass die Berechnungen auf Basis all dieser Eingangsdaten sehr aufwendig sind und meist einen Nachtlauf erfordern. Denn wie soll eine immer volatilere Produktionswelt, die schnelle Entscheidungen und Anpassungen im Stunden- oder gar Minutenbereich erfordert, mit einem System gesteuert werden, das nur einmal am Tag eine „optimale“ Produktionsreihenfolge ausspuckt?
ERP-/PPS-Systeme gaukeln demnach eine perfekte Scheinwelt vor?
Prof. Schneider: Sie stellen jedenfalls in den meisten Fällen nicht die reale Welt und schon gar nicht in Echtzeit dar. Die Frage ist nur, wie weit die datenbasierte PPS-Welt von der realen Welt entfernt ist. Problematisch ist aus meiner Sicht zu sehen, dass viele Lösungsansätze, wie etwa APS (Advanced Planning Systems) dann vorgaukeln, die Lösung läge in der Erfassung von noch mehr Parametern und noch höherer Datengenauigkeit. Ich bezeichne das als ›Just Push Harder‹!
Dieses in der Theorie vielleicht funktionierende Konstrukt gerät jedoch in volatilen Käufermärkten mit unbekannten Parameterausprägungen schnell an seine Grenzen. Komplexität lässt sich schlicht und ergreifend nicht mit noch mehr Komplexität beherrschen. In der Praxis ist das Chaos mit APS meist noch größer als ohne. Hier setzt Kanban an. Anstatt das Problem zu lösen (genauere Planungsparameter), löst es sich vom Problem, in dem die Logik umgekehrt wird. Das bedeutet von einer prognosebasierten Bedarfssteuerung auf eine Verbrauchssteuerung umzusteigen.
Wie funktioniert Kanban?
Prof. Schneider: Ein PPS-System versucht üblicherweise zentralistisch alle relevanten Daten zu sammeln und eine optimale Produktionsreihenfolge zu erstellen, die sowohl künftige Bedarfe als auch zahlreiche Restriktionen, wie etwa Rüstreihenfolgen, berücksichtigt. Diese optimale Reihenfolge wird dann durch das Produktionssystem „geschoben“. Wir sprechen von einer Push-Steuerung. Kanban dreht diese Logik quasi um. Da Prognosen naturgemäß nie exakt stimmen, wird versucht, ganz ohne Prognosen auszukommen.
Kanban ist eine „Verbrauchssteuerung“. Das bedeutet, dass ein mithilfe einer Kanban-Formel zu bestimmender Bestand vorhanden ist und in der Folge einfach nur das wieder ersetzt wird, was verbraucht wurde. Wir sprechen dann auch von einer Pull-Steuerung, da die Aktion vom Verbraucher, von der Senke ausgeht. Niemand auf der Welt, auch kein PPS-System, weiß genau, was der Werker in der Montage an Material verbraucht hat, außer dem Werker selbst. Also lassen wir ihn doch auch den Nachschub steuern.
Für welche Betriebsgrößen ist Kanban geeignet?
Prof. Schneider: Die Eignung von Kanban hat nichts mit der Unternehmensgröße zu tun. Kanban eignet sich auch für den eigenen Haushalt oder das Büro. In meinem Forschungsinstitut steuern wir den Nachschub von fast allem, vom Kopierpapier bis zu den Servietten mit Kanban. Wenn zehn Packungen verbraucht wurden, werden wieder zehn nachbeschafft und das vorhandene Material muss so lange reichen, bis die Nachbeschaffung eingetroffen ist. Sehr einfach, komplett ohne EDV und absolut zuverlässig. Es sollte allerdings beachtet werden, dass Kanban nicht für alle Teilearten geeignet ist. Kanban funktioniert am besten für sogenannte CXN-Teile: also Teile, die relativ günstig sind (C), regelmäßig gebraucht werden (X) und in nicht allzu vielen Varianten bevorratet werden müssen (N).
Welchen besonderen Vorteil hat Kanban?
Prof. Schneider: Der besondere Vorteil aus meiner Sicht ist, dass Kanban ein sehr komplexes Gesamtsystem in viele kleine sich selbst steuernde Regelkreise zerlegt. Es wird also ganz im Gegensatz zu den PPS-Systemen eben nicht zentralistisch versucht, alles zu optimieren, sondern man zerlegt das System in viele kleine, unabhängige Teilsysteme. Außerdem wird, wie bereits erwähnt, die Energie nicht darauf verwendet, die Prognosen genauer zu machen, sondern ohne Prognosen, die ohnehin nicht stimmen, auszukommen.
Was ist bezüglich der Kanban-Einführung in Sachen ›Abteilungsstruktur‹ zu beachten, damit Kanban ein Erfolg wird?Prof. Schneider: Ich denke, dass es am Anfang eine zentrale Einheit oder einen externen Partner geben muss, die/der das Wissen rund um Kanban aufbaut und vermittelt, aber die Verantwortung dann dezentral bei den Produktionsabteilungen liegt. Insofern sehe ich keine weitere Auswirkung auf die Abteilungsstruktur.
Was ändert sich bezüglich der Verantwortlichkeit? Konkret: Wer ist dafür verantwortlich, damit in einem Kanban-System die Unternehmensziele erreicht werden?
Prof. Schneider: Die Verantwortung für den Betrieb liegt dezentral bei den Mitarbeitern vor Ort. Auch das sehe ich als großen Vorteil von Kanban. Die jeweiligen Mitarbeiter vor Ort müssen die wenigen Kanban-Regeln einhalten und bei Veränderungen neu justieren. In der heutigen schnelllebigen, komplexen Welt helfen so mehr Köpfe mit, das System am Laufen zu halten. Das wäre zentral, mit der Zeitverzögerung der Erfassung der Daten und all den Unzulänglichkeiten von deren Qualität,kaum möglich.
Wenn Sie nach der Verantwortung für die Wirtschaftlichkeit, also die gezielte Reduzierung der Bestände in den Kanban-Systemen fragen, dann liegt die Verantwortung nicht bei der Produktion und der Logistik. Betrachten Sie einmal die wirklich relevanten Eingangsparameter, die die Bestände massiv in die Höhe treiben, dann liegen diese vielmehr im Einflussbereich des Einkaufs, des Vertriebs und der Technischen Entwicklung.
In einer Kanban-Umgebung sollten die Fertigungssegmente als Eigenbetriebe organisiert werden. Welche Vorteile ergeben sich dadurch?
Prof. Schneider: Wie ich bereits vorher schon einmal ausgeführt habe, wird damit ein ausgesprochen komplexes Gesamtsystem in viel einfacher zu beherrschende Teilsysteme zerlegt. Diese agieren selbstständig, wie Eigenbetriebe.
Gibt es auch bezüglich der Arbeitszeit etwas zu beachten?
Prof. Schneider: Ja, die Arbeitszeiten zwischen Quelle und Senke müssen einigermaßen synchronisiert sein. Sprich: Kanban kann nur bedingt funktionieren, wenn die verbrauchende Abteilung um 6 Uhr die Arbeit beginnt, die nachliefernde aber erst um 07.30. Oder aber eine Abteilung zweischichtig arbeitet und andere einschichtig.
Noch vor wenigen Jahrzehnten war es üblich, einen Arbeitsgang sehr kurz – beispielsweise ›Drehen nach Zeichnung‹ – festzulegen. Heute werden Arbeitspläne immer detaillierter ausgeführt, was zu unnötig großem Zeitaufwand führt. Gilt in einer Kanban-Umgebung demnach die Devise ›zurück in die Zukunft‹, da in diesem System Arbeitspläne so kurz wie möglich auszufallen haben?
Prof. Schneider: Damit Kanban funktioniert, muss die Wiederbeschaffungszeit festgelegt werden. Diese bedingt die maximale Länge für den Arbeitsplan. Wenn in einer Stunde ein Behälter mit 20 Teilen verbraucht wird, muss dieser Behälter auch in einer Stunde wieder mit 20 Teilen befüllt werden können. Die Länge des Arbeitsplans spielt keine Rolle, solange dieser Zusammenhang eingehalten wird. Ansonsten gilt, dass der Arbeitsplan verständlich sein muss.
Wie sollte der Stücklistenaufbau in einer Kanban-Organisation aussehen?
Prof. Schneider: Ich sehe keinen besonderen Zusammenhang zwischen dem Stücklistenaufbau und Kanban. Generell ist zu sagen, dass das klassische Refa-Verfahren des ›strukturierten Stücklistenprinzips‹ bewusst Baugruppen in der Stückliste erzeugt, während Lean mit dem ›Prinzip flache Stückliste‹ versucht, Baugruppen zu vermeiden. Was aber sehr wohl einen Einfluss auf die Einsetzbarkeit von Kanban hat, ist der Varianzbildungs- oder Einsteuerungspunkt, auch Schrittmacher oder Kundenentkopplungspunkt genannt. Alles hinter diesem Punkt kann nur noch gepusht und nicht mehr mit Kanban gepullt werden, da ansonsten die Reihenfolgeinformation verloren geht.
Der Schritt zu geringeren Stückzahlen im Kanban-System bedingt auch steigende Rüstkosten. Sehen Sie hier ein Problem?
Prof. Schneider: Die Losgrößen werden durch den EPEI (Every-Part-Every-Intervall) berechnet und haben nur indirekt mit Kanban zu tun. Tatsächlich sieht Lean aber die Prozessoptimierung in der Reduzierung der Rüstzeit und nicht in der möglichst geschickten, wie auch immer gearteten Losgrößenberechnung. Die vielen Losgrößenoptimierungsalgorithmen in unseren PPS-Systemen sind aus Lean-Sicht eine Optimierung am eigentlichen Problem vorbei.
Was ist in der Lagerlogistik zu ändern, wenn künftig nach den Kanban-Regeln gearbeitet werden soll?
Prof. Schneider: Die Lagerlogistiker müssen die Kanban-Regeln verstanden haben. Es darf nur nachgeliefert werden, wenn etwas verbraucht wurde und so viel wie verbraucht wurde. Wichtig ist also, dass dieselbe Person, die die leeren Behälter in der Montage (an der Senke) abholt, auch die Befüllung übernimmt und in der gleichen Reihenfolge wieder an der Senke anliefert. Wir hatten einen Fall, da hat sich das Unternehmen beschwert, dass Kanban nicht funktionieren würde.
Der Grund war ein zweistufiges System. Ein Logistiker holte die leeren Behälter an der Montagelinie ab und hat diese vor dem Lager auf Tische gestellt. Nach wenigen Umläufen war für den Lagerist nicht mehr erkennbar, welche Behälter neu dazugekommen sind oder schon lange dastanden. Der Effekt war natürlich, dass Teile schon ausgelagert wurden, die erst gerade angefordert worden waren und andere Behälter nach Stunden Wartezeit bereits an der Montagelinie ausgegangen sind. Es musste also entweder auf ein einstufiges Verfahren umgestellt werden oder zumindest die Reihenfolge der Ankunft der zu befüllenden Behälter erkennbar sein.
Die ABC-Analyse ist eine wichtige Dispositionsgrundlage. Ändert sich hier etwas, wenn nach Kanban gearbeitet wird?
Prof. Schneider: An der Logik der ABC-Analyse an sich nicht, aber wie bereits vorher ausgeführt, ist Kanban vorwiegend für CXN-Teile geeignet. Um diese Analysen regelmäßig zu fahren, ist die Unterstützung eines entsprechend Lean-fähigen PPS-Systems durchaus hilfreich.
IT-gestützte Bestandführungsverfahren verursachen einen hohen Pflegeaufwand für die Daten. Wie kann Kanban hier helfen, die Kosten zu senken?
Prof. Schneider: Sie benötigen für Kanban zunächst kein IT-System und müssen demnach auch die Daten nicht in einem zentralen System pflegen. Ein Kanban-System erfordert wesentlich weniger Daten und ist außerdem deutlich fehlertoleranter als ein zentrales Push-System. Natürlich kann ein Lean-kompatibles PPS-System bei der ständigen Überwachung vieler Kanban-Kreisläufe eine erhebliche Entlastung bieten.
Sind eigentlich alle Teilemengen für eine Produktion nach Kanban geeignet oder gibt es eine maximale Menge, die nicht überschritten werden sollte?
Prof. Schneider: Die Teilemenge kann ›ein Teil‹ sein oder auch ein Behälter oder eine Palette. Ein Kanban kann aber auch ein ganzer Sattelzugauflieger sein, beispielsweise werden in der LKW-Montage so die recht großen Cockpits angeliefert. Ist ein Auflieger leer, wird ein neuer angeliefert. Weit über diese Größe hinaus ist mir allerdings keine Kanban-Menge bekannt.
Ist zur Nutzung von Kanban eine EDV-Anlage nötig?
Prof. Schneider: Ab einem gewissen Umfang von Kanban-Kreisläufen macht eine Softwareunterstützung zur Kalkulation und ständigen Überwachung und Anpassung der Kanban-Kreisläufe Sinn. Für einen Start ist das aber nicht notwendig.
Demnach werden vorhandene PPS-/ERP-Systeme überflüssig?
Prof. Schneider: Kanban funktioniert ganz ohne EDV. PPS-Systeme bieten aber durchaus Vorteile. Wichtig ist aber, dass das gewählte PPS-System Lean-fähig ist und die Herstellerfirma die Lean-Philosophie verstanden hat. Ansonsten prallen hier Denkwelten aufeinander, die zu inkonsistenten und nicht funktionierenden Systemen führen. Ich muss aber sagen, dass aus meiner Erfahrung nur sehr wenige PPS-Systemhersteller die Lean-Denkweise verinnerlicht haben.
Welcher benötigte Zeitraum ist ins Auge zu fassen, wenn ein Unternehmen Kanban einführen möchte?
Prof. Schneider: Suchen Sie nicht nach Gründen warum Kanban bei Ihnen nicht funktioniert, sondern suchen Sie nach Teilen, mit denen Kanban funktionieren kann. Kanban wird nie mit allen Teilekategorien funktionieren. Starten Sie dann mit ausgewählten Kreisläufen und lernen Sie. Dehnen Sie das System nach den ersten Erfolgen im Unternehmen aus. Ich denke hier ist der Hinweis angebracht, dass nicht Kanban, sondern ›Pull‹ das Entscheidende ist. Kanban ist nur eine Form einer Pull-Steuerung. Andere Ausprägungen wären beispielsweise Golfball-Steuerung, Conwip, Polca und Drum-Buffer-Rope. Hier für jedes Unternehmen eine individuelle Werkzeugauswahl vorzunehmen, erfordert viel Erfahrung. Dafür wären wir der richtige Partner.
Was gibt es zu beachten?
Prof. Schneider: Beachten Sie die Kanban-Regeln. Bei Teilen mit unregelmäßigem Verbrauch oder hohen Ausschussquoten kann Kanban nicht funktionieren. Legen Sie die Kanban-Bestände nicht zu gering aus. Es wäre „Wasser auf die Mühlen“ der Kanban- und Lean-Gegner, wenn Sie die Endmontage wegen fehlender Dichtringe für ein paar Cent abstellen müssten. Rechnen Sie mit dem Sicherheitsfaktor von mindestens ›2‹ und ziehen Sie die Bestände dann systematisch nach unten.
Herr Prof. Schneider, vielen Dank für das Interview.
Mehr Informationen zur PuLL Beratung GmbH:
![]() |
PuLL Beratung GmbH |
![]() |
Schweriner Str. 1 |
![]() |
84036 Landshut |
![]() |
Tel.: 0871/95347394 |
![]() |
E-Mail: info@pull-beratung.de |
![]() |
www.pull-beratung.de |
War dieser Artikel für Sie hilfreich?
![]() |
![]() |
![]() |
![]() |
![]() |
Bitte bewerten Sie diese Seite durch Klick auf die Symbole.
Zugriffe heute: 1 - gesamt: 3043.