Die Art der CO2-armen Produktion
Umweltschutz und Profit vereint
Der Europäische Rat unterstützt den ›Green New Deal‹ der EU-Kommission und fordert einen konkreten Aktionsplan um bis zum Jahr 2050 Klimaneutralität zu erreichen. Das Unternehmen Diebold hat mit seiner modernen Gebäudetechnik diese Ziele jetzt schon erreicht, wie Hermann Diebold im Interview erläutert.
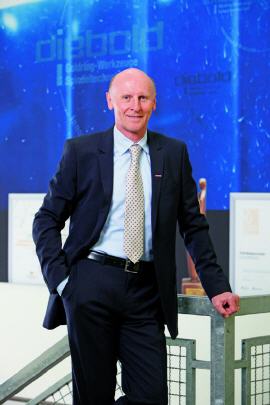
Hermann Diebold, GF der Helmut Diebold GmbH & Co.
Sehr geehrter Herr Diebold, Ihr Unternehmen stellt unter anderem hochgenaue Werkzeughalter her. Dazu ist eine klimatisierte Fertigung nötig, damit die besonders engen Toleranzen sicher eingehalten werden können. Ist die dazu nötige Klimatechnik nicht sehr energieintensiv?
Hermann Diebold: Wir setzen bedingungslos auf höchste Genauigkeiten und kleinste Toleranzen. Dafür betreiben wir schon seit 2006 eine vollklimatisierte Fertigung, die benötigte Kühlenergie wird sehr energiearm erzeugt. Die Kälteleistung wird zu 80 Prozent aus sogenannter freier Kühlung (nur mit Luft) erzeugt, kombiniert mit Flusswasser das wir für Kühlzwecke aus dem in der Nähe vorbeifließenden Bach mit freundlicher Genehmigung der Behörden entnehmen dürfen. In den warmen Sommermonaten, wenn die Temperatur selbst nachts nicht unter 12 Grad fällt – was bei uns nur maximal 2 Monate im Jahr der Fall ist – läuft ergänzend zur freien Kühlung ein Klimagerät mit. Die Produktionsgebäude werden mit Fußbodenheizung temperiert, die Wärme dafür kommt aus der Abwärme der Kompressoren in der Fertigung. Heizen, eher gesagt das Halten der Temperatur, erfolgt durch Wärmerückgewinnung mit sehr hohem Wirkungsgrad.
Was muss gegeben sein, damit dieses Konzept funktioniert?
Diebold: Dazu müssen die Produktionshallen eine geschlossene Hülle haben, zudem ist es nötig, jede Stunde die gesamte Luft in den Hallen zu tauschen. Im Jahre 2019 haben wir uns aufgrund der guten Erfahrung in der modernen Produktionshalle entschlossen, auch die Bestandsgebäude in das Klima-Lüftungs-System zu integrieren. Das Ganze ist natürlich nicht umsonst zu haben und diese Kosten müssen auf die Produkte umgelegt werden. Aber wenn man hochgenaue Produkte herstellen will, ist dieser Weg Pflicht.
Die Technik mit Heizungs- und Kühlungsanlage ist regelungstechnisch sicher sehr aufwendig. Welches Konzept wurde hier umgesetzt?
Diebold: Die Regelungstechnik ist sicher aufwändig, alles muss verkabelt werden damit Signale an der zentralen MSR (Mess-Steuer-Regelungstechnik) ankommen. Der Komfort ist aber ganz toll. Wir sehen alle Pumpen, Wasser- und Luft-Kreisläufe, Temperaturen und vor allem auch Störungen am zentralen PC. Wir müssen also nicht ständig in den Keller laufen um die einzelnen Geräte zu prüfen. Eine sogenannte Hausmeistertätigkeit entfällt komplett. Im Gegenteil: der Administrator wird per App informiert wenn eine Störung ansteht – auch am Wochenende oder am Abend. Er kann sie dann beseitigen oder einen Mitarbeiter, der in der Firma vor Ort ist, beauftragen, für die Störungsbeseitigung zu sorgen. Das kommt aber keine fünf Mal im Jahr vor. In der Klimahalle wird übrigens überhaupt nicht geheizt sondern nur gekühlt. Die anderen Hallen sind so ertüchtigt worden, dass über die Wärmerückgewinnung ein Wirkungsgrad von 96 Prozent erreicht wird, also 96 Prozent weniger Heizkosten und damit auch 96 Prozent weniger Co2-Ausstoß. In der ganzen Fabrik gibt es schon seit 2012 keine Brennstellen mehr, die mit Öl oder Gas betrieben werden. Der Co2-Ausstoß durch Heizen wurde demnach auf Null reduziert. Die wenige Wärme, die wir zum Heizen noch brauchen, beziehen wir von der Bio-Energie Killertal, unserem Nachbarn, der Wärme aus nachwachsenden Rohstoffen erzeugt. Wir können also mit Fug und Recht von einer „klimaneutralen Produktion“ sprechen. Mit diesem Konzept sind wir der Zeit weit voraus und können heute schon und sicher auch zukünftig alle Klimawirksamen Bedingungen erfüllen.
Es ist schon lange bekannt, dass eine klimatisierte Fertigung eine absolute Pflicht für hochgenaue Werkzeugaufnahmen ist. Immer wieder werden jedoch Klagen laut, die von ungenauen Werkzeugaufnahmen berichten. Wie ist Ihr Eindruck vom Marktumfeld?
Diebold: Hochgenaue Werkzeugaufnahmen herzustellen, ist teuer. In unserem Wettbewerbsumfeld sind viele Konkurrenzprodukte auf dem Markt, die nicht die Anforderungen der DIN/ISO Normen an ihre Genauigkeit erfüllen. Viele Anwender kaufen in gutem Glauben beim Händler ihres Vertrauens. Allerdings haben Händler nicht viele Möglichkeiten, die versprochenen Genauigkeiten der von ihnen verkauften Werkzeughalter zu prüfen. Da wir auch Messgeräte für das Vermessen von Werkzeughaltern herstellen, bieten wir die Überprüfung der beim Anwender vorhandenen Werkzeughalter als Dienstleistung an, was spätestens dann notwendig ist, wenn der Kunde Zerspanungsprobleme hat und nach den Ursachen dafür forschen muss. Das Ergebnis dieser Messungen ist erschreckend, weil nach unserer Erfahrung im Durchschnitt 30 Prozent der eingesetzten Werkzeughalter nicht die Genauigkeiten erfüllen, die die Norm fordert. Von besserer Genauigkeit ganz zu schweigen. Möchte der Anwender aber mit genauen, normgerechten Werkzeughaltern arbeiten, dann muss er diese 30 Prozent der Werkzeugaufnahmen neu beschaffen. Was für eine Verschwendung von Ressourcen und Geld!
Wie gestaltete sich Ihr Weg, eine Fabrik zu betreiben, die mühelos in der Lage ist, hochgenaue Werkzeugaufnahmen zu produzieren?
Diebold: Bevor wir unsere Klimatisierte Fabrik hatten, mussten wir enormen Aufwand betreiben, um Produkte toleranzhaltig hinzubekommen. An verbesserte Genauigkeit war gar nicht zu denken. Aus heutiger Sicht nennen wir das „abenteuerliches Arbeiten“. Wenn wir Glück hatten, haben die Werkstücke die damals schon klimatisierte Qualitätssicherung passiert und die gewünschte Genauigkeit erreicht. Wir hatten damals auch noch das klassische Lüftungskonzept indem man Fenster, Türen und Tore geöffnet hat um zu lüften und die Temperatur in der Fertigung erträglich zu halten. Viel Ausschuss und Nacharbeiten waren an der Tagesordnung. Ein Teiletourismus zum Aufchromen und erneuten Schleifen war oft notwendig. Zugesagte Termine konnten dann nicht gehalten werden und die Kostenrechnung für Bauteile wurde deutlich schlechter. Dies war unsere erste Motivation in eine vollklimatisierte Fertigung zu investieren.
Wie wurde dieser Gedanke umgesetzt?
Diebold: Der Energiespargedanke wurde erst in der Planungsphase Realität, nachdem wir erfahrene Planer gefunden hatten, die ihr Handwerk verstehen. Nachdem sich unser Konzept herumgesprochen und interessierte Firmen bei uns nachfragten, wie es funktioniert, haben wir gelernt, dass auf diesem Gebiet auch viele unerfahrene Berater, Planer und Errichter unterwegs sind. Wenn ein neu erstelltes Gebäude und sein Klimakonzept nicht funktionieren, ist das fatal. Wir werden immer wieder um Rat gefragt, was dann zu tun wäre, um das Ganze noch zu retten. Hohe Kosten sind dann die Folge für den Betreiber.
Effizienzsteigerungen in der Fertigung sind mit einer guten Organisation möglich. Sehen Sie hier noch viel Potenzial?
Diebold: In den vergangenen Jahren hat man sich vorwiegend mit Hauptzeitverbesserungen und Reduzierung der Nebenzeiten befasst. Das Thema ist ziemlich ausgereizt, jetzt muss man andere Hilfsmittel nutzen, wie etwa die Digitalisierung, um Kosten zu drücken. Damit Produktionsbetriebe ihre Maschinen schnell umrüsten können, stellen wir ihnen digitalisierte Werkzeugverwaltungssystem zur Verfügung, mit denen sie die Wartezeiten ihrer Maschinen minimieren können. Systeme, die es sogar ermöglichen, damit ganze Maschinen einzusparen. Das ist dann auch im Sinne der Nachhaltigkeit.
Von welcher Produktivitätserhöhung sprechen wir hier?
Diebold: Eine Produktivitätserhöhung um 30 Prozent ist auf jeden Fall zu erwarten. Jedes Unternehmen ist gefordert, ständig seine Effizienz zu steigern, um sich wirtschaftlich zukunftsfähig aufzustellen. Das liegt vor allem am immer weiter steigenden Wettbewerbsdruck. Die Aufgabe der Werkzeugindustrie ist es deshalb, Nachhaltigkeit und Effizienz für die Kunden zu vereinen. Vor allem für Lohnfertiger macht das einen großen Unterschied. Hier rüsten die Fertigungsbetriebe für wechselnde Bauteile oft mehrmals täglich ihre Maschinen um. So ein Umrüstvorgang kann zwischen 30 Minuten und mehreren Stunden dauern. In dieser Zeit macht die Maschine keine Späne, sie steht in dieser Zeit, verdient demnach auch kein Geld. Und spätestens nach acht Stunden geht der Bediener nach Hause, weil seine Schichtzeit abgelaufen ist. Ob der Job dann fertig ist oder nicht, ist ein ganz entscheidender wirtschaftlicher Faktor.
Wie funktioniert die digitale Werkzeugverwaltung?
Diebold: Mit der digitalisierten Werkzeugverwaltung stehen jederzeit und an allen Arbeitsplätzen die gleichen Daten zur Verfügung. Dazu müssen alle Werkzeuge mit einem eindeutigen Code versehen sein. Bei uns ist das ein Data-Matrix-Code, der alle Informationen über die Werkzeugaufnahme enthält – auch die Produktionsdaten und Produktionshistorie in Form einer Lebenslaufakte. Wo sich die Werkzeuge und das Zubehör befinden, geht eindeutig aus der Datenbank hervor. Hier ist i4.0 Realität geworden. Ein Zusammensuchen und improvisiertes Zusammenbauen der Werkzeuge ohne genauen Plan ist somit Vergangenheit. Es gibt auch keine Zettelwirtschaft oder Aufkleber mehr. Das Voreinstellen der Werkzeuge – wenn nötig das Einschrumpfen von Werkzeugen oder sogar das Wuchten der zusammengebauten Werkzeuge – wird von diesem digitalisierten Prozess geführt und erledigt. Die Korrekturdaten der Werkzeuge werden anschließend direkt in das NC-Programm übertragen. Auf diese Weise wird der Mensch als Fehlerquelle eliminiert. Die Überprüfung der Positionen im Werkzeugmagazin findet automatisch durch Scannen des Data-Matrix-Codes sowie Abfrage der Position statt.
Wird in diesem Konzept auch das zu bearbeitende Werkstück einbezogen?
Diebold: Auch die aufgespannten Werkstücke werden in diesen digitalisierten Prozess integriert. Nullpunktspannsysteme – am besten gleich erweitert durch eine automatische Beladung – sind das Zauberwort. Teile auf dem Maschinetisch manuell zu spannen, kostet wertvolle Produktionszeit. Anschließendes Ausrichten jedes einzelnen Werkstücks in der Maschine kostet nochmals wertvolle Produktionszeit. Dieser Vorgang sollte außerhalb der Maschine durchgeführt werden. Die Spannmittel bekommen per Data-Matrix-Code die Daten über die Spannsituation sowie den Startpunkt für das Maschinenprogramm als Code mit. Dieser kann von der Maschine gelesen werden. Ein aufwändiges Antasten des Werkstücks in der Maschine mit teuren Tastern kann dadurch entfallen. Und falls das Werkstück auf einer anderen Maschine bearbeitet werden soll, stehen diese Daten dort ohne zusätzlichen Aufwand ebenfalls zur Verfügung. So lässt sich die Produktivität einer Anlage problemlos um 30 Prozent steigern. Dies bei einer Investition, die sich garantiert innerhalb des ersten Jahres bezahlt macht und in den Folgejahren zu enormem wirtschaftlichem Nutzen verhilft.
Was ist noch auf der Haben-Seite zu verzeichnen?
Diebold: Auch Lieferzeiten und Risiko sinken, wenn ein Bauteil mit einer klar definierten Aufspannung bearbeitet wird. Im Wiederholfall entfallen fast alle Kosten für das erneute Rüsten. Der ökologische Footprint wird verbessert, indem Ressourcen, Energie, Zeit und Platz gespart werden. Um das zu realisieren, müssen wir uns mit Organisationsmethoden beschäftigen, die uns bis dato nicht zur Verfügung standen oder einfach zu teuer waren. Das Einsparen von Rohstoffen und das Recycling der Abfälle ist heute schon Standard und birgt kein weiteres Einsparungspotenzial.
Wie steht es in Sachen Kühlschmierstoffe? Wo sehen Sie hier den Trend, mehr für die Umwelt zu tun?
Diebold: Hier sehe ich einen Nachhaltigkeitstrend im Einsatz der Minimalmengenschmierung. Statt großen Mengen an Kühlschmiermitteln auf jeder einzelnen Maschine setzt man immer häufiger auf die Minimalmengenschmierung. Für die Bearbeitung wird hier nur noch ein Hauch von Öl gebraucht, was natürlich extrem ressourcenschonend ist. Unsere JetSleeve2.0-Schrumpffutter sowie die UltraJet3.0-Kraftspannfutter ermöglichen den Einsatz von MMS anstatt Schwallspülung mit Kühlmittel. Kombiniert mit intelligenten Mischgeräten für das Schmiermittel können viele Fräsprozesse „trocken“ durchgeführt werden. Und gleichzeitig wird der Fräserverschleiß minimiert, weil das MMS mit Hochdruck an der Stirnseite der Futter austritt, dabei den Fräser schmiert sowie kühlt und vor allem die Späne wegschleudert, sobald sie brechen. Ein Überfahren der Späne ist so nicht mehr möglich. Dies führt zu weniger ungeplanten Unterbrechungen im Prozess, was zu einer deutlichen Zeit- und Energieeinsparung führt.
Wo sehen Sie das größte Energieeinsparpotenzial in Ihrem Unternehmen?
Diebold: Das größte Potenzial zur Energieeinsparung liegt in der Fertigung. Der Strombedarf eines Produktionsunternehmens liegt bei etwa 250 Euro pro Mitarbeiter und pro Monat. Das ergibt 3000 Euro pro Mitarbeiter pro Jahr. Der Heizenergiebedarf liegt in einer ähnlichen Größenordnung. Also 6000 Euro pro Mann und Jahr stehen zur Debatte von denen ein erheblicher Anteil durch bessere Technik eingespart werden kann, die auch noch hilft, die Produkte zu verbessern. Weniger Energieverbrauch bedeutet nicht nur Co2 zu vermeiden, sondern ist auch im Interesse der machbaren Kosteneinsparungen. In unserer Produktion ist dies durch das Klimakonzept bereits vorbildlich gelöst.
Vonseiten der EU beziehungsweise der Bundesregierung werden für Unternehmen immer mehr Hürden errichtet, nachhaltig zu produzieren. Was kommt auf Unternehmen zu?
Diebold: Unternehmen werden zukünftig unter anderem nachweisen müssen, wie sich die Co2-Bilanz des eingekauften Rohstahls darstellt. Dies dient als Nachweis des Co2 footprints für Rohmaterialien. Ein Verwaltungsakt der von vorneherein lean und schlank sein muss, da sonst die Produkte teurer werden, mithin ihre Wettbewerbsfähigkeit leidet.
Wie beurteilen Sie diese Eingriffe des Staates in das unternehmerische Handeln?
Diebold: Der Nutzen eines Produkts muss für den Anwender stets im Vordergrund stehen. Unnötige Auflagen verteuern diese letztlich, was Wettbewerbern aus Ländern ohne derartige Auflagen zugutekommt.
Wie sehen Sie Ihr Unternehmen auf dem Weg in die Zukunft?
Diebold: Wir bei Diebold sehen uns in der Zukunft mehr als Technologie-Partner und Effizienz-Berater, nicht nur als Lieferant für Werkzeuglösungen aus Stahl und Eisen. Die Lösung für die Digitalisierung in der Werkzeugverwaltung haben wir bereits im Programm zu überschaubaren Kosten und vor allem bei maximaler Datensicherheit, was bei fortschreitender Digitalisierung ein entscheidender Wettbewerbsvorteil sein wird. Wir verkaufen nicht nur digitale Produkte und die Maschinen und Geräte dazu, nein wir begleiten die Kunden bei der Umsetzung durch unsere erfahrenen Anwendungstechniker und Spezialisten für Fertigungsoptimierung.
Sind steigende Strompreise ein Problem für Ihre Fertigung?
Diebold: Ein ganz klares ja. In den letzten zwei Jahren sind unsere Stromkosten trotz Einsatz energiesparender Technik um 20 Prozent gestiegen. EEG Umlagen und alternative Energieerzeugung sind ja stark im Fokus der Politik, sie werden aber immer mehr hinterfragt. Fragen Sie einen Ingenieur, was er von Co2-Einsparung, Windkraft und Elektromobilität hält. Sie bekommen immer die gleichen Antworten, nämlich dass die Politik mit Rasanz in der völlig falschen Richtung unterwegs ist. Ein Beispiel für die Versorgungssicherheit mit Strom: Im Frühjahr hatten wir eine Periode mit sehr starkem Wind. Daraufhin haben die Stromnetze angefangen zu „wackeln“ wegen dem Überschuss aus der Windenergie. Dafür gibt es bisher und auch zukünftig keine Regelungstechnik. Wir hatten drei kurze Stromausfälle an einem Tag, daher für 10 000 Euro zerstörte Teile und weitere 10 000 Euro Kosten, um die Maschinen wieder zum nächsten Gutteil zu bringen.
Sie unterhalten auch eine Fahrzeugflotte für Ihre Kundendienstmannschaft. Sind hier reine E-Autos praktikabel einsetzbar?
Diebold: Absolut nicht. Wenn ein Servicemann einen Termin hat, weil beim Kunden eine Anlage stillsteht, kann er keine Zeit mit der Suche nach einer Ladestation verbringen, in der Hoffnung, dass er dann dort auch laden kann. Hybrid-Fahrzeuge sind ja sehr beliebt aber ökologisch voll daneben. Zwei Motoren in einem Auto und dann noch Batterien, von denen man bisher nicht weiß, wie sie entsorgt werden können, halte ich für sehr fragwürdig. Serviceleute sind schon immer mit Dieselmotoren unterwegs gewesen, da diese die beste, sicherste, kostengünstigste und umweltfreundlichste Lösung darstellen. Die Politik hat aber den Diesel kaputtgeredet und jetzt stehen wir vor dem Dilemma, dass Hunderttausende qualifizierte Mitarbeiter in dieser Industrie ihren Job, ihren Wohlstand und ihre Sicherheit verlieren werden.
Die politischen Entscheidungen rund um Corona haben die Wirtschaft massiv einbrechen lassen. Haben Sie Pläne entwickelt, wie Ihr Unternehmen künftig mit derartigen Ereignissen umgehen wird?
Diebold: Corona hat der Industrie und vor allem den Dienstleistern einen gewaltigen Schlag versetzt. Es ist sehr schwierig, sich auf solche Situation vorzubereiten oder sogar gegenzusteuern. Jetzt scheint das Tal durchschritten zu sein, aber es geht viel zu langsam wirtschaftlich wieder aufwärts und die Unternehmen bluten aus. Irgendwie scheint es mir, dass niemand in der Industrie den Mut hat, seine Geschäfte weiter zu betreiben, zu investieren und zumindest einzukaufen. Eine deutsche Eigenart, die sich schon in der Krise 2008 gezeigt hat. Ich habe damals bei Index eine Maschine bestellt und war der große Held auf der Hausmesse, weil die Großen Kunden zwar dort waren, aber nichts getan haben. Ich wusste damals nicht ob ich die Maschine auch werde bezahlen können, habe es aber trotzdem getan, um diesen Top-Maschinenlieferanten zu unterstützen. Und es war die richtige Entscheidung.
Wie verhalten Sie andere Länder an der Stelle?
Diebold: Wir sehen, dass unsere Vertreter in Asien sehr quirlig unterwegs sind und bereits wieder gute Aufträge landen. Aber jeder muss dort kämpfen, auch weil die soziale Absicherung wie bei uns fehlt (dies gilt übrigens auch für viele europäische Länder). China hat ja einen klaren Plan, sich ein Stück von unserem Wohlstand zu holen, und ja, sie schaffen es. Langfristig wird dieses Szenario für den Wohlstand der kommenden Generationen schwierig.
Was halten Sie von den Subventionsmaßnahmen der Regierung?
Diebold: Es ist vor allem ein gutes Zeichen gewesen, bis zu 1.000 Milliarden Euro bereitzustellen. Es hat die Menschen und die Unternehmen beruhigt. Ich hoffe, dass sie am Ende nicht gebraucht werden, weil sonst die Inflation galoppiert und wieder ein Stück unseres Wohlstandes zugrunde geht.
Wie schützen Sie sich gegen Infektion mit Corona?
Diebold: Ich persönlich vermeide Kontakte wo immer es möglich ist. Ich muss nicht jeden Tag in den Supermarkt oder den Baumarkt. Ich war gut vorbereitet und kaufe schon seit vielen Jahren Dinge des täglichen Gebrauchs online. Aus dieser Erfahrung heraus entwickeln wir auch gerade ein Konzept, wie wir unsere Produkte im B2B vermehrt elektronisch verkaufen können. Dahinter steht auch ein gewaltiges Einsparpotenzial bei der Beschaffung von Gütern des industriellen Verbrauchs. Dies wird aber bisher in unserem Industriezweig viel zu wenig genutzt.
Wie schützen Sie Ihre Mitarbeiter?
Diebold: Als Corona akut wurde, haben wir sofort für die Verwaltung Homeoffice eingerichtet. Es sind also immer nur 50 Prozent der Mitarbeiter anwesend und die Teams treffen sich auch seit ein paar Wochen gar nicht mehr. In der Fertigung sind wir deutlich in Kurzarbeit und können damit die Teams im getrennten Wochen-Rhytmus einsetzen.
Was halten Sie von den Lockerungsmaßnahmen?
Diebold: Es scheint schon ok zu sein, dass jetzt Schulen, Kitas, Restaurants et cetera wieder auf Normalzustand zurückkommen wollen. Aber wehe es funktioniert nicht und der nächste Lockdown kommt, dann weiß ich keinen Rat mehr.
Herr Diebold, vielen Dank für das Interview.
Download
Dieses Interview finden Sie auch in Ausgabe 4/2020 unseres Fachmagazins ›Welt der Fertigung‹ auf Seite 16. Zum besagten Heft führt ein Klick auf den nachfolgenden Button!
Mehr Informationen zu Diebold:
![]() |
Diebold Goldring Werkzeuge GmbH & Co. |
![]() |
An der Sägmühle 4 |
![]() |
72417 Jungingen |
![]() |
Telefon 07477 871-0 |
![]() |
Fax 07477 871-30 |
![]() |
E-Mail: kontakt@hsk.com |
![]() |
www.hsk.com |
War dieser Artikel für Sie hilfreich?
![]() |
![]() |
![]() |
![]() |
![]() |
Bitte bewerten Sie diese Seite durch Klick auf die Symbole.
Zugriffe heute: 1 - gesamt: 2364.