Präzisionswerkzeuge mit Anspruch
Teile auf perfekte Weise zerspanen
Viele große Konzerne aus dem Bereich Aerospace, aber auch zahlreiche Mittelständler und kleinere Unternehmen vertrauen auf die Qualität der Präzisionswerkzeuge der Paul Horn GmbH. Deren breites Werkzeugportfolio sorgt dafür, dass zu vielen Bearbeitungsaufgaben das passende Werkzeug bereitsteht. Grund genug für die die Herrmann CNC-Drehtechnik GmbH aus Hohenlinden sowie die Apex Tool Group GmbH, sich aus diesem leistungsstarken Portfolio zu bedienen.
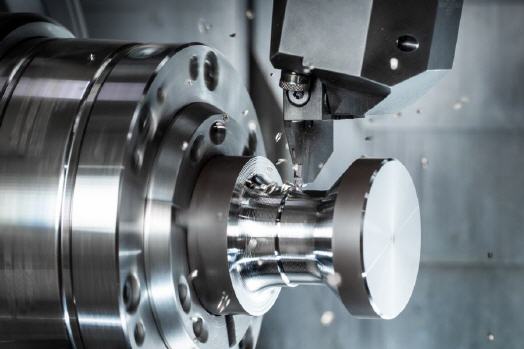
»Landeklappen sind zum Landen da« – ein häufiger Irrglaube, wenn es um die Beschreibung der ausfahrbaren Flügelverlängerungen geht. Die korrekte Bezeichnung der Verlängerung ist der Begriff ›Hochauftriebshilfe‹. Dieses System benötigt ein Flugzeug zum Start und zur Landung, um den Auftrieb zu vergrößern. Die Flügelflächen bieten bei den geringen Start- und Landegeschwindigkeiten sonst zu wenig Auftrieb. Des Weiteren erhöht sich der Luftwiderstand beim Landen, da die Geschwindigkeit sonst zu hoch wäre und die Bremsen der Räder überlasten könnten.
Zur genauen Steuerung des Auftriebs kann der Pilot die Flügelvorderkante (Slats) und die Flügelenden (Flaps) aus- und einfahren. Die Bewegung der Slats und Flaps geschieht über eine Mechanik im Flügelinneren. Hier kommt ein Stehlager der Herrmann CNC-Drehtechnik GmbH zum Einsatz. Das Lager überträgt das Drehmoment des Gestänges und gleicht das axiale Spiel über eine Verzahnung aus. Darüber hinaus dient das Stehlager als winkelbewegliche Kupplung zwischen den Wellen.
»Als Zulieferer in der Luftfahrtindustrie arbeiten wir täglich mit besonderen Werkstoffen, die nicht immer leicht zu zerspanen sind«, erklärt Produktionsleiter Schubel. Für die Stechbearbeitungen der Nabe und der Welle des Stehlagers setzt Schubel mit seinem Team auf Werkzeuge von Horn. Die Lagernabe fertigen die Zerspaner aus 1.4548 (X5CrNiCuNb17-4-4), einem Stahl mit hoher Festigkeit und Zähigkeit, der durch seine hohe Korrosionsbeständigkeit und den sehr guten mechanischen Eigenschaften häufig in der Luft- und Raumfahrt zum Einsatz kommt. Den großen und tiefen Einstich fertigen die Werker über das trochoidale Stechverfahren in das Werkstück. Zum Einsatz beim Schruppen kommt hierbei eine Vollradius-Stechplatte aus dem Horn-System ›S229‹ mit einem Radius von zwei Millimeter. Als Substrat kommt die Sorte ›AS66‹ zum Einsatz.
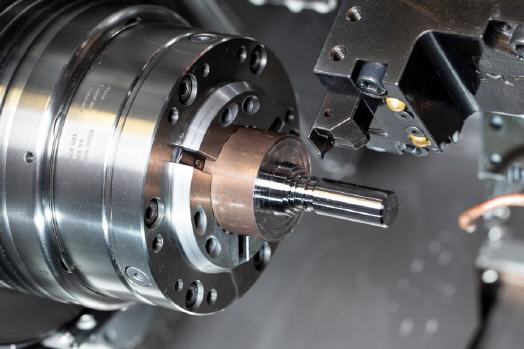
Für hohes Spanvolumen
Das trochoidale Drehen eignet sich sehr gut für das Drehen von tiefen und breiten Einstichen, bei denen ein hohes Spanvolumen generiert werden muss. »Wir wenden das Verfahren seit rund zwei Jahren aktiv an. Als CAM-System nutzen wir Esprit. Die Software war eine der ersten, die die Möglichkeit zum trochoidalen Stechen geboten hat«, sagt Schubel. Der Stechprozess gestaltet sich wie folgt: Der 30 mm breite und 15 mm tiefe Einstich wird mit der Vollradius-Wendeschneidplatte mit einer Schnittgeschwindigkeit von vc = 140 m/min bei einer Schnitttiefe von ap = 1 mm trochoidal geschruppt. Der Vorschub ist mit fn = 0,25 mm-1 programmiert. Das Schlichtaufmaß liegt bei 0,2 mm.
Beim Schlichten kommt ebenfalls eine Schneidplatte des Systems S229 zum Einsatz. Die Schlichtbearbeitung geschieht von zwei Seiten mit einer drei Millimeter breiten Stechplatte. Der Eckenradius beträgt 0,2 mm. Die Gesamt-Fertigungszeit des Einstiches liegt bei unter zwei Minuten. »Durch das Stechverfahren haben wir bei dem schwer zu zerspanenden Werkstoff keine Probleme mit langen Spänen«, so Schubel.
Die Welle des Stehlagers besteht aus dem Werkstoff SAE 51431 (1.4044), vergütet auf 1 350 bis 1 500 N/mm2. »Der Bezug dieses Stahles in Sonderqualität gestaltet sich häufig schwierig. Wir beziehen das Material direkt beim Hersteller in Frankreich. Wir bestellen es deshalb nicht in vielen Durchmesservarianten. Die geringeren Stückzahlen der zu fertigenden Bauteile rechtfertigen auch die teilweise hohen Abtragswerte. Sonst würden wir nicht aus einem 55 mm Rundmaterial eine 26,4 mm Welle drehen«, erzählt der Produktionsleiter. Die fünf Millimeter breiten Einstiche übernimmt eine Schneidplatte des Horn-Systems 223. Die Standzeit pro Schneide liegt hier bei über 300 Werkstücken. Das Innenausdrehen der Bohrung und die 45-Grad-Fase fertig eine Schneidplatte des Typs ›Supermini 105‹. Das Schlichten des Axialeinstiches übernimmt ebenfalls ein Supermini.
»Die geforderten hohen Oberflächengüten konnten wir mit den Werkzeugen problemlos einhalten«, so Schubel. Im Mittelpunkt steht bei der Fertigung immer die Qualität der Bauteile. Für die strenge Luftfahrtzertifizierung nach DIN EN 9100 ist ein sauberer Arbeitsplatz, hochqualifiziertes Personal und eine Qualitätssicherung mit Hightech-Messmaschinen eine bedingungslose Voraussetzung. Es sind nicht nur die offiziellen Zertifizierungen, auch die Kunden von Herrmann besuchen den Betrieb für regelmäßige Audits. »Sauberkeit, präzises Arbeiten und die ständige Qualitätskontrolle sind für unsere tägliche Arbeit ein absolutes Muss«, erzählt Schubel.
So fertigt der Betrieb alle Bauteilklassen für die Luftfahrtindustrie, welche von der Klasse 3 bis Klasse 1 reichen. Ein Klasse-1-Bauteil ist das kritischste Bauteil. Bei dessen Versagen wird die Sicherheit des Fluggeräts massiv beeinträchtigt. Beim Versagen eines Bauteils der Klasse 2, entsteht eine schwere Beeinträchtigung des Fluggeräts, aber die Landung ist noch möglich. Der Ausfall eines Klasse 3 Bauteils wirkt sich nicht auf die Funktionsweise aus.
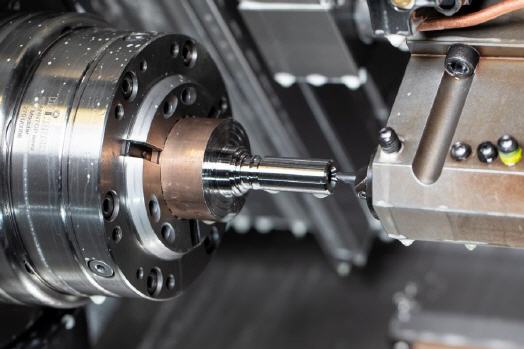
Für anspruchsvolle Einsätze
Durch das Knowhow bei der Zerspanung von sensiblen Bauteilen und schwer zerspanbaren Werkstoffen hat sich das Unternehmen bei vielen großen Luft- und Raumfahrtkonzernen einen sehr guten Ruf und den Status ›preferred supplier‹ erarbeitet.
So ist es kein Wunder, dass auch das Unternehmen Apex Tool Group GmbH auf Präzisionswerkzeuge von Horn setzt. Die Maschinen dieses Unternehmens finden ihren Einsatz beispielsweise in großen Montagelinien der Automobilindustrie, in der Montage der Luftfahrtindustrie sowie der Energieerzeugung. Eben überall dort, wo der Anwender sich auf die Leistung und Genauigkeit der Powertools verlassen muss.
Dies gilt beispielsweise bei exakt einzuhaltenden Anzugs-Drehmomenten von bestimmten Verschraubungen. Solche Verbindungen müssen dokumentiert werden. Die Marke ›Cleco‹ der Apex Tool Group bietet deshalb Maschinen, die die angezogenen Drehmomente automatisch und vernetzt genau dokumentieren. Auch die Langlebigkeit der Maschinen spielt in der Serienfertigung eine große Rolle. Für einige der Cleco-Maschinen gibt der Hersteller eine Garantie für mindestens zwei Millionen Schraubzyklen, bei einer sehr kleinen Toleranz der zulässigen Drehmomentabweichung.
Der Planetenträger ist eines der zentralen Bauteile einer Einbau-Schraubspindel. Diese Spindel kommt unter anderen in der Automobilmontage zum Einsatz. Fünf Schraubspindeln, als Paket montiert, verschrauben beispielsweise gleichzeitig alle fünf Radschrauben bei der Rädermontage. Auch in vollautomatisierten Fertigungs- und Montageanlage sind Cleco-Schraubspindeln verbaut. Das Planetengetriebe dient zur Kraftübertragung zwischen Motor und Spindel und ist sehr präzise gefertigt. Schon kleine Rundlauffehler können die geforderte Anzahl an Schraubzyklen über die Lebensdauer verändern.
Zur Fertigung des Planetenträgers setzten die Verantwortlichen auf das Fräs- Drehzentrum ›726 MT‹ von Stama. Zum Stechen eines 50 mm breiten Einstichs wird auf das Horn-Werkzeugsystem zum Stechen mit der Y-Achse gesetzt. Der Einstich wird vorher mit dem Horn-System ›S229‹ geschruppt.
Clevere Lösung
Speziell beim Ab- und Einstechen in Werkstücken mit größeren Durchmessern entstehen große Hebelkräfte. Die Platzverhältnisse in der Maschine erlauben oft nicht den Einsatz von Werkzeugen mit größerem Querschnitt. Daher hat Horn eine besondere Anordnung der Schneide im Werkzeugträger vorgenommen. Dies bewirkt, dass die Schnittkräfte in den Hauptquerschnitt des Stechhalters eingeleitet werden. Auf diese Weise ergibt sich bei gleichen Querschnitten der Stechhalter eine höhere Steifigkeit des Gesamtsystems. Dies erlaubt höhere Vorschübe bei gleicher Stechbreite.
Der Kraftfluss in Längsrichtung des Werkzeugs erlaubt schmälere Halter bei gleicher Steifigkeit des Systems. Bei modernen Generationen von Dreh- und Fräszentren führt das Abstechen mit den innovativen Stechwerkzeugen zu einer Einleitung der Schnittkraft in Spindelrichtung und damit zu einer höheren Steifigkeit des Gesamtsystems. Darüber hinaus bietet das System eine innere Kühlmittelzufuhr durch den Spannfinger und die Unterstützung. Als Schneideinsatz setzt Horn bei dem Stechsystem auf die Schneidplatte des Typs ›S100‹.
Für mehr Wirtschaftlichkeit
Der Wechsel der Stechstrategie brachte einen Zeitvorteil von über einer Minute. Das resultiert aus der Möglichkeit, mit dem Stechsystem den doppelten Vorschub zu fahren. Darüber hinaus stieg die Standzeit des Werkzeugs sowie die Spankontrolle, da der Span direkt nach unten abgeleitet wird. Gestochen wird mit einer Schnittgeschwindigkeit von vc = 130 m/min bei einer Vorschubgeschwindigkeit von 0,3 mm/U. Das Stechen ist eine reine Schruppoperation. Der Abstich geschieht am Durchmesser des Einstiches.
Geschlichtet wird der Einstich auf der Gegenspindel mit einer ISO DCMT-Schneidplatte. Auf der Gegenspindel wird wegen des Materialverzugs nicht geschruppt. Des Weitern wird mit einer glatten Spannzange gearbeitet.
Zur Aufnahme von den drei Zahnrädern des Planetengetriebes müssen in das Bauteil drei Nuten gefräst werden. Für diesen Zweck wird auf das Horn-Frässystem ›M310‹ mit einem Schneidkreis von 63 mm gesetzt. Durch den Wechsel auf den Scheibenfräser von Horn konnte die Vorschubgeschwindigkeit von früher 280 mm/min auf nun 400 mm/min erhöht werden. Des Weiteren erhöhte sich die Standzeit und das Fräsgeräusch klingt nun viel runder, so die Aussage der Maschinenbediener. Das Werkzeug fährt zum Fräsen der Nut auf einer Kreisbahn. Die 20 mm breite Nut fräst der Scheibenfräser in vier Schnitten. Bestückt ist das Horn-Frässystem mit dreischneidigen Wendeschneidplatten des Typs ›310‹.
»Wir sind mit dem Frässystem sehr zufrieden. Es ist preislich nicht günstig, aber Qualität hat seinen Preis und wenn wir die gesamten Prozesskosten betrachten, rechnet sich der höhere Preis aufgrund der hohen Standzeiten und der kürzeren Bearbeitungszeiten sehr schnell«, erzählen die Verantwortlichen der Apex Tool Group.
Download:
Diesen Artikel finden Sie auch in Ausgabe 4/2021 auf Seite 14. Zum besagten Heft führt ein Klick auf den nachfolgenden Button!
Mehr Informationen zur Paul Horn GmbH
![]() |
Hartmetall-Werkzeugfabrik |
![]() |
Paul Horn GmbH |
![]() |
Horn-Straße 1 |
![]() |
72072 Tübingen |
![]() |
Telefon: 07071 7004-0 |
![]() |
Fax: 07071 7289-3 |
![]() |
E-Mail: info@de.horn-group.com |
![]() |
www.horn-group.com/de |
War dieser Artikel für Sie hilfreich?
![]() |
![]() |
![]() |
![]() |
![]() |
Bitte bewerten Sie diese Seite durch Klick auf die Symbole.
Zugriffe heute: 5 - gesamt: 4117.