Additive Lösung für automobile Leistungselektronik
Serienfähige Aluminiumgehäuse für SiC-Inverter
Die Technologie des Direct Metal Laser Sintering (DMLS) ermöglicht die ebenso kostengünstige wie kurzfristige Bereitstellung serienreifer Bauteile aus Stahl und Metall. Das Unternehmen FKM realisiert mit diesem additiven Fertigungsverfahren beispielsweise Aluminiumgehäuse mit einer überaus filigranen 3D-Kühlkörperstruktur zur Herstellung hocheffizienter SiC-Wechselrichter für den Einsatz in E-Mobility-Anwendungen.
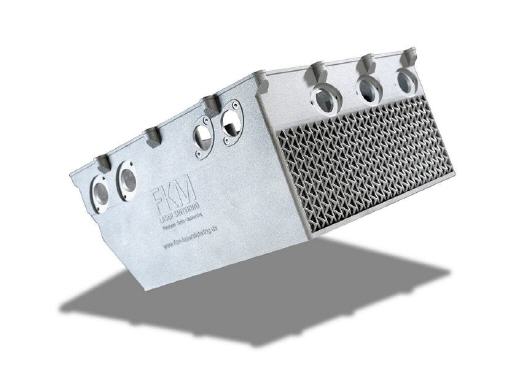
Vor den Toren der hessischen Kleinstadt Biedenkopf betreibt FKM eine der modernsten Lasersinter-Fabriken Europas. Neben 30 Sinteranlagen für das 3D-Printing von Serienteilen und Prototypen aus verschiedenen technischen Kunststoffen gehören auch über ein Dutzend Anlagen für die additive Fertigung von Bauteilen aus Stahl und Metall zum Maschinenpark des Unternehmens. Im Fokus des Direkten Metall Lasersinterns (DMLS) stehen dabei häufig vier Anlagen vom Typ M 290 des deutschen Herstellers EOS.
„Mit einem Bauraum von 250 x 250 x 325 mm (L x B x H) und ihrem leistungsstarken 400-Watt-Faserlaser versetzen uns diese Systeme in die Lage, flexibel und wirtschaftlich serienreife Bauteile aus Metall zu fertigen“, sagt FKM-Geschäftsführer Jürgen Blöcher.
Da diese Maschinen eine ganze Reihe validierter Legierungen verarbeiten können, entstehen in ihren Bauräumen sowohl Prototypen als auch Vor- und Kleinserien aus ganz unterschiedlichen Stahl- und Metall-Werkstoffen. Fertigstellen und ausliefern konnte FKM in diesen Tagen beispielsweise das erste Gehäuse für einen neuen, luftgekühlten SiC-Wechselrichter (40 kW), der vom Fraunhofer-Institut für Integrierte Systeme und Bauelemente-Technologie (IISB) für den Einsatz in der automobilen E-Mobility entwickelt wurde.
Dabei handelt es sich um eine 235 x 215 x 110 mm große Box mit integrierter Kühlgitterfläche und anschraubbarem Deckel aus der Aluminiumlegierung AlSi10Mg. Wie üblich im DMLS erfolgte die Fertigung direkt aus den CAD-Daten des Auftraggebers – also ohne den Zeit- und Kostenaufwand für Modell- und Werkzeugbau sowie Umformtechnik. Als abschließender Fertigungsschritt vor der Auslieferung fiel noch die mechanische Detail-Bearbeitung an, die zum Leistungsumfang von FKM gehört.
Komplexes 3D-Kühlgitter problemlos realisierbar
Das von FKM gefertigte Aluminiumgehäuse erfüllt alle wichtigen Kriterien für den Einbau der Leistungselektronik des neuen SiC-Inverters, dessen hohe Effizienz auf dem Einsatz sogenannter MOSFETs (Metall-Oxid-Halbleiter-Feldeffekttransistoren) beruht. Das Gehäuse bietet mit Wandstärken von 3,0 mm eine ausreichend hohe Stabilität und Steifigkeit zum Schutz des elektronischen Innenlebens, bringt allerdings Dank des leichten Werkstoffs nur 2,75 kg auf die Waage.
Insbesondere aber ließ sich durch den Einsatz des Lasersinterns eine höchst innovative Lösung für die Wärmeableitung realisieren, die für die Funktionsfähigkeit des schnell schaltenden SiC-Inverters entscheidende Bedeutung hat. Dabei handelt es sich um zwei in die Seitenwände des Gehäuses integrierte Kühlkörper, deren geometrisch überaus komplexe Mehrebenen-Gitterstruktur strömungstechnisch bis ins Detail ausgetüftelt ist und eine kompakte Bauweise des Gehäuses ermöglicht.
„Ein derart filigranes 3D-Design lässt sich mit konventionellen Methoden der Metallbearbeitung nicht wirtschaftlich realisieren; das Lasersintern ist hierfür das ideale Fertigungsverfahren und kann mit einer Schichtstärke von nur 0,03 mm zudem eine hohe Genauigkeit umsetzen“, erläutert Jürgen Blöcher.
Darüber hinaus positionierten die FKM-Techniker das Inverter-Gehäuse so im Bauraum der Lasersinteranlage, dass die Kühlgitter während der Fertigung zugleich als Stützkonstruktion dienten. Auf diese Weise war kein zusätzlicher Support erforderlich, der nachher hätte entfernt werden müssen.
Ab Losgröße 1 aufwärts
Das lasergesinterte Aluminiumgehäuse steht exemplarisch für zahlreiche ähnlich gelagerte Kundenprojekte im Fertigungsalltag von FKM. Wie in vielen anderen Fällen galt es auch hier zunächst, im Rahmen der Entwicklung des neuen SiC-Inverters eine idealtypische Lösung zu schaffen, die nach dem Productlaunch als Anknüpfungspunkt für den Einstieg in die Serienproduktion dient.
„Für eine kurzfristige Realisierung bedarfs- oder nachfragegesteuerter Vor- oder Kleinserien stehen uns dann auch unsere größeren DMLS-Anlagen der X-Line von Concept Laser zur Verfügung, in denen sich gleich mehrere Gehäuse-/Deckel-Sätze sintern lassen“, berichtet Firmenchef Jürgen Blöcher.
Je nach Projekt und Materialanforderung kann FKM zudem auf eine beachtliche Auswahl an metallischen Sinter-Werkstoffen zugreifen. Neben dem Werkzeugstahl 1.2709, den Edelstählen 1.4404 und 1.4542 sowie der Chrom-Nickel-Legierung Inconel 718 verfügt das Unternehmen über die Möglichkeit, das bereits erwähnte Aluminium sowie Cobalt-Chrom und Titan im DMLS-Verfahren zu verarbeiten. „Neu ins unsere Werkstoff-Palette mit aufgenommen haben wir vor wenigen Tagen außerdem eine lasersinterfähige Kupfer-Legierung“, ergänzt Jürgen Blöcher.
Allein im vergangenen Jahr hat FKM in seiner Lasersinter-Fabrik in Biedenkopf über 9000 Einzelaufträge mit wechselnden Losgrößen gefertigt. Nach wie vor lag und liegt der Schwerpunkt dabei zwar auf der Realisierung von zum Teil hochkomplexen Formteilen aus technischen Kunststoffen, doch Jürgen Blöcher betont: „Der Anteil der Sinterteile aus Metall nimmt kontinuierlich zu, wobei die entscheidenden Impulse derzeit aus Medizintechnik, Antriebstechnik und Fluidtechnik kommen.“
Mehr Informationen zur FKM Sintertechnik GmbH:
![]() |
FKM Sintertechnik GmbH |
![]() |
Zum Musbach 6 |
![]() |
35216 Biedenkopf |
![]() |
Tel.: +49 (0) 64 61 / 75 85 2 - 0 |
![]() |
Fax:+49 (0) 64 61 / 75 85 2 - 90 |
![]() |
E-Mail: info@fkm.email |
![]() |
www.fkm-lasersintering.de |
War dieser Artikel für Sie hilfreich?
![]() |
![]() |
![]() |
![]() |
![]() |
Bitte bewerten Sie diese Seite durch Klick auf die Symbole.
Zugriffe heute: 5 - gesamt: 4569.