Passion for Perfection
Interview mit Hermann Diebold
Das Unternehmen Diebold hat schon 2006 in die vollklimatisierte Fertigung investiert. Eine visionäre Investition, die sich heute bezahlt macht.
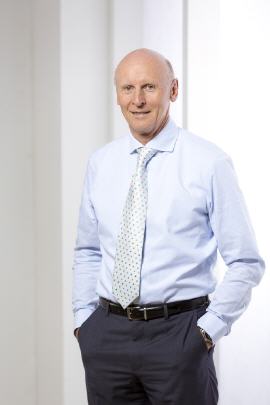
Herr Diebold, was verbirgt sich hinter Ihrem Slogan Passion for Perfection?
Hermann Diebold: Passion for Perfection heißt, wir machen unsere Produkte so gut wie möglich und nicht so gut wie nötig.
Können Sie das präzisieren?
Diebold: Ja das kann man einfach erklären. Es gibt im Bereich Werkzeughalter DIN/ISO-Normen, die entsprechende Genauigkeiten insbesondere für HSK-Kegel vorschreiben. Werden diese Normen in den Genauigkeiten eingehalten funktionieren die Schnittstellen zwischen Spindel und HSK-Werkzeughalter. Bei höheren Ansprüchen beim HSC-Fräsen (High Speed Cutting) oder HPC-Fräsen (High Performance Cutting) müssen die Toleranzen deutlich kleiner sein als in der Norm vorgesehen, um gute Zerspanungsergebnisse zu erreichen. Konkret: nach unserer Erfahrung erfüllen 30 Prozent der Werkzeughalter, die auf dem Markt sind, nicht die Genauigkeiten, die die DIN/ISO verlangt.
Können Sie das an einem Beispiel erklären?
Diebold: HSK Kegel sind überbestimmt und müssen durch die Spannkraft des Einzugssystems verformt werden. Wenn der Werkzeughalter an der oberen Toleranzgrenze der Norm gefertigt ist und die Spindel ebenfalls, dann gehen beim Einziehen des Werkzeuges in die Spindel 35 Prozent der Spannkraft gegen die Planfläche verloren. Dann kann man sich gut vorstellen, dass der Rundlauf des Werkzeuges enorm leidet. Also fertigen wir die Toleranzen entsprechend kleiner, um die Toleranz möglichst gegen Null zu erreichen. Wenn das gewährleistet ist, hat die Werkzeugaufnahme den optimalen Sitz in der Spindel und jeder Maschinenbediener wird mit seinem Zerspanungsergebnis hoch zufrieden sein.
Nennen Sie uns ein anschauliches Beispiel!
Diebold: Ja gerne. Ich nehme gerne das Beispiel der österreichischen 1Euro-Münze, die das Gesicht Mozarts auf der Rückseite hat. Für die Münzherstellung braucht man einen Prägestempel, der mit kleinsten Fräsern bei hoher Geschwindigkeit gefertigt wird. Wenn Mozart schielt, dann haben die Toleranzen im Fräsprozess nicht gestimmt. Das sind wenige µ, die aber trotzdem mit bloßem Auge zu erkennen sind.
Gibt es noch höhere Anforderungen Ihrer Kunden?
Diebold: Ja, wir sehen drei wichtige Blöcke an technischen Herausforderungen:
- unsere Kunden brauchen Spannfutter mit einem Rundlauf vom HSK-Kegel zur Werkzeugaufnahmeseite < 1µ
- hochpräzise Werkzeughalter müssen mit besonders aufwändiger Technik dynamisch gewuchtet werden
- für Hochgeschwindigkeitsfräsen sind Werkzeugaufnahmen mit großen Dämpfungseigenschaften erforderlich
Können Sie solche Produkte schon anbieten?
Diebold: Ja, wir haben die praktischen Versuchsreihen abgeschlossen und sind in der Lage, solche Werkzeughalter für diese anspruchsvollen Anwendungen anzubieten.
Was braucht es dazu?
Diebold: Für die Herstellung solch hochgenauer Aufnahmen sind eine vollklimatisierte Fertigung mit konstant 21 Grad Celsius, entsprechend genaue Maschinen und vor allem gut ausgebildete und erfahrene Facharbeiter nötig, die in der Lage sind, solche Genauigkeiten zu fertigen. Und nicht zuletzt wird eine entsprechende messtechnische Einrichtung benötigt, um solche kleinen Toleranzen messen und dokumentieren zu können.
Was ist das Besondere an Ihrer Messtechnik?
Diebold: Wir stellen Mehrstellen- Messgeräte zum Messen der HSK-Kegel her. Dazu gehören Einstellmeister der höchsten Genauigkeitsstufe. Diese messen und zertifizieren wir in einem Messraum der Güteklasse 2 auf dem Niveau eines Kalibrierinstitutes.
Was fragen Ihre Kunden am meisten nach?
Diebold: Das sind insbesondere Werkzeugaufnahmen fürs Hochgeschwindigkeitsfräsen, also HSK 40,32,25 und 20. Unser meistverkaufter Artikel sind Schrumpffutter HSK-E 40 mit einem Durchmesser von 3 mm. Wir sind in diesem Sektor Weltmarktführer.
Was zeichnet Sie als Weltmarktführer aus?
Diebold: Ein Schrumpffutter mit einem Durchmesser von 3 mm in höchster Genauigkeit zu fertigen ist nicht trivial. Dazu wird eine klimatisierte Einrichtung benötigt, über die einige Mitbewerber nicht verfügen. Hinzu kommt eine konsequente Umsetzung der Fertigungsmethode bis hin zum Vermessen des Teils. Unsere Kunden haben festgestellt, dass sie die genauesten Schrumpffutter nur bei uns bekommen.
Wo sehen Sie weitere Entwicklungsschritte in Sachen Technologievorsprung?
Diebold: Von Seiten der Technik sind immer Qualitäts- bzw. Genauigkeitsverbesserungen möglich. Unsere Maschinen werden immer genauer und mit der richtigen Messtechnik kann man deutliche Schritte nach vorne machen. Wir fertigen Teile genauer, als man sie technisch messen kann. Wenn man den Rundlauf misst, muss entweder das Teil oder die Messeinrichtung bewegt werden. Auch Messmaschinen können auf Grund ihrer Messstrategie und dem Verrechnen von Messwerten dies nicht leisten. Deshalb verwenden wir eigenentwickelte Messstraegien für Rundläufe < 1µ.
Können Sie ein weiteres Beispiel nennen?
Diebold: Selbstverständlich! Wir stellen sehr viele Ausricht-und Rundlaufprüfdorne her. Üblicherweise glaubt man, dass ein Messdorn auf einer vollautomatischen Messmaschine gemessen werden kann. Die Messverfahren und die Software sind aber nicht in der Lage, dies in der ausreichenden Genauigkeit zu dokumentieren. Wir benutzen drei verschiedene Messmethoden, darunter auch die Messmaschine, um Messdorne zu zertifizieren. Mit der Produktlinie ›Messdorne‹ sind wir sehr erfolgreich und wachsen jährlich um 30 Prozent. Offensichtlich haben die Anwender herausgefunden, dass es bei uns außergewöhnlich präzise Messdorne zu marktüblichen Preisen gibt.
Wie kam es zu dieser Leidenschaft für Perfektion?
Diebold: Wir haben schon 2006 visionär in die vollklimatisierte Fertigung investiert und konnten so den Genauigkeitsbereich sukzessive weiterentwickeln. Erst in den letzten fünf Jahren sehen wir, dass unsere Kundschaft diese hohen Genauigkeiten auch benötigt und anwendet. Sie sehen den Nutzen, weil sie noch genauer fertigen können. Wir waren also der Zeit um einige Jahre voraus. Die ersten Jahre waren wir enttäuscht, dass diese Investition keinen zählbaren Nutzen gebracht hat, aber inzwischen ist es ein must-have, um die Leidenschaft für Perfektion umzusetzen.
Herr Diebold herzlichen Dank für das Interview.
Mehr Informationen zu Diebold:
![]() |
Diebold Goldring Werkzeuge GmbH & Co. |
![]() |
An der Sägmühle 4 |
![]() |
72417 Jungingen |
![]() |
Telefon 07477 871-0 |
![]() |
Fax 07477 871-30 |
![]() |
E-Mail: kontakt@hsk.com |
![]() |
www.hsk.com |
War dieser Artikel für Sie hilfreich?
![]() |
![]() |
![]() |
![]() |
![]() |
Bitte bewerten Sie diese Seite durch Klick auf die Symbole.
Zugriffe heute: 4 - gesamt: 4875.