Partnerschaft mit Doppelmayr ausgebaut
Neue Fertigungsstraße beim Seilbahnbau-Marktführer
Mit seinen Seilbahnlösungen erklimmt die Doppelmayr/Garaventa Gruppe höchste und entlegenste Winkel der Erde, transportiert Menschen zum Skifahren, Urlauben oder in die tägliche Arbeit. Seit 17 Jahren pflegen der Marktführer im Seilbahnbau und MicroStep eine enge Partnerschaft. Auf der Jagd nach stetigen Verbesserungen wurde die zuverlässige Fertigungsstraße komplett erneuert. Dadurch steigerte Doppelmayr seine Flexibilität im Zuschnitt, dessen Präzision und auch die Produktionsgeschwindigkeit.
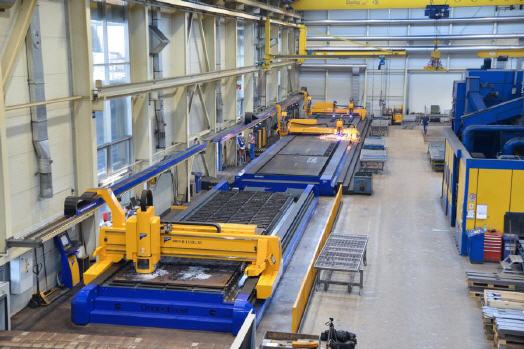
Türkis schimmerndes Meer, glitzernde Sandstrände, von Palmen bedeckte Inseln – der Anblick, den Vietnam-Urlauber bei einer Fahrt mit der längsten Seilbahn der Welt seit wenigen Monaten genießen dürfen, ist einzigartig. 7.899,9 Meter verbinden die beiden Ferieninseln Phú Quốc und Hòn Thơm im Süden des Landes im Golf von Thailand, an höchster Stelle führt die Seilbahn den Besucher auf 164 Meter Höhe. Szenenwechsel: La Paz, Bolivien, höchst gelegener Regierungssitz der Welt am Fuß des schneebedeckten 6.438 Meter hohen Bergs Illimani. Statt U-Bahnen verbinden bald zehn Seilbahnlinien die einzelnen Stadtteile, die sich bis nach El Alto auf atemberaubende 4.100 Meter hinaufziehen. Zwei einzigartige Winkel der Welt, zwei Zeugnisse der Leistungsfähigkeit der Doppelmayr/Garaventa Gruppe.
Denn die Historie der Firma Doppelmayr ist geprägt von Innovationen, Rekorden und Superlativen. Adjektive wie „längste“, „größte“, „höchste“ und mehr zieren die Überschriften reich bebilderter Artikel in etlichen Zeitungen und Magazinen. Mit seinen Seilbahnsystemen erschließt der Technologieführer abgelegene Winkel des Erdballs in luftigen Höhen und verbindet mit innovativen Transportlösungen Menschen mit Städten und Natur. In 95 Staaten des Erdballs sind auf sechs Kontinenten etliche tausend Seilbahnanlagen täglich im Einsatz, beinahe 15.000 wurden seit der Gründung der Gruppe und der Fokussierung auf die Seilbahnbranche im 20. und 21. Jahrhundert ausgeliefert und in Betrieb genommen.
Nicht grundlos trägt das Unternehmen seit mehr als einem halben Jahrhundert weltweit den Titel Markt- und Technologieführer. „Vorausschauen, Trends erkennen, Innovationen schaffen. Das sind die Stärken, auf die sich Doppelmayr-Kunden verlassen können. Unsere Kunden sind unsere Partner, mit vielen arbeiten wir seit Jahrzehnten gut zusammen. So konnten wir immer wieder Meilensteine setzen“, erklärt Walter Eberle die Stärken der Gruppe. Er ist als stellvertretender Produktionsleiter in der Fertigungsplanung bei Doppelmayr am Stammsitz im österreichischen Wolfurt am Bodensee tätig.
Spannende Projekte nur mit modernen Technologien umsetzbar
Auf Eberles Schreibtisch liegen permanent neue und spannende Projekte, der Markt verlangt nach immer kurzfristigeren Lieferungen bei gleichzeitig steigender Individualität der Lösungen. „Als Markt- und Technologieführer ist es natürlich immer unser Ziel den höchsten Stand der Technik zu halten. Dafür ist es notwendig in der Produktion auf neue Technologie zu setzen“, so Eberle.
Das gelang der Doppelmayr/Garaventa Gruppe in der jüngsten Vergangenheit einmal mehr. In den vergangenen beiden Jahren wurde der gesamte Bereich Zuschnitt grundlegend modernisiert. Dabei vertraut die weltweit tätige Gruppe auf Lösungen von MicroStep – wie bereits seit mehr als 15 Jahren. Um die Jahrtausendwende war Doppelmayr auf der Suche nach einem geeigneten Lohnschneider, wurde aber bei bis zu 5.000 geforderten Brennteilen täglich nicht fündig. „So mussten wir notgedrungen einen Lieferanten für Schneidanlagen suchen und sind am Ende glücklicherweise bei der Firma MicroStep gelandet“, blickt Eberle zurück.
Die Entscheidung damals war einfach zu fällen: Doppelmayr wollte einen einzigen Ansprechpartner für Software, Steuerung, Bohranlage und Schneidanlagen, MicroStep bot als einziges Unternehmen diese Komplettlösung an. So leistete die 60 Meter lange Fertigungsstraße beinahe zwei Jahrzehnte gute Arbeit – bis es nun an der Zeit war, diese zu modernisieren. Maßgabe war dabei die Präzision beim Fasenschneiden so zu erhöhen, dass beim anschließenden automatisierten Roboterschweißen keine Probleme auftraten. Zudem sollten die Neuanschaffungen mehr Flexibilität, Produktivität und Effizienz sichern.
„Unsere Anwendungen müssen sehr genau sein, weil wir ungefähr zwei Drittel der Bauteile anschließend mit dem Roboter schweißen. Deswegen können wir hier nur eine Fasentoleranz von ± 0,5 mm verschmerzen. Das ist für diesen thermischen Prozess eine sehr, sehr hohe Anforderung“, betont Walter Eberle.
Führende Technologie, gute Erfahrungen und Servicenähe sprechen für MicroStep
Vor diesem Hintergrund informierte sich der Entscheidungszirkel bestehend aus Eberle und weiteren Produktionsverantwortlichen wie Abteilungsleiter und Maschinenbediener ausgiebig am Markt, besuchte Messen, nahm Technologien bei Vorführungen unter die Lupe. Am Ende fiel die Entscheidung erneut auf den Weltmarktführer im automatisierten Plasmaschneiden. „Es waren mehrere Kriterien, die entscheidend waren. Wir haben 15 Jahre lang zusammen gute Erfahrungen gemacht, die Servicenähe zu Bad Wörishofen hat natürlich auch einen Vorteil und beim Thema Fasenschneiden in dieser Qualität hat MicroStep ein Alleinstellungsmerkmal, wenn es darum geht, die erforderlichen Toleranzen einzuhalten.“
Seite Mitte 2016 wurde die Fertigungsstraße schrittweise erneuert. Implementiert wurden: eine Bohranlage mit einem Portal und automatischem Werkzeugwechsler sowie zwei Schneidanlagen mit insgesamt vier Portalen. Drei der Schneidportale sind jeweils mit einem Plasmarotator, einem 2D-Plasmabrenner und zwei Autogenbrennern ausgestattet – ein weiteres Schneidportal mit vier Brennern zum parallelen autogenen Brennschneiden. „Von den Erfahrungen können wir Positives berichten, es hat vom ersten Tag so funktioniert, wie es angedacht war“, so Eberle.
Mit den drei identischen Schneidportalen sei man nun deutlich flexibler. Rund 13.000 Tonnen Blech verarbeitete Doppelmayr im Zuschnitt jährlich in der jüngeren Vergangenheit. Laut einer Schätzung Eberles seien im Dreischichtbetrieb nun 18.000 Tonnen möglich.
„Wir werden in Zukunft mehr schneiden. Wenn wir mehr Anlagen bauen, brauchen wir die Kapazitäten. Um die vermehrt auftretenden Produktionsspitzen abdecken zu können, haben wir nun mehr Kapazität im Zuschnitt. Das ist ja die erste Stelle in der Fertigung, da dürfen wir nicht in Rückstand kommen. So haben wir noch gut Reserve für die Zukunft“, sagt Eberle.
Die beiden Schneidanlagen wurden zudem noch mit je einer CCD-Kamera ausgerüstet. Diese ermitteln die exakte Lage bereits eingebrachter Bohrlöcher auf dem Blech, an denen sich die gewünschte Verschachtelung dann automatisch ausrichtet. Im Ergebnis kann das Material präzise in exakt der gewünschten Relation zu den bereits eingebrachten Bohrungen geschnitten werden. „Da uns all diese Technologien auf einer Fertigungsstraße zur Verfügung stehen, sparen wir uns jede Menge zeitintensiven Materialtransport ohne Wertschöpfung“, erklärt Eberle.
Die gesamte Fertigungsstraße ist mit der Inbetriebnahme der letzten Anlage in Betrieb und läuft seitdem im Mehrschichtbetrieb – auch dank einer einwöchigen Kundenschulung vom ersten Tag an. Für die Doppelmayr/Garaventa Gruppe ein lohnender Schritt. Davon ist auch Walter Eberle überzeugt – nach mehr als 15 Jahren Zusammenarbeit. „Es zeichnet das Unternehmen aus, dass man den Fortschritt sucht und sich nicht auf dem Verdienten ausruht und weiter schaut, was man verbessern kann.“
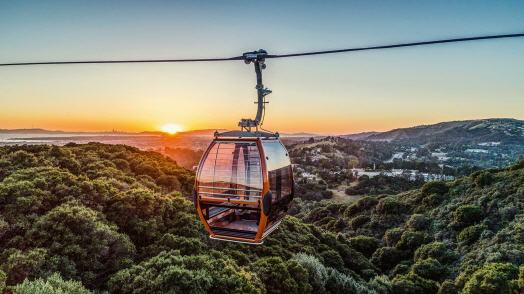
Mehr Informationen zu Microstep:
![]() |
MicroStep Europa GmbH |
![]() |
Messerschmittstraße 10 |
![]() |
86825 Bad Wörishofen |
![]() |
Tel.: +49 8247 96294-00 |
![]() |
Fax: +49 8247 96294-09 |
![]() |
E-Mail: info@microstep.com |
![]() |
www.microstep.com |
War dieser Artikel für Sie hilfreich?
![]() |
![]() |
![]() |
![]() |
![]() |
Bitte bewerten Sie diese Seite durch Klick auf die Symbole.
Zugriffe heute: 5 - gesamt: 4643.