Der Standard in Sachen ›Fasswechsel‹
Vakuum-System von Tartler
Der schnelle und sichere Austausch der Komponentenfässer gehört zu wichtigen Prozessstufen bei der Verarbeitung hochviskoser Polyurethan- und Epoxidharze sowie Silikone. Als heikel erweist sich hierbei jedoch die Möglichkeit und das Risiko, dass Luft während des Fasswechsels in die Anlage oder den Prozess eingebracht werden kann. Beim anschließenden Abpumpen und Verarbeiten des Materials verursacht diese „Schadluft“ dann technische Störungen, die mitunter sogar die Sicherheit des Maschinenbedieners gefährden. Gängige Folgeplatten-Vorrichtungen können daran wenig ändern. Das neue vollautomatische Vakuum-Entlüftungssystem mit Vakuumspannfass von Tartler räumt alle Probleme aus dem Weg.
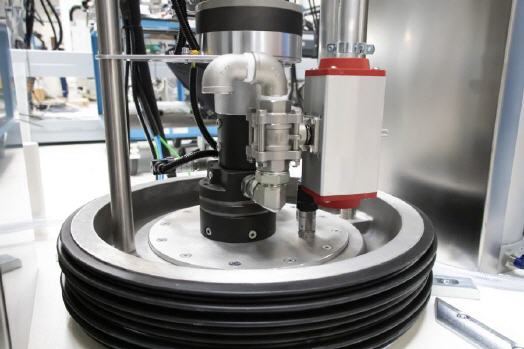
Schlecht, suboptimal oder perfekt? Wer hochviskose Silikone, Polyurethan- oder Epoxidharze in hochautomatisierten Dosier- und Mischanlagen verarbeitet, hat beim routinemäßig anstehenden Austausch der Spannring-Deckelfässer mit den A- und B-Komponenten derzeit prinzipiell drei Möglichkeiten: Nach Altväter Sitte (wenig empfehlenswert), nach derzeit etabliertem Verfahren (schon besser) oder mit dem neuen Vakuumfasswechsel-System TAVA 200 D von TARTLER (innovativ).
Erste Option: Technisch überholt
Die Traditionalisten unter den Kunststoffverarbeitern, die nicht von der althergebrachten Vorgehensweise des Fasswechsels ablassen wollen und die Fassentlüftung vor oder während des Umpumpens immer noch manuell per Kugelhahn oder andere Öffnungen vornehmen, sollten wissen: Das ist nicht mehr zeitgemäß, bietet keinerlei Prozesssicherheit und kann – da das Risiko gefährlicher Spritzer besteht – böse ins Auge gehen. Über Jahrzehnte gehörte diese Methode freilich zum Alltag in der Dosier- und Mischtechnik.
Via Kugelhahn einige Becher voll Material abziehen, bis man keine Luft mehr unter der Folgeplatte vermutet, und Start. Befand sich doch noch Luft unter der Folgeplatte, „verschluckten“ sich die Förder- und Dosierpumpen daran und der Prozess musste eventuell unterbrochen werden. Auch beim Herausfahren der Folgeplatte bestand die Möglichkeit, dass es spritzte, weil sich die benötige Druckluft im Fass in diesem Moment „entladen“ konnte. Hoher Reinigungsaufwand, dauernder Materialverlust und Restmengen im Fass und eine mögliche Kontamination des Mitarbeiters waren die Folgen – und der Sicherheitsbeauftragte hat die Hände über dem Kopf zusammengeschlagen. Wie gesagt, das ist heute technisch überholt.
Zweite Option: Der aktuelle Standard
Deutlich fortschrittlicher und erheblich sicherer ist das derzeit weit verbreitete Verfahren, bei dem die Entlüftung unter Vakuumbeaufschlagung erfolgt. Hierbei wird eventuell vorhandene Luft zwischen der Folgeplatte und der Oberfläche des Materials im Fass abgesaugt – solange, bis die Folgeplatte dicht auf dem Material sitzt. Diese Vorgehensweise beim Fasswechsel ist relativ bedienerfreundlich, verhindert gefährliche Spritzer und minimiert den Materialverlust. Allerdings erfasst die Methode nur die „Schadluft“ über dem Material und es kann kein hohes Vakuum erzeugt werden. Unter den Gesichtspunkten von Prozesssicherheit und Materialeffizienz ist diese Vorgehensweise also ebenfalls suboptimal. Sie eignet sich außerdem nicht für alle Materialien. Sie ist jedoch das derzeit etablierte Verfahren.
Dritte Option: Zukunftsweisend
Die neue Systemlösung TAVA 200 D von TARTLER schafft alle prozess-und sicherheitstechnischen Probleme beim routinemäßigen Wechsel der Materialgebinde mit hochviskosen Polyurethan- oder Epoxidharzen aus der Welt. Es handelt sich hierbei um ein vollautomatisiertes Vakuumsystem mit Vakuumspannfass zum Aufnehmen, Abpumpen und Entlüften der industrieüblichen Deckelfässer. Mit der TAVA 200 D ist garantiert, dass während des Fasswechsels kein Lufteintrag in die Misch- und Dosieranlage erfolgt.
Der Grund dafür: Zwischen der Materialoberfläche und der Folgeplatte wird ein Vakuum von -0,97 bar erzeugt. Die im Fass vorhandene Luft wird via Vakuumanschluss vollständig und kontinuierlich durch eine zwar luft- aber nicht mediendurchlässige Fassfolgeplatte abgesaugt. Es wird auch jene Luft erfasst, die eventuell in die Förder- und Dosierpumpe eingedrungen ist (weil eventuell beim Anheben der vorherigen Fassfolgeplatte pastöses Material herausgetropft ist). Ein überdruckbedingtes Spritzen ist grundsätzlich ausgeschlossen, da bei der TAVA 200 D die Folgeplatte unter Druck herausgefahren und kurz vor ihrem Austritt aus dem Fass mit einem geringen Vakuum beaufschlagt wird.
Das TAVA 200 D von TARTLER erzeugt und regelt das Vakuum über eine prozessorientiert ausgelegte Steuerung. Die Vakuumbeaufschlagung wird erst abgeschaltet, wenn sich absolut keine Luft mehr im System befindet. Alles ist auf maximale Prozessoptimierung und Sicherheit ausgelegt. Das System ist bedienerfreundlich, arbeitet vollautomatisch bietet dem Anwender volle Kontrolle bei null Materialverlust, null Spitzgefahr und null Handarbeit. Im Zusammenspiel mit der intelligenten Maschinensteuerung der Misch- und Dosieranlagen den Baureihen NODOPOX und TARDOSIL von TARTLER stellt die TAVA 200 D einen neuen Standard bei der Verarbeitung pastöser Polyurethan- und Epoxidharze sowie Silikone auf.
Mehr Informationen zur Tartler GmbH:
![]() |
TARTLER GmbH |
![]() |
Relystraße 48 |
![]() |
64720 Michelstadt |
![]() |
Tel.: 0049 (0) 60 61 / 96 72-0 |
![]() |
Fax: 0049 (0) 60 61 / 96 72-295 |
![]() |
E-Mail: u.tartler@tartler.com |
![]() |
www.tartler.com |
War dieser Artikel für Sie hilfreich?
![]() |
![]() |
![]() |
![]() |
![]() |
Bitte bewerten Sie diese Seite durch Klick auf die Symbole.
Zugriffe heute: 4 - gesamt: 4823.