Alle 40 Sekunden ist eine Baugruppe fertig
Abschirmteile für Abgasanlagen montieren
Auch wenn viele den Diesel schon fürtoterklärthaben: In die Herstellung dieser Antriebsart investiert die Automobilindustrie nach wie vor kräftig. Nicht umsonst hat der Sondermaschinenbauer MartinMechanic gerade eine Anlage fertiggestellt, mit der Abschirmteile für Abgasanlagen von Dieselfahrzeugen montiert und verschweißt werden. Mit der MCA211668 wird alle 40 Sekunden eine Baugruppe mit 200 Millimeter Länge produziert.
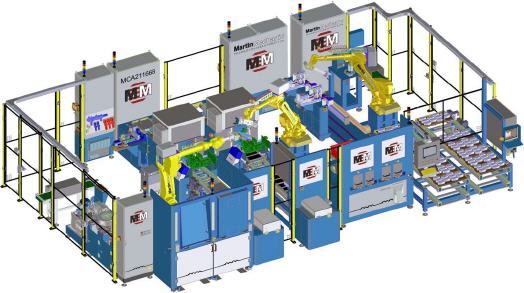
Diese Teile, die einen Durchmesser von 100 Millimeter haben, dienen der Direktisolierung der Abgasanlagen, die bei eingeschaltetem Motor sehr heiß werden. Mit der Isolation ist gewährleistet, dass wertvolle Wärmeenergie nicht verloren geht. Außerdem tragen die Abschirmteile zur Senkung der Emissionen bei und schützen als Schalldämpfer vor zu lauten Geräuschen. In der Mitte der Produktionsanlage wurde die Schweißstation des Kunden integriert, die die äußeren und innere Edelstahlhüllen miteinander verschweißt. Für den kompletten Arbeitsvorgangsind drei Industrieroboter von Fanuc im Einsatz. Produziert wird sortenrein.
Ein Werkstückträger, in den jeweils zehn Außenhülsen aus Edelstahl von Hand eingelegt werden, fährt über zwei Stauförderbänder in den ersten Teil der Arbeitszelle. Auf dem Bereitstellungsplatz wird anhand der Codierung durch einenTransponder zunächst überprüft, ob es sich um die richtigen Materialien handelt. Das gleiche passiert mit den Innenhülsen auf dem zweiten Transportband. Dann entnimmt der erste Fanuc-Roboter vom Typ M-710iC/50 mit seinem Doppelgreifer die beiden Hülsen, um sie in die sich drehende optische Messstation einzulegen.
Ein Laser misst die Außenmaße der Hülsen und übergibt die teilespezifischen Messdaten an die Steuerung der Anlage. Ist der Werkstückträger leer, fährt er automatisch auf die untere Ebene, wo ihn der Werker von Hand wieder entnimmt. Ein zweiter Roboter der gleichen Bauart legt temperaturbeständige Matten in die Wickelstationein. Hierfür werden die gestapelten Matten durch den Werker in vier Schubladen zur Verfügung gestellt. Sind die Schubladen voll, werden sie geschlossen.
Stimmt der dazugehörige Code mit der ausgewählten Bauvariante überein, wird die Produktion freigegeben, sodass der Roboter die erste Matte mit seinem Greifer entnehmen und auf die Mattenwaage legen kann. Bewegt sich das Gewicht der Matte innerhalb der vorgeschriebenen Spezifikation, entspricht sie den richtigen Maßenund es ist auch sichergestellt, dass es sich jeweils um nur eine Matte handelt –in diesem Fall 200 auf 250 Millimeter.
Der erste Roboter greift sich parallel zu diesem Arbeitsgang die Außen-und Innenhülsen. Nacheinander werden in der Wickelstation die erste Matte um die Innenhülse gelegt, die Außenhülse wiederum darübergestülpt und dann alles in eine zweite Matte gewickelt. Schließlich wird eine Kunststofffolie um die komplette Baugruppe gestretcht, damit sie nicht mehr auseinanderfallen kann. Die Folie wird zweifach verschweißt und der überstehende Rest abgetrennt.
Die Baugruppe wandert mithilfe des Roboters in die Schweißstation des Kunden, wo Innen-und Außenhülse miteinander verschweißt werden. Entsprechen Bauteile jedoch nicht den Qualitätskriterien des optischen Messsystems, werden sie über ein Transportband ausgeschleust. Möglich ist außerdem, komplette Baugruppen, die nicht weiter verschweißt werden sollen, ebenfalls über ein Staufördersystem manuell zu entnehmen.
Zurück zur Schweißstation: Die vollautomatische Beladetür gibt das Bauteil wieder frei. Jetzt kommt ein dritter Fanuc-Roboter vom Typ R-2000iB/175L zum Einsatz. Er presst die verschweißten Baugruppen hydraulisch in die vom Werker bereitgestellten Edelstahlschalen ein.
In der Nachdrückstation wird die Baugruppe lagerichtig positioniert. Anschließend werden die Enden der Schale gebogen, damit sich die Baugruppe nicht mehr bewegt, sodass ihr Durchmesser ordnungsgemäß kalibriert werden kann. Der Industrieroboter legt die Baugruppe in einer weiteren Station ab, wo sie mit einem Laser beschriftet wird. Ehe die fertige Baugruppe zur Prägestation befördert wird, wird ihr Datamatrix-Code gegengelesen. Die Teile, die wiederum nicht in Ordnung sind, werden über ein Austrageband ausgeschleust.
Nur die guten Baugruppen erhalten jetzt den Prägestempel des Herstellers und werden in den dafür bereitgestellten Gitterboxen mit Zwischenablagen abgelegt. Bis zu sechs Ebenen mit je 12 Baugruppen werden auf einer Palette übereinandergestapelt. Die Anlagentür öffnet sich automatisch, und der Werker kann die Paletten mit dem Hubwagen abtransportieren.
12Monate brauchten die Ingenieure von MartinMechanic, um die beiden Arbeitszellen zu entwickeln und auf die kundeneigene Schweißstationperfekt als Komplettanlage abzustimmen.
Das Herz derMCA211668 istdie SPS-Steuerung S7-1517F von Siemens. Praktischerweise kann das mobile, kabelgebundene Touchpanel KTP900an drei Stellen der umfangreichen Anlage eingesteckt werden.
Mehr Informationen zur Friedrich Martin GmbH:
![]() |
Friedrich Martin GmbH & Co KG |
![]() |
Hauptstrasse. 25 |
![]() |
72202 Nagold |
![]() |
Tel.: +49(0) 74 52-84 66-0 |
![]() |
Fax: +49(0) 74 52-84 66-5 66 |
![]() |
E-Mail: info@MartinMechanic.com |
![]() |
www.martinmechanic.com |
War dieser Artikel für Sie hilfreich?
![]() |
![]() |
![]() |
![]() |
![]() |
Bitte bewerten Sie diese Seite durch Klick auf die Symbole.
Zugriffe heute: 4 - gesamt: 4966.