Wärmerückgewinnung senkt Kosten
Effiziente Druckluftstation von Atlas Copco
Mehr Kundenzufriedenheit durch höhere Produktivität: Mit dem Einsatz neuer effizienterer Produktionstechnik am Hauptsitz in Schwabach kann die Apollo-Optik GmbH & Co. KG Kundenwünsche nun noch schneller erfüllen. Parallel zur Einführung der neuen Fertigungsanlagen entschieden sich die Schwabacher für ein Druckluftkonzept von Atlas Copco, das allen Anforderungen in puncto Effizienz, Flexibilität und Service genügt.
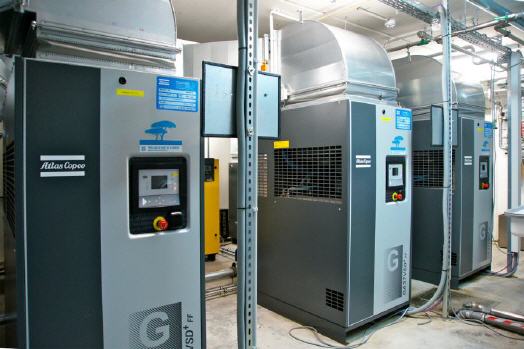
Durchblick im Minutentakt: Seit die Apollo-Optik ihre Produktionsanlagen am Hauptsitz in Schwabach komplett modernisiert hat, kommen die fertigen Brillen noch schneller zu den Kunden der Optiker-Kette. Gerade mal 60 Sekunden benötigen die neuen Fräsautomaten für die vollautomatische, hochpräzise Formgebung eines Brillenglases. Seit Anfang 2015 arbeiten in Schwabach insgesamt zwölf dieser Maschinen in zwei Linien rund um die Uhr, an fünf Tagen in der Woche.
„Unsere Produktivität ist seitdem signifikant gestiegen“, erklärt Oliver Knapp, Direktor Supply Chain bei Apollo-Optik in Schwabach. „Früher, als hier noch ausschließlich halbautomatische Schleifmaschinen liefen, haben wir acht Minuten für die Bearbeitung eines Glases gebraucht. Jetzt geht das fast zehn Mal so schnell.“ Diese Verbesserung erhöhe die Kundenzufriedenheit in den rund 800 Apollo-Filialen in Deutschland sowie in den etwa 100 Geschäften der österreichischen Pearle-Kette, deren Aufträge ebenfalls in Schwabach gefertigt werden.
„Fertigung bedeutet bei uns, dass die gewünschten Gläser gemäß der individuellen Kundendaten an die Form der gewählten Fassung angepasst werden“, sagt Knapp. „Diesen Prozess nennen wir Formrandung.“ Die eintreffenden Gestelle, Gläser und Datenblätter erhalten dafür zunächst einen Barcode und gelangen dann in ein vollautomatisiertes Zwischenlager, das sogenannte „Hotel“. Wenn alle Bestandteile der Brille komplett vorliegen, werden diese auf einem Warenträger angeordnet und erreichen über Förderbänder die Fräsautomaten. Dort liest die Maschine den Barcode ein, zentriert die Gläser automatisch und fixiert sie mittels Vakuum. Im Anschluss startet der formgebende Fräsprozess. Montiert werden Gestell und Gläser dann entweder in einer eigenen Optiker-Abteilung in Schwabach oder in den Filialen vor Ort.
Druckluftbedarf hat sich verdreifacht
Gemeinsam mit der neuen Produktionstechnik haben die Schwabacher auch ihre Druckluftversorgung komplett erneuert. „Durch den Ausbau des Maschinenparks ist unser Druckluftbedarf natürlich immens nach oben gegangen“, erläutert der Technische Leiter, Volkan Koz. „Von fünf bis sechs Kubikmetern pro Minute hat sich der Verbrauch in etwa verdreifacht auf 17 bis 18 Kubikmeter. Diese Menge müssen wir in der erforderlichen Qualität sicherstellen – und das natürlich möglichst effizient und kostengünstig.“
Die Fräsautomaten benötigen Druckluft unter anderem für die Vakuumerzeugung, zum Abblasen von Kunststoffstaub und für den Betrieb der Pneumatikzylinder. Jede Maschine zieht etwa 800 Liter Druckluft pro Minute. Entsprechend hoch sind die Bedarfsschwankungen, wenn einmal nicht alle Maschinen laufen. „Die Schwankungen liegen zwischen sieben und 17 Kubikmetern pro Minute“, rechnet Volkan Koz. „Das führt bei reinen Volllast-Leerlauf-Kompressoren zu hohen Energieverlusten. Daher haben wir uns bei der Konzeption unserer neuen Druckluftversorgung für drehzahlgeregelte Kompressoren entschieden.“
Drehzahlregelung garantiert Effizienz bei schwankendem Bedarf
In der Druckluftstation arbeiten drei öleingespritzte Schraubenkompressoren des Typs GA 37 VSD+ FF von Atlas Copco. VSD steht für „Variable Speed Drive“, das heißt, die Motordrehzahl wird exakt dem Luftbedarf anpasst. Bei der FF-Version (Full Feature) sind ab Werk Kältetrockner, Druckluftfilter, Kondensatableiter und -trenner sowie alle Komponenten für eine Wärmerückgewinnung in das Kompressorgehäuse integriert. Eine nachgeschaltete Kombination aus Hochleistungsvorfiltern der Typen DD/PD, einem Aktivkohlefilter QDT und einem PDP-Staubfilter von Atlas Copco stellt sicher, dass die Druckluft gemäß ISO 8573-1:2010 Klasse 1 technisch ölfrei ist.
Die drei neuen Kompressoren von Atlas Copco arbeiten mit drei Kompressoren mit fester Drehzahl eines Wettbewerbers zusammen, die bereits aus der Zeit vor dem Umbau stammen. Den unteren Lastbereich decken zwei der Bestandsmaschinen ab. Je nach Bedarf schalten sich dann ein oder zwei GA-Kompressoren hinzu. Die jeweils dritten Kompressoren stehen als Redundanz zur Verfügung. Gesteuert werden alle Kompressoren zentral von einem übergeordneten ES-Energiesparsystem von Atlas Copco. Dieses koordiniert die Maschinen so, dass sie möglichst immer an ihrem optimalen Betriebspunkt laufen.
„Mittlerweile arbeiten wir in einem Druckband von 7,4 bis 8,4 bar, früher haben wir 9,5 bar gebraucht“, berichtet Volkan Koz. „Wir konnten den Betriebsdruck mit der neuen Anlage also um zwei bar senken.“ Rechnet man hier mit der Faustformel, die von 6 bis 7 % geringeren Energiekosten pro Bar ausgeht, konnte Apollo-Optik seinen Stromverbrauch allein durch diese Maßnahme um mehr als 10 % reduzieren. Was das Unternehmen absolut durch die neue Anlage an Druckluft einsparen kann, ist hingegen nicht exakt zu kalkulieren. „Da wir zusammen mit der Druckluft auch die Produktion komplett umgebaut haben, kann ich momentan noch keine Aussage bezüglich der Wirtschaftlichkeit der neuen Anlage machen“, sagt Volkan Koz.
Effizienzkontrolle mit SmartLink Energy
„Ich bin aber überzeugt davon, dass wir hinsichtlich der Energieeffizienz bei der Drucklufterzeugung und Aufbereitung den richtigen Schritt getan haben. Und selbstverständlich überprüfe ich regelmäßig die Leistungsdaten – unter anderem mit dem Überwachungssystem SmartLink Energy von Atlas Copco.“ Damit lassen sich alle Effizienzparameter einfach und kontinuierlich verfolgen. Volkan Koz‘ Abteilung Technik kann zu jeder Zeit den Verbrauch abfragen und sieht, wie sich der Verbrauchstrend im Unternehmen entwickelt.
Detaillierte Analysen helfen, Effizienzsteigerungen sichtbar zu machen. Die Ergebnisse des Monitorings sind auf dem SmartLink-Portal von Atlas Copco einsehbar und können als Excel-Tabelle, als Grafik oder als kompletter technischer Bericht exportiert werden. Darüber hinaus kontrolliert das System die verbleibende Zeit bis zum nächsten Servicetermin, übernimmt die komplette Überwachung der Druckluftstation und schickt im Notfall eine Warnmeldung per E-Mail oder SMS auf das (mobile) Endgerät des verantwortlichen Technikers.
„Ich wollte die Effizienz der Kompressoren kontrollieren können“, begründet Volkan Koz seine Entscheidung für den zusätzlichen Service von Atlas Copco. „Momentan kann ich den Verbrauch zwar nur ablesen, aber im Laufe eines Jahres ist dann auch ein Vergleich möglich. Außerdem erhalte ich automatisch die Verbrauchskurven der Kompressoren.“ Dadurch habe sein Team beispielsweise entdeckt, dass es Leckagen im System gibt. Das sei deutlich geworden, weil Samstag und Sonntag die Kompressoren auf geringem Niveau liefen. „Wir brauchen da zwar ganz geringe Mengen an Druckluft für die Wasseraufbereitung“, erläutert Volkan Koz, „aber der gemessene Verbrauch lag deutlich höher.“
Die Beseitigung der Leckagen wird sich künftig ebenso positiv auf den Energieverbrauch auswirken wie die seit April 2015 installierte Wärmerückgewinnung der drei neuen Kompressoren. „Da wir bereits eine Wärmerückgewinnung für die Bestands-Kompressoren hatten, war die komplette Infrastruktur vorhanden“, erklärt Volkan Koz. „Deshalb haben wir auch alle neuen Kompressoren mit integrierter Wärmerückgewinnung bestellt. Über die Plattenwärmetauscher erhalten wir im Sekundärkreislauf etwa 70 Grad Celsius heißes Wasser, das wir in den Rücklauf unseres Heizungssystems einspeisen.“ Die resultierenden Einsparungen könne man momentan noch nicht genau erfassen. „Aber in unseren Hochrechnungen gehen wir von jährlich 6000 bis 7000 Euro weniger Heizkosten aus, so dass sich die Wärmerückgewinnung in zwei bis drei Jahren amortisiert haben wird“, prognostiziert Volkan Koz.
Atlas Copco punktet mit flexibler Komplettlösung
Dass Atlas Copco bei der Ausschreibung für die neue Kompressoren-Station der Schwabacher punkten konnte, liegt an der ebenso effizienten wie flexiblen Komplettlösung, die exakt den Bedürfnissen des Kunden entsprach. „Das Ausschlaggebende war, dass Atlas Copco unser Konzept eins zu eins umsetzen konnte“, lobt Koz. „Unsere Fertigung und Druckluftversorgung sind so aufgebaut, dass sie auch variabel an anderen Orten eingesetzt werden können. Wir können die zwei neuen Linien und die drei GAs abbauen und woanders wieder aufbauen. Mit diesem Konzept hat uns Atlas Copco überzeugt.“ Auch energetisch gesehen habe die Druckluftanlage den Anforderungen entsprochen. Ein wichtiger Aspekt, da die Geschäftsführung im Unternehmen sehr großen Wert auf Energieeffizienz und Nachhaltigkeit lege.
Da das Druckluftkonzept auch hinsichtlich des Aufbaus flexibel sein sollte, konnten die neuen Kompressoren problemlos bei laufendem Betrieb installiert werden, ohne die Bestandssituation zu verändern. „Vor sechs Jahren haben wir unser komplettes Leitungsnetz saniert und in der Produktion eine Ringleitung installiert“, erläutert Koz. „Damals haben wir bereits die komplette Infrastruktur so aufgebaut, dass der jetzige Umbau problemlos möglich war. Aufgrund des höheren Volumenstroms mussten wir die Druckluftleitungen bis zum Übergabepunkt an der Ringleitung vergrößern – ansonsten waren keine Änderungen erforderlich.“
Für fünf Jahre rundum sorglos bezüglich Wartung und Garantie
Auch in puncto Service und Wartung vertraut man in Schwabach auf die Erfahrungen von Atlas Copco. Mit dem Kauf der neuen Anlage hat sich Volkan Koz gleichzeitig für das neue Angebot Xtended Warranty+ der Essener entschieden. Dieses „Rundum-sorglos-Paket“ umfasst nicht nur alle Service- und Wartungsleistungen für die Druckluftanlage, sondern ist darüber hinaus mit einer auf fünf Jahre verlängerten Garantie für die Maschinen verbunden. „So bin ich sicher, dass fünf Jahre lang nichts passieren kann“, erklärt Volkan Koz. „Und wenn es mal Probleme geben sollte, werden diese von Atlas Copco kostenlos behoben. Ich sehe mich als Dienstleister der Produktion, und die muss laufen. Denn der Fokus von Apollo-Optik liegt auf der Kundenzufriedenheit, und wenn die Produktion stillsteht, ist der Kunde nicht zufrieden.“
Mehr Informationen zu Atlas Copco:
![]() |
Atlas Copco Deutschland |
![]() |
Langemarckstr. 35 |
![]() |
D-45141 Essen |
![]() |
Tel.: +49 (0)201 21 77 0 |
![]() |
Fax: +49 (0)201-2177-100 |
![]() |
E-Mail: atlascopco.deutschland@de.atlascopco.com |
![]() |
www.atlascopco.de |
![]() |
------------------------------------------------------ |
![]() |
Handwerkzeuge: |
![]() |
Atlas Copco Tools Central Europe GmbH |
![]() |
Langemarckstr. 35 |
![]() |
D-45141 Essen |
![]() |
Tel.: +49 (0)201 21 77 0 |
![]() |
E-Mail: tools.de@atlascopco.com |
![]() |
www.atlascopco.com/de-de/itba |
War dieser Artikel für Sie hilfreich?
![]() |
![]() |
![]() |
![]() |
![]() |
Bitte bewerten Sie diese Seite durch Klick auf die Symbole.
Zugriffe heute: 5 - gesamt: 5718.